asalisbury
Mechanical
- Mar 6, 2024
- 13
I am working on determining if I have any lateral torsional buckling in this beam. I can't really find any equations for this specific scenario so any help or pointers would be appreciated. It's a very thin and long metal beam that is getting loaded on each end with 5,000lbs. It is pressing into a simple support that covers most of the beams span.
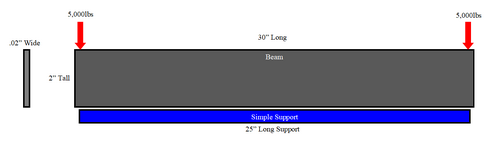
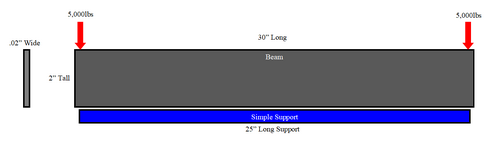