Hi everyone,
I'm trying to simulate a coining process with microgeometry with 0.2mm in the width relief, and I noticed some poor aspect in the final form of the coin. The Figure 1 shows a quarter of the coin and a bad appearance in the contour of the relief with bright spots.
The figure 2 gives a zoom on a local width of the relief where we can see the distortion of the elements in a way that doesn’t seem normal.
I’ve tried different parameters to improve the quality, such as: refining the mesh of the blank, refining the mesh of the punch, rounding sharp corners, reducing mass scaling and time scaling, changing the hourglass control method, choosing different contact approach (general contact and contact pairs), removing friction or inserting a maximum shear stress, but nothing seemed to work efficient.
Any suggestion on what I should try?
Below is some information about my model:
- Dynamic Explicit Analyses;
- ALE activated with different frequencies and sweep;
- Rigid punch;
- Deformable blank with hexaedral elements and reduced integration;
- Hourglass control: Enhanced or Default;
I'm trying to simulate a coining process with microgeometry with 0.2mm in the width relief, and I noticed some poor aspect in the final form of the coin. The Figure 1 shows a quarter of the coin and a bad appearance in the contour of the relief with bright spots.
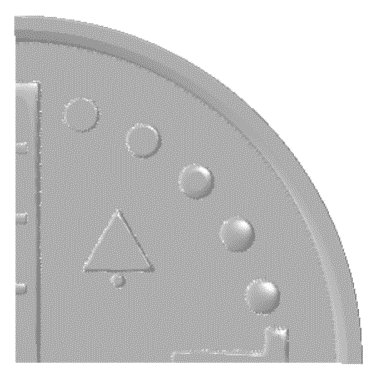
The figure 2 gives a zoom on a local width of the relief where we can see the distortion of the elements in a way that doesn’t seem normal.
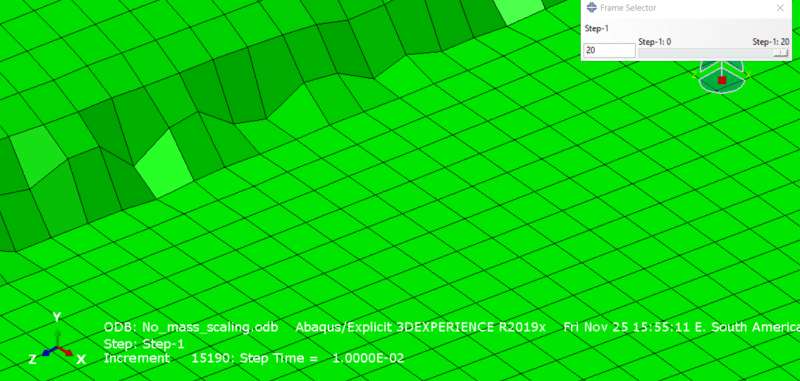
I’ve tried different parameters to improve the quality, such as: refining the mesh of the blank, refining the mesh of the punch, rounding sharp corners, reducing mass scaling and time scaling, changing the hourglass control method, choosing different contact approach (general contact and contact pairs), removing friction or inserting a maximum shear stress, but nothing seemed to work efficient.
Any suggestion on what I should try?
Below is some information about my model:
- Dynamic Explicit Analyses;
- ALE activated with different frequencies and sweep;
- Rigid punch;
- Deformable blank with hexaedral elements and reduced integration;
- Hourglass control: Enhanced or Default;