I have a customer who wants to reduce the speed of a large grinder. He wants to use a VFD to drop the speed about 20%. They're grinding ceramics so there is fairly low torque involved, usually something on the order of 10% of what the machine was designed for. In my opinion this does make this a reasonable candidate for VFD slowing.
My question is that the 25hp 60Hz 220V 50 year old motor has a plate that reads:
With these innards.
It states 720RPM which means @60Hz that we're talking about a 10 pole motor.
1) Will a typical VFD stoop to this many poles?
2) Isn't 720RPM the synchronous speed?? Does that make this a synchronous motor? Is that a problem?
Keith Cress
kcress -
My question is that the 25hp 60Hz 220V 50 year old motor has a plate that reads:
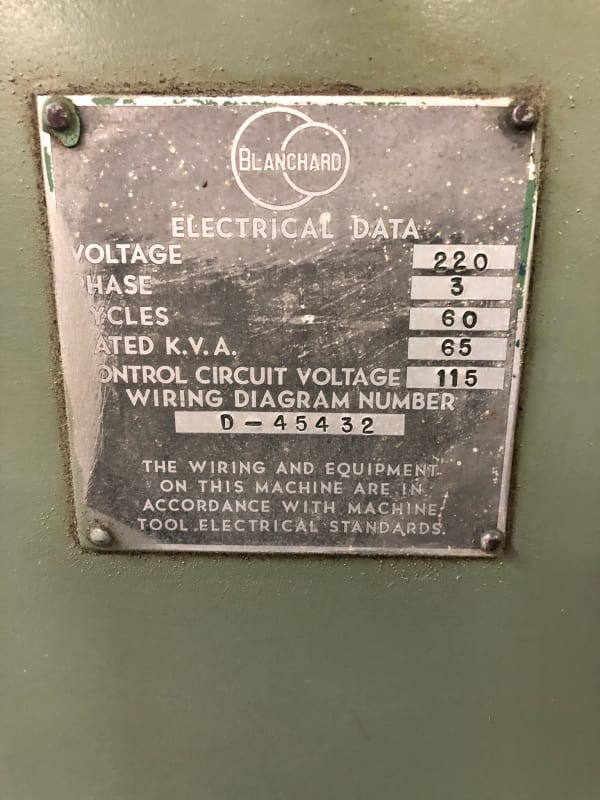
With these innards.
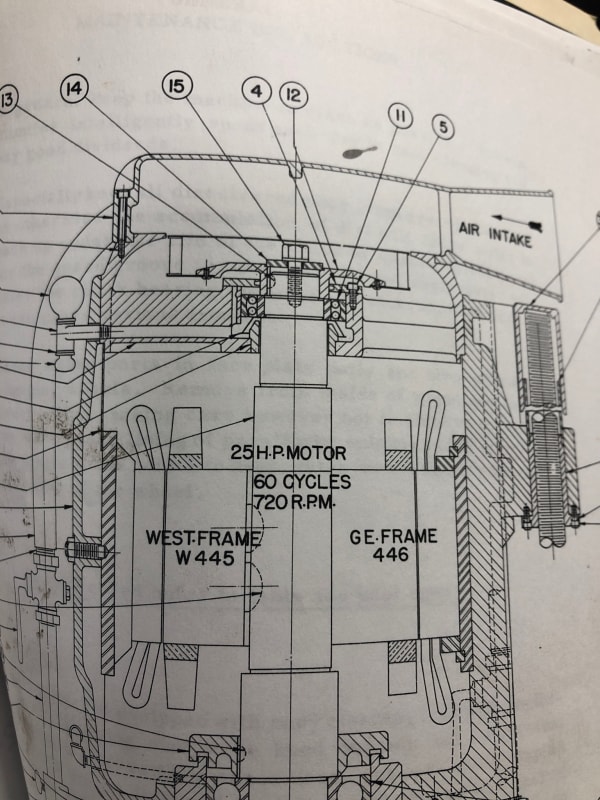
It states 720RPM which means @60Hz that we're talking about a 10 pole motor.
1) Will a typical VFD stoop to this many poles?
2) Isn't 720RPM the synchronous speed?? Does that make this a synchronous motor? Is that a problem?
Keith Cress
kcress -