gearcutter
Industrial
- May 11, 2005
- 683
Interesting summary of a yet-to-be-released report into the cause of an engine shut-down on an A330 while flying over Australia.
So far it appears like there's been an oil pump failure due to damage sustained to the drive shaft.
Looking at the picture of the failed shaft; I'm somewhat surprised at how it has been designed. Perhaps the undercut between the spline and bearing diameter is some kind of inherently designed shear point.
So far it appears like there's been an oil pump failure due to damage sustained to the drive shaft.
Looking at the picture of the failed shaft; I'm somewhat surprised at how it has been designed. Perhaps the undercut between the spline and bearing diameter is some kind of inherently designed shear point.
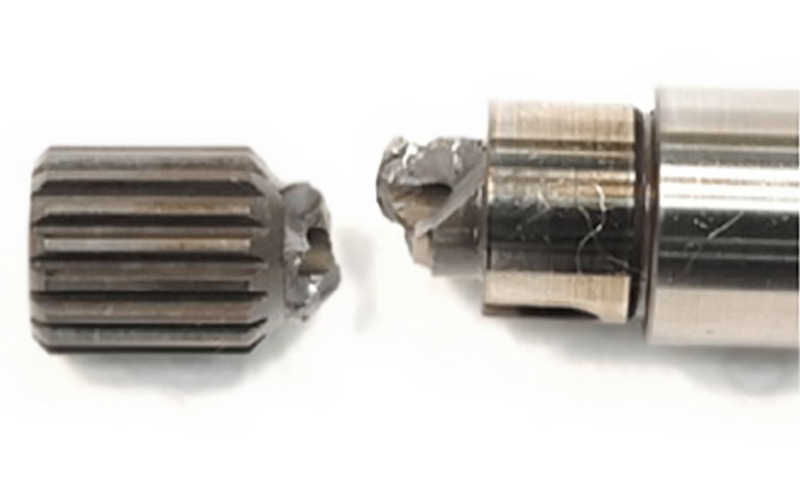