Mandrill22
Mechanical
I have a bar linkage system that ends up being a sort of 4 bar linkage. There are 2 bars running in parallel on either side of the "joints".
Each joint has a shaft with a bushing, with an H7/h7 fit.
My question is if there is an equation to determine what the tolerance would need to be from hole-to-hole on each bar.
Images attached.
Each joint has a shaft with a bushing, with an H7/h7 fit.
My question is if there is an equation to determine what the tolerance would need to be from hole-to-hole on each bar.
Images attached.
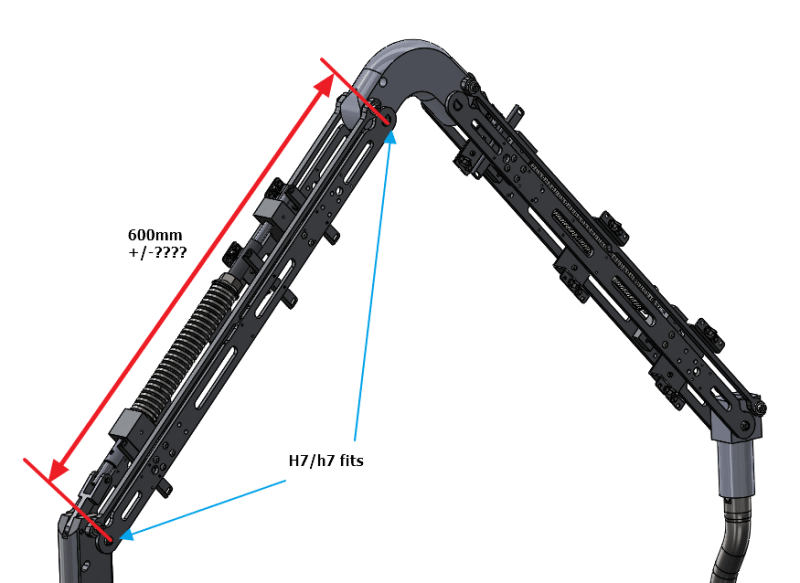
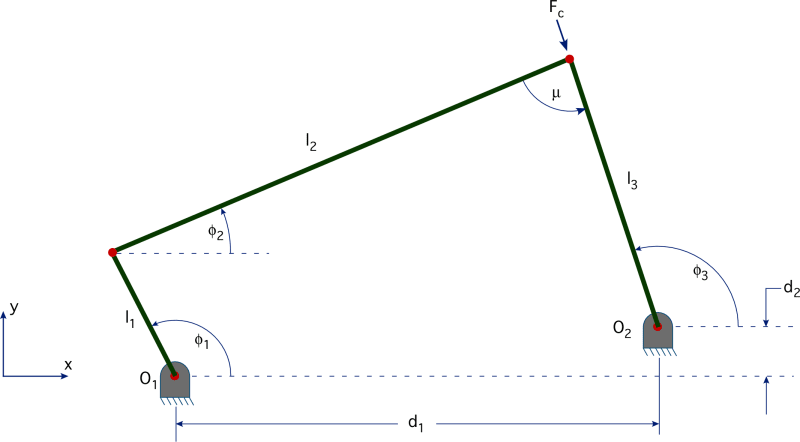