Please take a look at the attached image from the Steel Stud Mfrs Assoc. - the question is: if a boxed header is chosen from the table, does it come "off the truck" pre-manufactured with NO seam welds/cap & screws required to be specified by the EOR? I'll withhold my thought briefly. Thanks
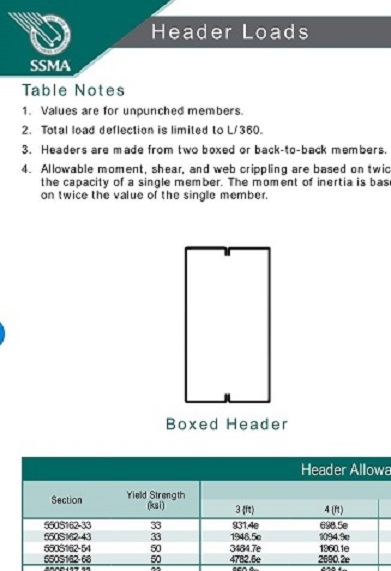