Yao Lingbo
Civil/Environmental
- Jan 16, 2025
- 1

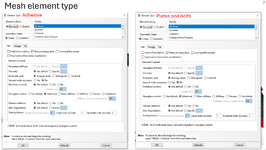
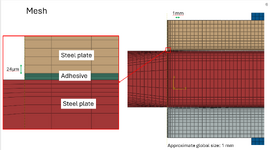
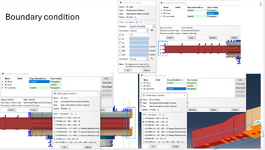
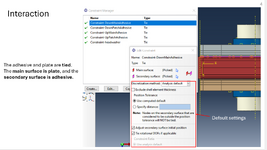
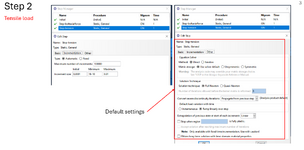
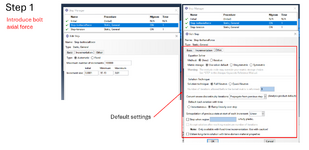
For the analysis, I set two Static, General step with Nlgeom enabled.
However, due to the large difference in Young's modulus between the steel plates (206,000 MPa) and the adhesive (approximately 3,100 MPa), I suspect that the adhesive layer undergoes significant deformation when subjected to both the bolt axial force and the tensile load. As a result, the analysis is interrupted at the first step (introducing the bolt axial force) due to large deformations.
This issue has been troubling me for several months. Could you provide advice on how to solve this problem?
Thank you very much for your assistance
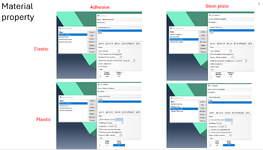