Entherm
Civil/Environmental
- Sep 23, 2020
- 34
In the ABAQUS, my member is a beam 127.5625 in. long with a uniform rectangular cross-section of 3.5 in2. I input a bilinear steel property with true stress of 42.06 ksi, plastic strain 0, and ultimate true stress of 72 ksi and plastic strain 0.18. This came from a yield point of 42 ksi and ultimate stress of 65 ksi.
When I applied a compressive load of 250 kips, I, however, get the following force-displacement curve. Based on the area and yield point, my yield force would be 147 kips and the ultimate point of 227 kips. The axial displacement from ABAQUS does not seem to comply with this. Can I get help on what might be happening?
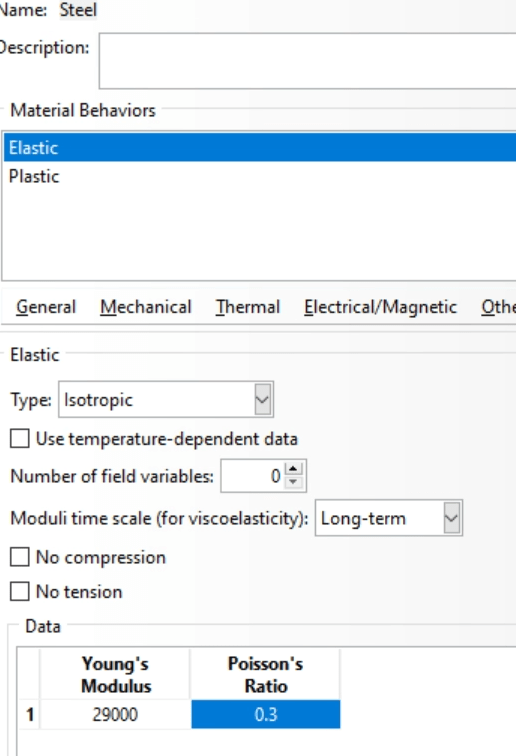
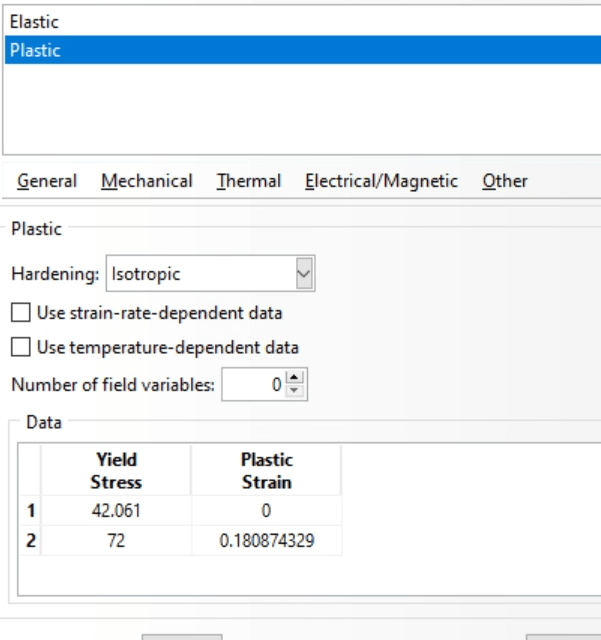
When I applied a compressive load of 250 kips, I, however, get the following force-displacement curve. Based on the area and yield point, my yield force would be 147 kips and the ultimate point of 227 kips. The axial displacement from ABAQUS does not seem to comply with this. Can I get help on what might be happening?
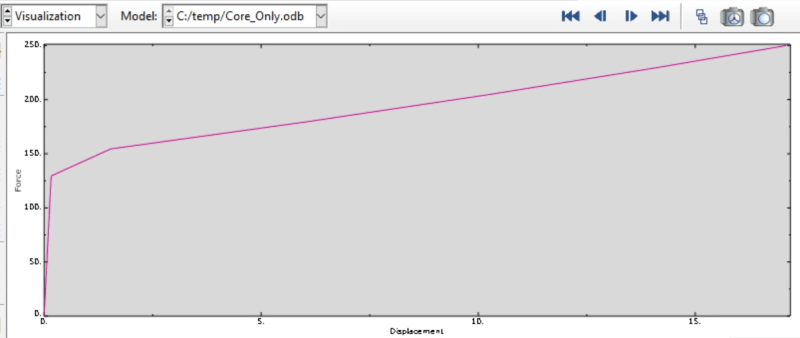