Here is a situation I have not had very often:
Notice the "FAIL" due to uplift at the support 3. What would be the best resolution? Cut the beam at support 2 or design the connection and post at 3 for the uplift?
I kind of like keeping the beam in one piece to maintain my lateral continuity.
A confused student is a good student.
Nathaniel P. Wilkerson, PE
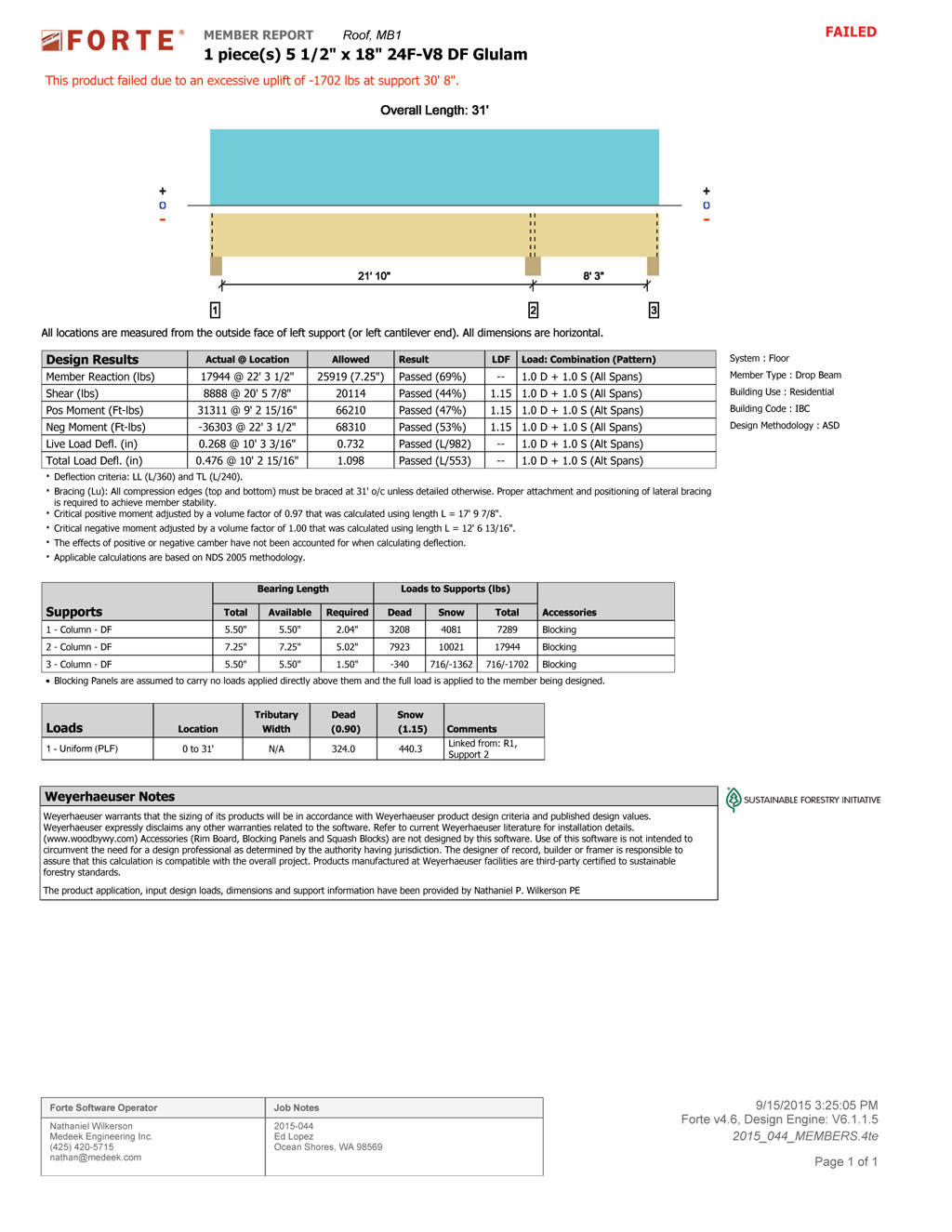
Notice the "FAIL" due to uplift at the support 3. What would be the best resolution? Cut the beam at support 2 or design the connection and post at 3 for the uplift?
I kind of like keeping the beam in one piece to maintain my lateral continuity.
A confused student is a good student.
Nathaniel P. Wilkerson, PE