bdn2004
Electrical
- Jan 27, 2007
- 792
Inside this panel a single 300A fuse blows up and then catches on fire. The fuses upstream did not blow, neither did the adjacent fuses in the panel. The panel remained energized throughout the whole episode. This feeds an infrared heating system. Any ideas on WHY something like this could happen? And why didn't the fuse just open - instead blowing up ?
The fuse manufacturer was contacted and they said that fuses at low overload currents have trouble opening. They also said it could be there was a solder problem on the fuse or there could be sand fill issues that could cause internal arcing especially in the 600A range of overload.
Any thoughts? Has anyone seen anything like this before? What were your conclusions and things you did to remedy or see that it could not happen again ?
The fuse manufacturer was contacted and they said that fuses at low overload currents have trouble opening. They also said it could be there was a solder problem on the fuse or there could be sand fill issues that could cause internal arcing especially in the 600A range of overload.
Any thoughts? Has anyone seen anything like this before? What were your conclusions and things you did to remedy or see that it could not happen again ?
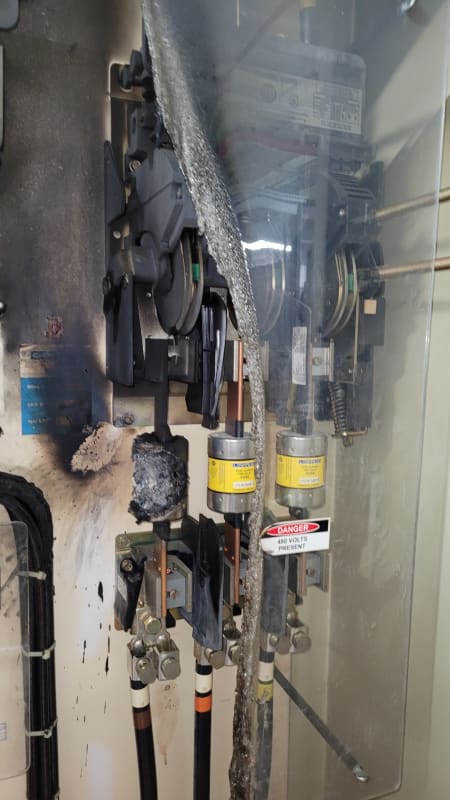