I've some concerns about a suggested modification to an existing liquid starter during a planned maintenance program.
The company performing the overhaul are proposing to insulate the moving electrodes from earth (other that the resistance through the electrolyte)
Existing
Proposed
We have five liquid starters and have been in operation since circa. 1970 without and significant issues. The original manufactures (Allen West) documentation Leaflet 909/A/3 that states “Neutral or Star point is earthed, so that the rotor slip rings must be insulated from earth” In this case the motor winding are insulated from earth.
MOTOR DETAILS
MANUFACTURER Harland and Wolff
TYPE Slip Ring Induction
OUTPUT 1200
RATED SPEED 1480
RATED VOLTAGE 6600
RATED CURRENT 91
PHASE 3
FREQUENCY 50
POLES 4
CONNECTION Y
ROTOR S.R.
ROTOR VOLTS 1310
ROTOR CURRENT 418
INSULATION CLASS B
FRAME A40/60
STANDARD BS 2613
LIQUID STARTER DETAILS
The motor operated Liquid Starters were manufactured by Allen West & Co Ltd, Brighton, model TS5.
Each Liquid Starter is controlled via existing relay and timer logic implemented within the pump-house control console and respective MV motor starter.
Each of the units have been subject to periodic checking and adjustment of electrolyte level and concentration.
My question being, that if the star point is insulated from earth what happen if we lose a rotor winding and the circuit goes out of balance? Is this potentially dangerous?
The company performing the overhaul are proposing to insulate the moving electrodes from earth (other that the resistance through the electrolyte)
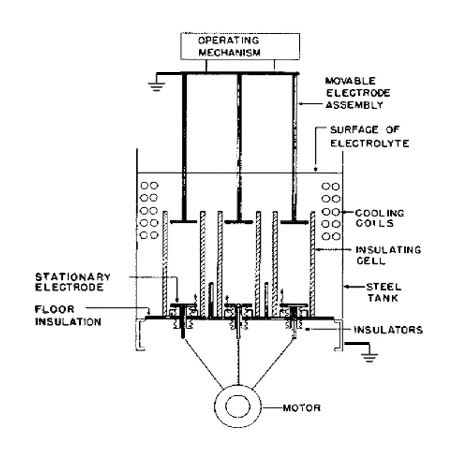
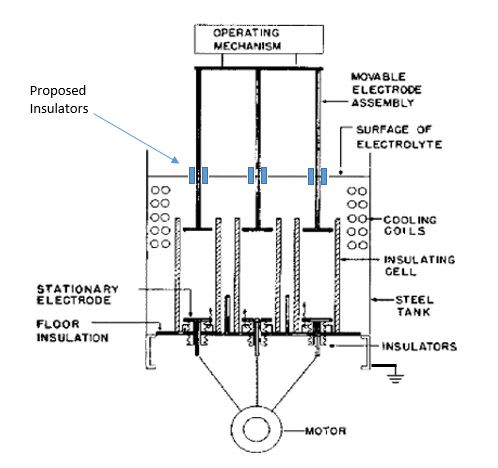
We have five liquid starters and have been in operation since circa. 1970 without and significant issues. The original manufactures (Allen West) documentation Leaflet 909/A/3 that states “Neutral or Star point is earthed, so that the rotor slip rings must be insulated from earth” In this case the motor winding are insulated from earth.
MOTOR DETAILS
MANUFACTURER Harland and Wolff
TYPE Slip Ring Induction
OUTPUT 1200
RATED SPEED 1480
RATED VOLTAGE 6600
RATED CURRENT 91
PHASE 3
FREQUENCY 50
POLES 4
CONNECTION Y
ROTOR S.R.
ROTOR VOLTS 1310
ROTOR CURRENT 418
INSULATION CLASS B
FRAME A40/60
STANDARD BS 2613
LIQUID STARTER DETAILS
The motor operated Liquid Starters were manufactured by Allen West & Co Ltd, Brighton, model TS5.
Each Liquid Starter is controlled via existing relay and timer logic implemented within the pump-house control console and respective MV motor starter.
Each of the units have been subject to periodic checking and adjustment of electrolyte level and concentration.
My question being, that if the star point is insulated from earth what happen if we lose a rotor winding and the circuit goes out of balance? Is this potentially dangerous?