elinah34
Mechanical
- Aug 19, 2014
- 145
Hello,
This is the first time I draw a modular profile (item) construction. What type of tolerances (and values range) is acceptable and reasonable?
I guess that size tolerances are OK, but what about the required precision?
If I want profiles to be parallel to each other, can I require it and on the same time avoid "no bid" by manufacturers?
I am very experienced in machining and know what precisiona can be achieved, but in this case (assembled modular profiles) I am not sure what and how can be achieved.
I am adding pictures for illustration.
![image029[1222].png image029[1222].png](https://www.eng-tips.com/data/attachments/5/5105-1722280cfe273ccfde29dedd519f5467.jpg)
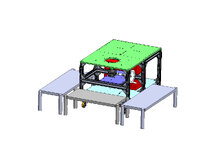
This is the first time I draw a modular profile (item) construction. What type of tolerances (and values range) is acceptable and reasonable?
I guess that size tolerances are OK, but what about the required precision?
If I want profiles to be parallel to each other, can I require it and on the same time avoid "no bid" by manufacturers?
I am very experienced in machining and know what precisiona can be achieved, but in this case (assembled modular profiles) I am not sure what and how can be achieved.
I am adding pictures for illustration.
![image029[1222].png image029[1222].png](https://www.eng-tips.com/data/attachments/5/5105-1722280cfe273ccfde29dedd519f5467.jpg)
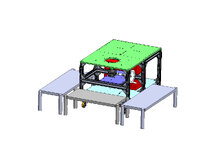
Last edited: