Hello everyone !
We are trying to complete one tour track with our fsae model for bachelor project. We design just front suspension and build and assembly with fsae_2018 template. I have a few question that we can't achieve anthying.
1) As you can see in our model, we think there is a problem with anti-roll bar and rocker joint. Can you help us ?
2) With these configurations in Smart-driver;
We have a problem with cornering in the last-corner.
-------------------------------------------------------------------------------
| Model Title |
|=============================================================================|
| |
| Adams Car Assembly (Adams 2019.2) |
| |
-------------------------------------------------------------------------------
command: !
command: !INFO Adams Version: Adams 2019.2
command: !INFO Adams Build: 2019.2.0-CL661333
command: !INFO Assembly File: <alulantekardene>/assemblies.tbl/fsae_full_vehicle.asy
command: !INFO Solver Library: C:/PROGRA~1/MSC~1.SOF/Adams/2019_2/win64/acar_solver.dll
command: !
command: string/5, string=exp4_smart_driver.xml
command: preferences/solver=CXX
command: preferences/list,status=on
PREFERENCES:
SIMFAIL = NOSTOPCF
Contact Geometry Library = (not loaded)
Thread Count = 1
Library Search Path = Not Set
Status Message = On
Solverbias = CXX (C++ Solver)
command: control/routine=abgTire::con901,func=user(901,85,98,104,1,2)
command: control/routine=abgTire::con901,func=user(901,89,99,105,1,4)
command: control/routine=abgTire::con901,func=user(901,94,107,113,1,6)
command: control/routine=abgTire::con901,func=user(901,98,108,114,1,8)
command: output/nosep
command: control/routine=abgVDM::EventInit, function=user(5,1,8,0,3,6,6,17)
vdm::EvtMonitor::EvtMonitor
End conditions evaluated in SENSUB.
ASD_vfSet_Globals()
=================================================================
Adams Smartdriver
Version Adams 2019.2
=================================================================
Using SmartDriver Template file:
C:\Program Files\MSC.Software\Adams\2019_2\win64/.smartdriver.xml
SDF_xml_upd_controller()
Info: minPreviewDistance is negative or not set, using default 5m.
Drv_Model::vfSetMaxLenItx
Info: MaxLenItx is negative or not set, using default (100m).
SDF_xml_upd_mini()
Max. Drive Accel = 50
Max. Brake Accel = 50
Max. LatAcc Left = 5
Max. LatAcc Right = 5
Geo_DCurve::ifFit_BSpline()
Info: Fitting BSplines with iOrder = 4, Closed = 0 and iNP = 1351.
SmartDriver: preparing speed profile using:
TYR900 -> Pacejka 89 Tire Model
TYR900 -> Pacejka 89 Tire Model
Road3D::vfPreprocessRoad : Road is flat (all banks same, all slopes same), short-cuts will be taken.
Road3D::vfPreprocessRoad : Road is flat (all banks same, all slopes same), short-cuts will be taken.
TYR900 -> Pacejka 89 Tire Model
TYR900 -> Pacejka 89 Tire Model
Road3D::vfPreprocessRoad : Road is flat (all banks same, all slopes same), short-cuts will be taken.
SDBrain::vfCalc()
Info: Begin Speed Profile Calculation
Info: End Speed Profile Calculation
Drv_Core::ifSDBpre
AutoAccX is FALSE.
Static Set-up solution may be inconsistent with target at t=0.
Setting Longitudinal Setup Type to NONE.
command: control/routine=abgVDM::EventRunAll, function=user(0)
fdm::ActJoiMot
Setting function on: steering::steering_wheel_angle
command: MOTION/4, FUNCTION=0.0
command: SFORCE/1, FUNCTION=0.0
fdm::ActVar
Connecting: steering::steering_wheel_angle
To : driver_demand::steering
fdm::ActVar
Setting function on: driver_demand::steering
command: VARIABLE/92, FUNCTION=AZ(683,891)
command: DEACTIVATE/SFORCE, ID=4
Deactivated model.testrig.jfs_steering_rack_force.force, force/torque values will be zero in function-expression references.
command: DEACTIVATE/SFORCE, ID=5
Deactivated model.testrig.jfs_steering_rack_force.force_j, force/torque values will be zero in function-expression references.
command: DEACTIVATE/MOTION, ID=3
Deactivated model.testrig.jms_steering_rack_travel.motion, force/torque values will be zero in function-expression references.
command: DEACTIVATE/MOTION, ID=4
Deactivated model.testrig.jms_steering_wheel_angle.motion, force/torque values will be zero in function-expression references.
fdm::ActJoiFor
Setting function on: steering::steering_wheel_torque
command: SFORCE/2, FUNCTION=DIF(4)
fdm::ActVar
Setting function on: driver_demand::throttle
command: VARIABLE/94, FUNCTION=USER(976,3)\ ROUTINE=abgVDM::var976
fdm::ActVar
Setting function on: driver_demand::brake
command: VARIABLE/96, FUNCTION=USER(975,3)\ ROUTINE=abgVDM::var975
fdm::ActVar
Setting function on: driver_demand::gear
command: VARIABLE/98, FUNCTION=(6.0)
fdm::ActVar
Setting function on: driver_demand::clutch
command: VARIABLE/100, FUNCTION=0.0
vdm::SteadyState::MiniInfo
Static Task : 'Straight'
Lon. Acceleration : 0.000 [m/s^2]
Initial Velocity : 16.667 [m/s]
Perform Linear : No
Include Damping : Yes
Halt on Failure : Yes
fdm::ActVar
Setting function on: driver_demand::clutch
command: VARIABLE/100, FUNCTION=1.0
command: ACTIVATE/MOTION,ID=4
command: SIM/STAT
Begin Static Solution
TIRE ID: 2
TYR900 -> Pacejka 89 Tire Model
Using 3D Spline Road
One point Contact
3D Spline road C:/Program Files/MSC.Software/Adams/2019_2/acar/shared_car_database.cdb/roads.tbl/3d_road_smooth_track.xml
Removing overlapping points:
Removing point: 1351 0.000000 0.000000 0.000000
TIRE ID: 4
TYR900 -> Pacejka 89 Tire Model
Using 3D Spline Road
One point Contact
3D Spline road C:/Program Files/MSC.Software/Adams/2019_2/acar/shared_car_database.cdb/roads.tbl/3d_road_smooth_track.xml
Removing overlapping points:
Removing point: 1351 0.000000 0.000000 0.000000
TIRE ID: 6
TYR900 -> Pacejka 89 Tire Model
Using 3D Spline Road
One point Contact
3D Spline road C:/Program Files/MSC.Software/Adams/2019_2/acar/shared_car_database.cdb/roads.tbl/3d_road_smooth_track.xml
Removing overlapping points:
Removing point: 1351 0.000000 0.000000 0.000000
TIRE ID: 8
TYR900 -> Pacejka 89 Tire Model
Using 3D Spline Road
One point Contact
3D Spline road C:/Program Files/MSC.Software/Adams/2019_2/acar/shared_car_database.cdb/roads.tbl/3d_road_smooth_track.xml
Removing overlapping points:
Removing point: 1351 0.000000 0.000000 0.000000
STATICS: Original static solver will be used with the Sparse linear solver.
---- START: ERROR ----
Contact point is not on the road, end of road maybe reached.
Tire id: 6
ID = 6
---- END: ERROR ----
Static Solution converged in 8 iterations
Residual imbalance is less than 0.00000E+00
End Static Solution
Simulate status=0
command: DEACTIVATE/JPRIM,ID=2
Deactivated model.testrig.josinl_body_stake, force/torque values will be zero in function-expression references.
command: DEACTIVATE/JPRIM,ID=3
Deactivated model.testrig.josper_yaw_stake, force/torque values will be zero in function-expression references.
command: DEACTIVATE/SFORCE,ID=1
Deactivated model.testrig.sse_steering_force, force/torque values will be zero in function-expression references.
command: DEACTIVATE/JPRIM,ID=6
Deactivated model.fsae_front_tire.jolper_sse_jprim, force/torque values will be zero in function-expression references.
command: DEACTIVATE/JPRIM,ID=7
Deactivated model.fsae_front_tire.jorper_sse_jprim, force/torque values will be zero in function-expression references.
command: DEACTIVATE/JPRIM,ID=8
Deactivated model.fsae_rear_tire.jolper_sse_jprim, force/torque values will be zero in function-expression references.
command: DEACTIVATE/JPRIM,ID=9
Deactivated model.fsae_rear_tire.jorper_sse_jprim, force/torque values will be zero in function-expression references.
fdm::ActVar
Setting function on: driver_demand::clutch
command: VARIABLE/100, FUNCTION=0.0
command: ACTIVATE/JPRIM,ID=2
command: ACTIVATE/SFORCE,ID=1
command: ACTIVATE/JPRIM,ID=6
command: ACTIVATE/JPRIM,ID=7
command: ACTIVATE/JPRIM,ID=8
command: ACTIVATE/JPRIM,ID=9
command: DEACTIVATE/MOTION,ID=4
Deactivated model.testrig.jms_steering_wheel_angle.motion, force/torque values will be zero in function-expression references.
acar/vdm_gra_mod
Setting gravity vector in g's to: 0.00000E+00 0.00000E+00 -1.00000E+00
command: accgrav/igrav= 0.00000E+00,jgrav= 0.00000E+00,kgrav=-9.80665E+03
Apply a two steps statics:
Begin Static Solution
STATICS: Original static solver will be used with the Sparse linear solver.
Static Solution converged in 8 iterations
Residual imbalance is less than 8.61626E-06
End Static Solution
command: sim/sta
Begin Static Solution
STATICS: Original static solver will be used with the Sparse linear solver.
Static Solution converged in 2 iterations
Residual imbalance is less than 2.15912E-10
End Static Solution
Simulate status=0
acar/vdm_gra_mod
Setting gravity vector in g's to: 0.00000E+00 0.00000E+00 -1.00000E+00
command: accgrav/igrav= 0.00000E+00,jgrav= 0.00000E+00,kgrav=-9.80665E+03
command: DEACTIVATE/JPRIM,ID=2
Deactivated model.testrig.josinl_body_stake, force/torque values will be zero in function-expression references.
command: DEACTIVATE/SFORCE,ID=1
Deactivated model.testrig.sse_steering_force, force/torque values will be zero in function-expression references.
command: DEACTIVATE/JPRIM,ID=6
Deactivated model.fsae_front_tire.jolper_sse_jprim, force/torque values will be zero in function-expression references.
command: DEACTIVATE/JPRIM,ID=7
Deactivated model.fsae_front_tire.jorper_sse_jprim, force/torque values will be zero in function-expression references.
command: DEACTIVATE/JPRIM,ID=8
Deactivated model.fsae_rear_tire.jolper_sse_jprim, force/torque values will be zero in function-expression references.
command: DEACTIVATE/JPRIM,ID=9
Deactivated model.fsae_rear_tire.jorper_sse_jprim, force/torque values will be zero in function-expression references.
command: ACTIVATE/MOTION,ID=4
command: MOTION/4,FUNC=1.938668222799135E-04
fdm::ActVar
Setting function on: driver_demand::steering
command: VARIABLE/92, FUNCTION=0.00019386682227991346
command: DEACTIVATE/SFORCE, ID=2
Deactivated model.testrig.jfs_steering_wheel_torque.force, force/torque values will be zero in function-expression references.
fdm::ActJoiMot
Connecting: driver_demand::steering
To : steering::steering_wheel_angle
fdm::ActJoiMot
Setting function on: steering::steering_wheel_angle
command: MOTION/4, FUNCTION=VARVAL(92)
vdm:
ynamic::Setup
Setting up for minimaneuver: ADAMS_SMART_DRIVER
Note: quantities are expressed in S.I. [m, kg, s, rad].
Maneuver Name : ADAMS_SMART_DRIVER
abort time : 600.000000
sample period : 0.010000
- Demand : steering
actuator_type : ROTATION
control_method : MACHINE
- Demand : throttle
control_method : MACHINE
- Demand : braking
control_method : MACHINE
- Demand : gear
control_method : MACHINE
- Demand : clutch
control_method : MACHINE
- Machine control parameters
steer_control : PATH
speed_control : MAP
- End condition #1
type : TIME
test : >>
trigger value : 600.000000
allowed error : 0.000000
filter time : 0.000000
delay : 0.000000
group : __NO_GROUP__
vdm:
rivingMachine:
utputSignal
Info: Setting Steering IC: 0.000193867 (radians)
fdm::ActVar
Setting function on: driver_demand::steering
command: VARIABLE/92, FUNCTION=USER(985,0), ROUTINE=abgVDM::VAR985
vdm:
rivingMachine:
utputSignal
Info: Setting Throttle IC: 3.75211
vdm:
rivingMachine:
utputSignal
Info: Setting Brake IC: 6.82922e-18
fdm::ActVar
Setting function on: driver_demand::throttle
command: VARIABLE/94, FUNCTION=USER(985,1), ROUTINE=abgVDM::VAR985
fdm::ActVar
Setting function on: driver_demand::brake
command: VARIABLE/96, FUNCTION=USER(985,2), ROUTINE=abgVDM::VAR985
vdm:
rivingMachine:
utputSignal
Info: Setting Gear IC: 6
vdm:
rivingMachine:
utputSignal
Info: Setting Clutch IC: 0
fdm::ActVar
Setting function on: driver_demand::gear
command: VARIABLE/98, FUNCTION=USER(985,3), ROUTINE=abgVDM::VAR985
fdm::ActVar
Setting function on: driver_demand::clutch
command: VARIABLE/100, FUNCTION=USER(985,4), ROUTINE=abgVDM::VAR985
command: SIMULATE/DYNAMIC, DUR=600, DTOUT=0.01
Begin Simulation
****** Performing Dynamic Simulation using Gstiff I3 Integrator ******
The system is modelled with INDEX-3 DAEs.
The integrator is GSTIFF, CORRECTOR = modified
Integration error = 1.000000E-02
Simulation Step Function Cumulative Integration CPU
Time Size Evaluations Steps Taken Order time
___________ ___________ ___________ ___________ _________ ________
0.00000E+00 5.00000E-04 0 0 1 3.58
STFINT:MIN_STEP_SIZE HMIN=1.000000000E-08; Reached At Time=5.624000000E+01.
The integrator could not advance the simulation.
An attempt to further decrease the integration step-size failed.
Suggested course of action:
1. Decrease the value of HMIN.
2. Relax the accuracy requirements (ERROR) on the integrator.
3. Increase the number of iterations allowed for convergence.
4. Revisit the way the mechanical system has been modeled.
Last good step-size: 2.583806597E-08.
---- START: WARNING ----
Right road edge passed!
Tire id: 1
Simulation time is 5.711000000E+01
---- END: WARNING ----
---- START: WARNING ----
Right road edge passed!
Tire id: 3
Simulation time is 5.718785764E+01
---- END: WARNING ----
---- START: WARNING ----
Right road edge passed!
Tire id: 0
Simulation time is 5.719858881E+01
---- END: WARNING ----
STFINT:MIN_STEP_SIZE HMIN=1.000000000E-08; Reached At Time=5.723000000E+01.
The integrator could not advance the simulation.
An attempt to further decrease the integration step-size failed.
Suggested course of action:
1. Decrease the value of HMIN.
2. Relax the accuracy requirements (ERROR) on the integrator.
3. Increase the number of iterations allowed for convergence.
4. Revisit the way the mechanical system has been modeled.
Last good step-size: 1.222581343E-08.
STFINT:MIN_STEP_SIZE HMIN=1.000000000E-08; Reached At Time=5.735000000E+01.
The integrator could not advance the simulation.
An attempt to further decrease the integration step-size failed.
Suggested course of action:
1. Decrease the value of HMIN.
2. Relax the accuracy requirements (ERROR) on the integrator.
3. Increase the number of iterations allowed for convergence.
4. Revisit the way the mechanical system has been modeled.
Last good step-size: 3.138854719E-08.
STFINT:MIN_STEP_SIZE HMIN=1.000000000E-08; Reached At Time=5.736000000E+01.
The integrator could not advance the simulation.
An attempt to further decrease the integration step-size failed.
Suggested course of action:
1. Decrease the value of HMIN.
2. Relax the accuracy requirements (ERROR) on the integrator.
3. Increase the number of iterations allowed for convergence.
4. Revisit the way the mechanical system has been modeled.
Last good step-size: 1.580239414E-08.
STFINT:MIN_STEP_SIZE HMIN=1.000000000E-08; Reached At Time=5.742000000E+01.
The integrator could not advance the simulation.
An attempt to further decrease the integration step-size failed.
Suggested course of action:
1. Decrease the value of HMIN.
2. Relax the accuracy requirements (ERROR) on the integrator.
3. Increase the number of iterations allowed for convergence.
4. Revisit the way the mechanical system has been modeled.
Last good step-size: 1.033525721E-08.
STFINT:MIN_STEP_SIZE HMIN=1.000000000E-08; Reached At Time=5.743000000E+01.
The integrator could not advance the simulation.
An attempt to further decrease the integration step-size failed.
Suggested course of action:
1. Decrease the value of HMIN.
2. Relax the accuracy requirements (ERROR) on the integrator.
3. Increase the number of iterations allowed for convergence.
4. Revisit the way the mechanical system has been modeled.
Last good step-size: 1.359623232E-08.
STFINT:MIN_STEP_SIZE HMIN=1.000000000E-08; Reached At Time=5.755000000E+01.
The integrator could not advance the simulation.
An attempt to further decrease the integration step-size failed.
Suggested course of action:
1. Decrease the value of HMIN.
2. Relax the accuracy requirements (ERROR) on the integrator.
3. Increase the number of iterations allowed for convergence.
4. Revisit the way the mechanical system has been modeled.
Last good step-size: 1.093545622E-08.
STFINT:MIN_STEP_SIZE HMIN=1.000000000E-08; Reached At Time=5.762000000E+01.
The integrator could not advance the simulation.
An attempt to further decrease the integration step-size failed.
Suggested course of action:
1. Decrease the value of HMIN.
2. Relax the accuracy requirements (ERROR) on the integrator.
3. Increase the number of iterations allowed for convergence.
4. Revisit the way the mechanical system has been modeled.
Last good step-size: 1.346948258E-08.
STFINT:MIN_STEP_SIZE HMIN=1.000000000E-08; Reached At Time=5.773000000E+01.
The integrator could not advance the simulation.
An attempt to further decrease the integration step-size failed.
Suggested course of action:
1. Decrease the value of HMIN.
2. Relax the accuracy requirements (ERROR) on the integrator.
3. Increase the number of iterations allowed for convergence.
4. Revisit the way the mechanical system has been modeled.
Last good step-size: 1.348904494E-08.
STFINT:MIN_STEP_SIZE HMIN=1.000000000E-08; Reached At Time=5.784000000E+01.
The integrator could not advance the simulation.
An attempt to further decrease the integration step-size failed.
Suggested course of action:
1. Decrease the value of HMIN.
2. Relax the accuracy requirements (ERROR) on the integrator.
3. Increase the number of iterations allowed for convergence.
4. Revisit the way the mechanical system has been modeled.
Last good step-size: 1.120464558E-08.
STFINT:MIN_STEP_SIZE HMIN=1.000000000E-08; Reached At Time=5.785000000E+01.
The integrator could not advance the simulation.
An attempt to further decrease the integration step-size failed.
Suggested course of action:
1. Decrease the value of HMIN.
2. Relax the accuracy requirements (ERROR) on the integrator.
3. Increase the number of iterations allowed for convergence.
4. Revisit the way the mechanical system has been modeled.
Last good step-size: 1.571685596E-08.
STFINT:MIN_STEP_SIZE HMIN=1.000000000E-08; Reached At Time=5.790000000E+01.
The integrator could not advance the simulation.
An attempt to further decrease the integration step-size failed.
Suggested course of action:
1. Decrease the value of HMIN.
2. Relax the accuracy requirements (ERROR) on the integrator.
3. Increase the number of iterations allowed for convergence.
4. Revisit the way the mechanical system has been modeled.
Last good step-size: 1.576183364E-08.
STFINT:MIN_STEP_SIZE HMIN=1.000000000E-08; Reached At Time=5.794000000E+01.
The integrator could not advance the simulation.
An attempt to further decrease the integration step-size failed.
Suggested course of action:
1. Decrease the value of HMIN.
2. Relax the accuracy requirements (ERROR) on the integrator.
3. Increase the number of iterations allowed for convergence.
4. Revisit the way the mechanical system has been modeled.
Last good step-size: 1.136120897E-08.
STFINT:MIN_STEP_SIZE HMIN=1.000000000E-08; Reached At Time=5.795000000E+01.
The integrator could not advance the simulation.
An attempt to further decrease the integration step-size failed.
Suggested course of action:
1. Decrease the value of HMIN.
2. Relax the accuracy requirements (ERROR) on the integrator.
3. Increase the number of iterations allowed for convergence.
4. Revisit the way the mechanical system has been modeled.
Last good step-size: 1.466259889E-08.
STFINT:MIN_STEP_SIZE HMIN=1.000000000E-08; Reached At Time=5.802000000E+01.
The integrator could not advance the simulation.
An attempt to further decrease the integration step-size failed.
Suggested course of action:
1. Decrease the value of HMIN.
2. Relax the accuracy requirements (ERROR) on the integrator.
3. Increase the number of iterations allowed for convergence.
4. Revisit the way the mechanical system has been modeled.
Last good step-size: 1.635581835E-08.
STFINT:MIN_STEP_SIZE HMIN=1.000000000E-08; Reached At Time=5.803000000E+01.
The integrator could not advance the simulation.
An attempt to further decrease the integration step-size failed.
Suggested course of action:
1. Decrease the value of HMIN.
2. Relax the accuracy requirements (ERROR) on the integrator.
3. Increase the number of iterations allowed for convergence.
4. Revisit the way the mechanical system has been modeled.
Last good step-size: 2.579866606E-08.
STFINT:MIN_STEP_SIZE HMIN=1.000000000E-08; Reached At Time=5.812000000E+01.
The integrator could not advance the simulation.
An attempt to further decrease the integration step-size failed.
Suggested course of action:
1. Decrease the value of HMIN.
2. Relax the accuracy requirements (ERROR) on the integrator.
3. Increase the number of iterations allowed for convergence.
4. Revisit the way the mechanical system has been modeled.
Last good step-size: 3.091593569E-08.
STFINT:MIN_STEP_SIZE HMIN=1.000000000E-08; Reached At Time=5.813000000E+01.
The integrator could not advance the simulation.
An attempt to further decrease the integration step-size failed.
Suggested course of action:
1. Decrease the value of HMIN.
2. Relax the accuracy requirements (ERROR) on the integrator.
3. Increase the number of iterations allowed for convergence.
4. Revisit the way the mechanical system has been modeled.
Last good step-size: 1.268633957E-08.
STFINT:MIN_STEP_SIZE HMIN=1.000000000E-08; Reached At Time=5.814000000E+01.
The integrator could not advance the simulation.
An attempt to further decrease the integration step-size failed.
Suggested course of action:
1. Decrease the value of HMIN.
2. Relax the accuracy requirements (ERROR) on the integrator.
3. Increase the number of iterations allowed for convergence.
4. Revisit the way the mechanical system has been modeled.
Last good step-size: 2.774257941E-08.
STFINT:MIN_STEP_SIZE HMIN=1.000000000E-08; Reached At Time=5.847000000E+01.
The integrator could not advance the simulation.
An attempt to further decrease the integration step-size failed.
Suggested course of action:
1. Decrease the value of HMIN.
2. Relax the accuracy requirements (ERROR) on the integrator.
3. Increase the number of iterations allowed for convergence.
4. Revisit the way the mechanical system has been modeled.
Last good step-size: 1.352924459E-08.
STFINT:MIN_STEP_SIZE HMIN=1.000000000E-08; Reached At Time=5.852000000E+01.
The integrator could not advance the simulation.
An attempt to further decrease the integration step-size failed.
Suggested course of action:
1. Decrease the value of HMIN.
2. Relax the accuracy requirements (ERROR) on the integrator.
3. Increase the number of iterations allowed for convergence.
4. Revisit the way the mechanical system has been modeled.
Last good step-size: 1.317684002E-08.
STFINT:MIN_STEP_SIZE HMIN=1.000000000E-08; Reached At Time=5.854000000E+01.
The integrator could not advance the simulation.
An attempt to further decrease the integration step-size failed.
Suggested course of action:
1. Decrease the value of HMIN.
2. Relax the accuracy requirements (ERROR) on the integrator.
3. Increase the number of iterations allowed for convergence.
4. Revisit the way the mechanical system has been modeled.
Last good step-size: 1.021133813E-08.
STFINT:MIN_STEP_SIZE HMIN=1.000000000E-08; Reached At Time=5.855000000E+01.
The integrator could not advance the simulation.
An attempt to further decrease the integration step-size failed.
Suggested course of action:
1. Decrease the value of HMIN.
2. Relax the accuracy requirements (ERROR) on the integrator.
3. Increase the number of iterations allowed for convergence.
4. Revisit the way the mechanical system has been modeled.
Last good step-size: 1.751435948E-08.
STFINT:MIN_STEP_SIZE HMIN=1.000000000E-08; Reached At Time=5.856000000E+01.
The integrator could not advance the simulation.
An attempt to further decrease the integration step-size failed.
Suggested course of action:
1. Decrease the value of HMIN.
2. Relax the accuracy requirements (ERROR) on the integrator.
3. Increase the number of iterations allowed for convergence.
4. Revisit the way the mechanical system has been modeled.
Last good step-size: 2.504145194E-08.
STFINT:MIN_STEP_SIZE HMIN=1.000000000E-08; Reached At Time=5.863000000E+01.
The integrator could not advance the simulation.
An attempt to further decrease the integration step-size failed.
Suggested course of action:
1. Decrease the value of HMIN.
2. Relax the accuracy requirements (ERROR) on the integrator.
3. Increase the number of iterations allowed for convergence.
4. Revisit the way the mechanical system has been modeled.
Last good step-size: 1.360748988E-08.
STFINT:MIN_STEP_SIZE HMIN=1.000000000E-08; Reached At Time=5.865000000E+01.
The integrator could not advance the simulation.
An attempt to further decrease the integration step-size failed.
Suggested course of action:
1. Decrease the value of HMIN.
2. Relax the accuracy requirements (ERROR) on the integrator.
3. Increase the number of iterations allowed for convergence.
4. Revisit the way the mechanical system has been modeled.
Last good step-size: 1.181008889E-08.
STFINT:MIN_STEP_SIZE HMIN=1.000000000E-08; Reached At Time=5.867000000E+01.
The integrator could not advance the simulation.
An attempt to further decrease the integration step-size failed.
Suggested course of action:
1. Decrease the value of HMIN.
2. Relax the accuracy requirements (ERROR) on the integrator.
3. Increase the number of iterations allowed for convergence.
4. Revisit the way the mechanical system has been modeled.
Last good step-size: 2.629760666E-08.
STFINT:MIN_STEP_SIZE HMIN=1.000000000E-08; Reached At Time=5.869000000E+01.
The integrator could not advance the simulation.
An attempt to further decrease the integration step-size failed.
Suggested course of action:
1. Decrease the value of HMIN.
2. Relax the accuracy requirements (ERROR) on the integrator.
3. Increase the number of iterations allowed for convergence.
4. Revisit the way the mechanical system has been modeled.
Last good step-size: 1.227114873E-08.
STFINT:MIN_STEP_SIZE HMIN=1.000000000E-08; Reached At Time=5.870000000E+01.
The integrator could not advance the simulation.
An attempt to further decrease the integration step-size failed.
Suggested course of action:
1. Decrease the value of HMIN.
2. Relax the accuracy requirements (ERROR) on the integrator.
3. Increase the number of iterations allowed for convergence.
4. Revisit the way the mechanical system has been modeled.
Last good step-size: 1.398442324E-08.
STFINT:MIN_STEP_SIZE HMIN=1.000000000E-08; Reached At Time=5.872000000E+01.
The integrator could not advance the simulation.
An attempt to further decrease the integration step-size failed.
Suggested course of action:
1. Decrease the value of HMIN.
2. Relax the accuracy requirements (ERROR) on the integrator.
3. Increase the number of iterations allowed for convergence.
4. Revisit the way the mechanical system has been modeled.
Last good step-size: 2.456432940E-08.
STFINT:MIN_STEP_SIZE HMIN=1.000000000E-08; Reached At Time=5.877000000E+01.
The integrator could not advance the simulation.
An attempt to further decrease the integration step-size failed.
Suggested course of action:
1. Decrease the value of HMIN.
2. Relax the accuracy requirements (ERROR) on the integrator.
3. Increase the number of iterations allowed for convergence.
4. Revisit the way the mechanical system has been modeled.
Last good step-size: 1.612340668E-08.
STFINT:MIN_STEP_SIZE HMIN=1.000000000E-08; Reached At Time=5.878000000E+01.
The integrator could not advance the simulation.
An attempt to further decrease the integration step-size failed.
Suggested course of action:
1. Decrease the value of HMIN.
2. Relax the accuracy requirements (ERROR) on the integrator.
3. Increase the number of iterations allowed for convergence.
4. Revisit the way the mechanical system has been modeled.
Last good step-size: 1.364133387E-08.
STFINT:MIN_STEP_SIZE HMIN=1.000000000E-08; Reached At Time=5.882000000E+01.
The integrator could not advance the simulation.
An attempt to further decrease the integration step-size failed.
Suggested course of action:
1. Decrease the value of HMIN.
2. Relax the accuracy requirements (ERROR) on the integrator.
3. Increase the number of iterations allowed for convergence.
4. Revisit the way the mechanical system has been modeled.
Last good step-size: 2.966662959E-08.
STFINT:MIN_STEP_SIZE HMIN=1.000000000E-08; Reached At Time=5.884000000E+01.
The integrator could not advance the simulation.
An attempt to further decrease the integration step-size failed.
Suggested course of action:
1. Decrease the value of HMIN.
2. Relax the accuracy requirements (ERROR) on the integrator.
3. Increase the number of iterations allowed for convergence.
4. Revisit the way the mechanical system has been modeled.
Last good step-size: 1.559977286E-08.
STFINT:MIN_STEP_SIZE HMIN=1.000000000E-08; Reached At Time=5.887000000E+01.
The integrator could not advance the simulation.
An attempt to further decrease the integration step-size failed.
Suggested course of action:
1. Decrease the value of HMIN.
2. Relax the accuracy requirements (ERROR) on the integrator.
3. Increase the number of iterations allowed for convergence.
4. Revisit the way the mechanical system has been modeled.
Last good step-size: 1.023119753E-08.
STFINT:MIN_STEP_SIZE HMIN=1.000000000E-08; Reached At Time=5.888000000E+01.
The integrator could not advance the simulation.
An attempt to further decrease the integration step-size failed.
Suggested course of action:
1. Decrease the value of HMIN.
2. Relax the accuracy requirements (ERROR) on the integrator.
3. Increase the number of iterations allowed for convergence.
4. Revisit the way the mechanical system has been modeled.
Last good step-size: 1.511731316E-08.
STFINT:MIN_STEP_SIZE HMIN=1.000000000E-08; Reached At Time=5.890000000E+01.
The integrator could not advance the simulation.
An attempt to further decrease the integration step-size failed.
Suggested course of action:
1. Decrease the value of HMIN.
2. Relax the accuracy requirements (ERROR) on the integrator.
3. Increase the number of iterations allowed for convergence.
4. Revisit the way the mechanical system has been modeled.
Last good step-size: 1.157932692E-08.
STFINT:MIN_STEP_SIZE HMIN=1.000000000E-08; Reached At Time=5.891000000E+01.
The integrator could not advance the simulation.
An attempt to further decrease the integration step-size failed.
Suggested course of action:
1. Decrease the value of HMIN.
2. Relax the accuracy requirements (ERROR) on the integrator.
3. Increase the number of iterations allowed for convergence.
4. Revisit the way the mechanical system has been modeled.
Last good step-size: 1.318509821E-08.
STFINT:MIN_STEP_SIZE HMIN=1.000000000E-08; Reached At Time=5.892000000E+01.
The integrator could not advance the simulation.
An attempt to further decrease the integration step-size failed.
Suggested course of action:
1. Decrease the value of HMIN.
2. Relax the accuracy requirements (ERROR) on the integrator.
3. Increase the number of iterations allowed for convergence.
4. Revisit the way the mechanical system has been modeled.
Last good step-size: 2.101033921E-08.
STFINT:MIN_STEP_SIZE HMIN=1.000000000E-08; Reached At Time=5.908000000E+01.
The integrator could not advance the simulation.
An attempt to further decrease the integration step-size failed.
Suggested course of action:
1. Decrease the value of HMIN.
2. Relax the accuracy requirements (ERROR) on the integrator.
3. Increase the number of iterations allowed for convergence.
4. Revisit the way the mechanical system has been modeled.
Last good step-size: 2.915244809E-08.
STFINT:MIN_STEP_SIZE HMIN=1.000000000E-08; Reached At Time=5.909000000E+01.
The integrator could not advance the simulation.
An attempt to further decrease the integration step-size failed.
Suggested course of action:
1. Decrease the value of HMIN.
2. Relax the accuracy requirements (ERROR) on the integrator.
3. Increase the number of iterations allowed for convergence.
4. Revisit the way the mechanical system has been modeled.
Last good step-size: 3.915533188E-08.
STFINT:MIN_STEP_SIZE HMIN=1.000000000E-08; Reached At Time=5.910000000E+01.
The integrator could not advance the simulation.
An attempt to further decrease the integration step-size failed.
Suggested course of action:
1. Decrease the value of HMIN.
2. Relax the accuracy requirements (ERROR) on the integrator.
3. Increase the number of iterations allowed for convergence.
4. Revisit the way the mechanical system has been modeled.
Last good step-size: 1.163095477E-08.
STFINT:MIN_STEP_SIZE HMIN=1.000000000E-08; Reached At Time=5.910010344E+01.
The integrator could not advance the simulation.
An attempt to further decrease the integration step-size failed.
Suggested course of action:
1. Decrease the value of HMIN.
2. Relax the accuracy requirements (ERROR) on the integrator.
3. Increase the number of iterations allowed for convergence.
4. Revisit the way the mechanical system has been modeled.
Last good step-size: 3.452081530E-08.
STFINT:MIN_STEP_SIZE HMIN=1.000000000E-08; Reached At Time=5.911000000E+01.
The integrator could not advance the simulation.
An attempt to further decrease the integration step-size failed.
Suggested course of action:
1. Decrease the value of HMIN.
2. Relax the accuracy requirements (ERROR) on the integrator.
3. Increase the number of iterations allowed for convergence.
4. Revisit the way the mechanical system has been modeled.
Last good step-size: 1.536897407E-08.
STFINT:MIN_STEP_SIZE HMIN=1.000000000E-08; Reached At Time=5.912000000E+01.
The integrator could not advance the simulation.
An attempt to further decrease the integration step-size failed.
Suggested course of action:
1. Decrease the value of HMIN.
2. Relax the accuracy requirements (ERROR) on the integrator.
3. Increase the number of iterations allowed for convergence.
4. Revisit the way the mechanical system has been modeled.
Last good step-size: 3.469928182E-08.
STFINT:MIN_STEP_SIZE HMIN=1.000000000E-08; Reached At Time=5.913000000E+01.
The integrator could not advance the simulation.
An attempt to further decrease the integration step-size failed.
Suggested course of action:
1. Decrease the value of HMIN.
2. Relax the accuracy requirements (ERROR) on the integrator.
3. Increase the number of iterations allowed for convergence.
4. Revisit the way the mechanical system has been modeled.
Last good step-size: 1.898442316E-08.
STFINT:MIN_STEP_SIZE HMIN=1.000000000E-08; Reached At Time=5.914000000E+01.
The integrator could not advance the simulation.
An attempt to further decrease the integration step-size failed.
Suggested course of action:
1. Decrease the value of HMIN.
2. Relax the accuracy requirements (ERROR) on the integrator.
3. Increase the number of iterations allowed for convergence.
4. Revisit the way the mechanical system has been modeled.
Last good step-size: 3.679658324E-08.
STFINT:MIN_STEP_SIZE HMIN=1.000000000E-08; Reached At Time=5.915000000E+01.
The integrator could not advance the simulation.
An attempt to further decrease the integration step-size failed.
Suggested course of action:
1. Decrease the value of HMIN.
2. Relax the accuracy requirements (ERROR) on the integrator.
3. Increase the number of iterations allowed for convergence.
4. Revisit the way the mechanical system has been modeled.
Last good step-size: 3.735121450E-08.
STFINT:MIN_STEP_SIZE HMIN=1.000000000E-08; Reached At Time=5.916000000E+01.
The integrator could not advance the simulation.
An attempt to further decrease the integration step-size failed.
Suggested course of action:
1. Decrease the value of HMIN.
2. Relax the accuracy requirements (ERROR) on the integrator.
3. Increase the number of iterations allowed for convergence.
4. Revisit the way the mechanical system has been modeled.
Last good step-size: 1.978423952E-08.
STFINT:MIN_STEP_SIZE HMIN=1.000000000E-08; Reached At Time=5.917000000E+01.
The integrator could not advance the simulation.
An attempt to further decrease the integration step-size failed.
Suggested course of action:
1. Decrease the value of HMIN.
2. Relax the accuracy requirements (ERROR) on the integrator.
3. Increase the number of iterations allowed for convergence.
4. Revisit the way the mechanical system has been modeled.
Last good step-size: 3.231917852E-08.
STFINT:MIN_STEP_SIZE HMIN=1.000000000E-08; Reached At Time=5.918000000E+01.
The integrator could not advance the simulation.
An attempt to further decrease the integration step-size failed.
Suggested course of action:
1. Decrease the value of HMIN.
2. Relax the accuracy requirements (ERROR) on the integrator.
3. Increase the number of iterations allowed for convergence.
4. Revisit the way the mechanical system has been modeled.
Last good step-size: 4.126851332E-08.
STFINT:MIN_STEP_SIZE HMIN=1.000000000E-08; Reached At Time=5.919000000E+01.
The integrator could not advance the simulation.
An attempt to further decrease the integration step-size failed.
Suggested course of action:
1. Decrease the value of HMIN.
2. Relax the accuracy requirements (ERROR) on the integrator.
3. Increase the number of iterations allowed for convergence.
4. Revisit the way the mechanical system has been modeled.
Last good step-size: 1.586853770E-08.
STFINT:MIN_STEP_SIZE HMIN=1.000000000E-08; Reached At Time=5.920000000E+01.
The integrator could not advance the simulation.
An attempt to further decrease the integration step-size failed.
Suggested course of action:
1. Decrease the value of HMIN.
2. Relax the accuracy requirements (ERROR) on the integrator.
3. Increase the number of iterations allowed for convergence.
4. Revisit the way the mechanical system has been modeled.
Last good step-size: 2.567768974E-08.
STFINT:MIN_STEP_SIZE HMIN=1.000000000E-08; Reached At Time=5.921000000E+01.
The integrator could not advance the simulation.
An attempt to further decrease the integration step-size failed.
Suggested course of action:
1. Decrease the value of HMIN.
2. Relax the accuracy requirements (ERROR) on the integrator.
3. Increase the number of iterations allowed for convergence.
4. Revisit the way the mechanical system has been modeled.
Last good step-size: 3.296201693E-08.
STFINT:MIN_STEP_SIZE HMIN=1.000000000E-08; Reached At Time=5.922000000E+01.
The integrator could not advance the simulation.
An attempt to further decrease the integration step-size failed.
Suggested course of action:
1. Decrease the value of HMIN.
2. Relax the accuracy requirements (ERROR) on the integrator.
3. Increase the number of iterations allowed for convergence.
4. Revisit the way the mechanical system has been modeled.
Last good step-size: 2.671155612E-08.
STFINT:MIN_STEP_SIZE HMIN=1.000000000E-08; Reached At Time=5.923000000E+01.
The integrator could not advance the simulation.
An attempt to further decrease the integration step-size failed.
Suggested course of action:
1. Decrease the value of HMIN.
2. Relax the accuracy requirements (ERROR) on the integrator.
3. Increase the number of iterations allowed for convergence.
4. Revisit the way the mechanical system has been modeled.
Last good step-size: 1.637524089E-08.
STFINT:MIN_STEP_SIZE HMIN=1.000000000E-08; Reached At Time=5.924000000E+01.
The integrator could not advance the simulation.
An attempt to further decrease the integration step-size failed.
Suggested course of action:
1. Decrease the value of HMIN.
2. Relax the accuracy requirements (ERROR) on the integrator.
3. Increase the number of iterations allowed for convergence.
4. Revisit the way the mechanical system has been modeled.
Last good step-size: 1.062767277E-08.
STFINT:MIN_STEP_SIZE HMIN=1.000000000E-08; Reached At Time=5.925000000E+01.
The integrator could not advance the simulation.
An attempt to further decrease the integration step-size failed.
Suggested course of action:
1. Decrease the value of HMIN.
2. Relax the accuracy requirements (ERROR) on the integrator.
3. Increase the number of iterations allowed for convergence.
4. Revisit the way the mechanical system has been modeled.
Last good step-size: 2.008101422E-08.
STFINT:MIN_STEP_SIZE HMIN=1.000000000E-08; Reached At Time=5.926000000E+01.
The integrator could not advance the simulation.
An attempt to further decrease the integration step-size failed.
Suggested course of action:
1. Decrease the value of HMIN.
2. Relax the accuracy requirements (ERROR) on the integrator.
3. Increase the number of iterations allowed for convergence.
4. Revisit the way the mechanical system has been modeled.
Last good step-size: 1.045900172E-08.
STFINT:MIN_STEP_SIZE HMIN=1.000000000E-08; Reached At Time=5.926999944E+01.
The integrator could not advance the simulation.
An attempt to further decrease the integration step-size failed.
Suggested course of action:
1. Decrease the value of HMIN.
2. Relax the accuracy requirements (ERROR) on the integrator.
3. Increase the number of iterations allowed for convergence.
4. Revisit the way the mechanical system has been modeled.
Last good step-size: 1.210867447E-08.
---- START: ERROR ----
The integrator is unable to proceed. Possible Causes:
(1) The accuracy required for the numerical solution can not be attained.
Relax (increase) the value of the acceptable integration ERROR.
(2) Incompatible redundant constraints, a lock up, or a bifurcation
situation. The latter two indicate a mechanism design problem.
(3) The system includes a zero (or relatively small) mass on a part with
an unconstrained translational degree of freedom.
Make sure you have mass on all parts with translational degrees of freedom.
(4) The system includes a zero (or relatively small) inertia on a part
with an unconstrained rotational degree of freedom.
Make sure you have inertias on all parts with rotational degrees of freedom.
(5) An Adams element has a function expression that equals exactly itself.
For example,
SFORCE/id1,I=id2,J=id3,ROT,FUNC=SFORCE(id1,jflag,comp,rm),and
DIFF/id4,IMPLICIT,IC=0,FUNC=DIF1(id4).
Similarly,
VARIABLE/id5, FUNC=VARVAL(id5)*TIME
equals itself at 1 second. Avoid setting an Adams element equal to itself.
Simulation time is 5.927542149E+01
Simulation time is 5.927542149E+01
---- END: ERROR ----
Dynamic Solution stopped.
End Simulation
Simulate status=-124
---- START: ERROR ----
SIMULATE command failed for minimaneuver: ADAMS_SMART_DRIVER
Aborting Execution.
Simulation time is 5.927542149E+01
---- END: ERROR ----
---- START: ERROR ----
Adams Solver (C++) run terminating due to STOP requested by user.
Simulation time is 5.927542149E+01
---- END: ERROR ----
Termination status=-995
Terminating Adams Car usersubs...
Finished -----
Elapsed time = 1055.54s, CPU time = 1073.20s, 101.67%
Simulation is complete.
As you can see our model, goes out in last corner.
I hope to see your help.
We are trying to complete one tour track with our fsae model for bachelor project. We design just front suspension and build and assembly with fsae_2018 template. I have a few question that we can't achieve anthying.
1) As you can see in our model, we think there is a problem with anti-roll bar and rocker joint. Can you help us ?
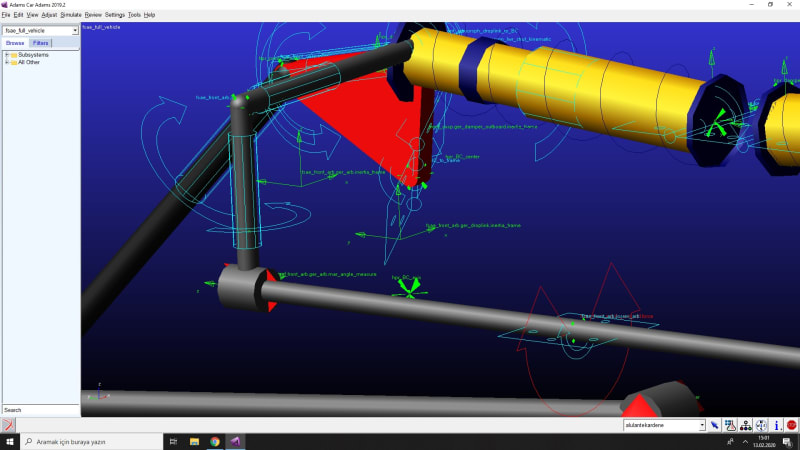
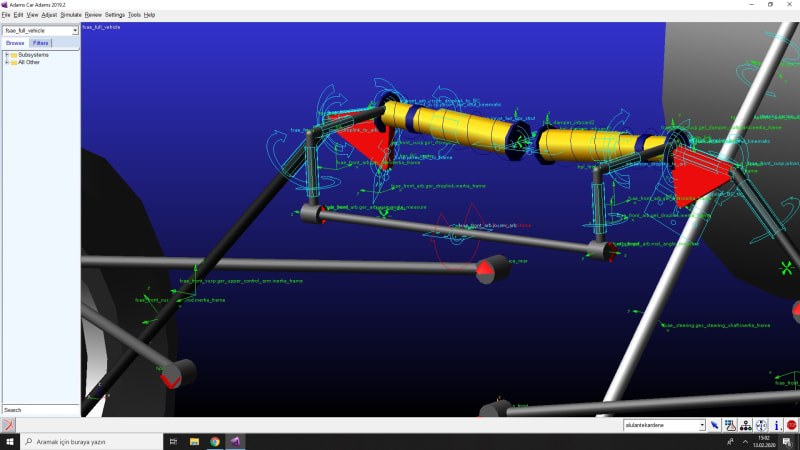
2) With these configurations in Smart-driver;
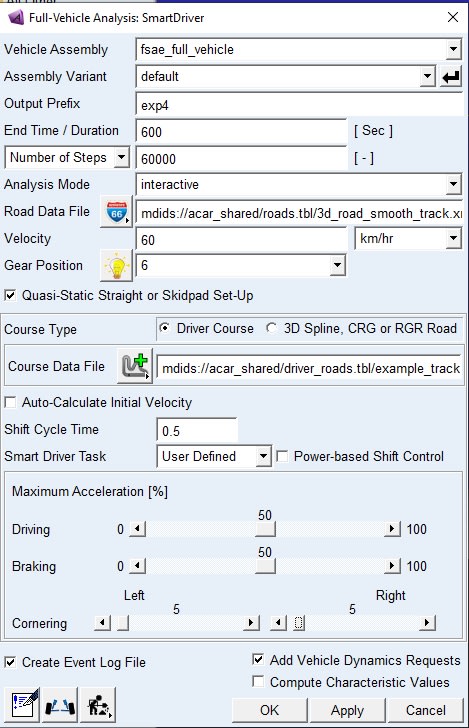
We have a problem with cornering in the last-corner.
-------------------------------------------------------------------------------
| Model Title |
|=============================================================================|
| |
| Adams Car Assembly (Adams 2019.2) |
| |
-------------------------------------------------------------------------------
command: !
command: !INFO Adams Version: Adams 2019.2
command: !INFO Adams Build: 2019.2.0-CL661333
command: !INFO Assembly File: <alulantekardene>/assemblies.tbl/fsae_full_vehicle.asy
command: !INFO Solver Library: C:/PROGRA~1/MSC~1.SOF/Adams/2019_2/win64/acar_solver.dll
command: !
command: string/5, string=exp4_smart_driver.xml
command: preferences/solver=CXX
command: preferences/list,status=on
PREFERENCES:
SIMFAIL = NOSTOPCF
Contact Geometry Library = (not loaded)
Thread Count = 1
Library Search Path = Not Set
Status Message = On
Solverbias = CXX (C++ Solver)
command: control/routine=abgTire::con901,func=user(901,85,98,104,1,2)
command: control/routine=abgTire::con901,func=user(901,89,99,105,1,4)
command: control/routine=abgTire::con901,func=user(901,94,107,113,1,6)
command: control/routine=abgTire::con901,func=user(901,98,108,114,1,8)
command: output/nosep
command: control/routine=abgVDM::EventInit, function=user(5,1,8,0,3,6,6,17)
vdm::EvtMonitor::EvtMonitor
End conditions evaluated in SENSUB.
ASD_vfSet_Globals()
=================================================================
Adams Smartdriver
Version Adams 2019.2
=================================================================
Using SmartDriver Template file:
C:\Program Files\MSC.Software\Adams\2019_2\win64/.smartdriver.xml
SDF_xml_upd_controller()
Info: minPreviewDistance is negative or not set, using default 5m.
Drv_Model::vfSetMaxLenItx
Info: MaxLenItx is negative or not set, using default (100m).
SDF_xml_upd_mini()
Max. Drive Accel = 50
Max. Brake Accel = 50
Max. LatAcc Left = 5
Max. LatAcc Right = 5
Geo_DCurve::ifFit_BSpline()
Info: Fitting BSplines with iOrder = 4, Closed = 0 and iNP = 1351.
SmartDriver: preparing speed profile using:
TYR900 -> Pacejka 89 Tire Model
TYR900 -> Pacejka 89 Tire Model
Road3D::vfPreprocessRoad : Road is flat (all banks same, all slopes same), short-cuts will be taken.
Road3D::vfPreprocessRoad : Road is flat (all banks same, all slopes same), short-cuts will be taken.
TYR900 -> Pacejka 89 Tire Model
TYR900 -> Pacejka 89 Tire Model
Road3D::vfPreprocessRoad : Road is flat (all banks same, all slopes same), short-cuts will be taken.
SDBrain::vfCalc()
Info: Begin Speed Profile Calculation
Info: End Speed Profile Calculation
Drv_Core::ifSDBpre
AutoAccX is FALSE.
Static Set-up solution may be inconsistent with target at t=0.
Setting Longitudinal Setup Type to NONE.
command: control/routine=abgVDM::EventRunAll, function=user(0)
fdm::ActJoiMot
Setting function on: steering::steering_wheel_angle
command: MOTION/4, FUNCTION=0.0
command: SFORCE/1, FUNCTION=0.0
fdm::ActVar
Connecting: steering::steering_wheel_angle
To : driver_demand::steering
fdm::ActVar
Setting function on: driver_demand::steering
command: VARIABLE/92, FUNCTION=AZ(683,891)
command: DEACTIVATE/SFORCE, ID=4
Deactivated model.testrig.jfs_steering_rack_force.force, force/torque values will be zero in function-expression references.
command: DEACTIVATE/SFORCE, ID=5
Deactivated model.testrig.jfs_steering_rack_force.force_j, force/torque values will be zero in function-expression references.
command: DEACTIVATE/MOTION, ID=3
Deactivated model.testrig.jms_steering_rack_travel.motion, force/torque values will be zero in function-expression references.
command: DEACTIVATE/MOTION, ID=4
Deactivated model.testrig.jms_steering_wheel_angle.motion, force/torque values will be zero in function-expression references.
fdm::ActJoiFor
Setting function on: steering::steering_wheel_torque
command: SFORCE/2, FUNCTION=DIF(4)
fdm::ActVar
Setting function on: driver_demand::throttle
command: VARIABLE/94, FUNCTION=USER(976,3)\ ROUTINE=abgVDM::var976
fdm::ActVar
Setting function on: driver_demand::brake
command: VARIABLE/96, FUNCTION=USER(975,3)\ ROUTINE=abgVDM::var975
fdm::ActVar
Setting function on: driver_demand::gear
command: VARIABLE/98, FUNCTION=(6.0)
fdm::ActVar
Setting function on: driver_demand::clutch
command: VARIABLE/100, FUNCTION=0.0
vdm::SteadyState::MiniInfo
Static Task : 'Straight'
Lon. Acceleration : 0.000 [m/s^2]
Initial Velocity : 16.667 [m/s]
Perform Linear : No
Include Damping : Yes
Halt on Failure : Yes
fdm::ActVar
Setting function on: driver_demand::clutch
command: VARIABLE/100, FUNCTION=1.0
command: ACTIVATE/MOTION,ID=4
command: SIM/STAT
Begin Static Solution
TIRE ID: 2
TYR900 -> Pacejka 89 Tire Model
Using 3D Spline Road
One point Contact
3D Spline road C:/Program Files/MSC.Software/Adams/2019_2/acar/shared_car_database.cdb/roads.tbl/3d_road_smooth_track.xml
Removing overlapping points:
Removing point: 1351 0.000000 0.000000 0.000000
TIRE ID: 4
TYR900 -> Pacejka 89 Tire Model
Using 3D Spline Road
One point Contact
3D Spline road C:/Program Files/MSC.Software/Adams/2019_2/acar/shared_car_database.cdb/roads.tbl/3d_road_smooth_track.xml
Removing overlapping points:
Removing point: 1351 0.000000 0.000000 0.000000
TIRE ID: 6
TYR900 -> Pacejka 89 Tire Model
Using 3D Spline Road
One point Contact
3D Spline road C:/Program Files/MSC.Software/Adams/2019_2/acar/shared_car_database.cdb/roads.tbl/3d_road_smooth_track.xml
Removing overlapping points:
Removing point: 1351 0.000000 0.000000 0.000000
TIRE ID: 8
TYR900 -> Pacejka 89 Tire Model
Using 3D Spline Road
One point Contact
3D Spline road C:/Program Files/MSC.Software/Adams/2019_2/acar/shared_car_database.cdb/roads.tbl/3d_road_smooth_track.xml
Removing overlapping points:
Removing point: 1351 0.000000 0.000000 0.000000
STATICS: Original static solver will be used with the Sparse linear solver.
---- START: ERROR ----
Contact point is not on the road, end of road maybe reached.
Tire id: 6
ID = 6
---- END: ERROR ----
Static Solution converged in 8 iterations
Residual imbalance is less than 0.00000E+00
End Static Solution
Simulate status=0
command: DEACTIVATE/JPRIM,ID=2
Deactivated model.testrig.josinl_body_stake, force/torque values will be zero in function-expression references.
command: DEACTIVATE/JPRIM,ID=3
Deactivated model.testrig.josper_yaw_stake, force/torque values will be zero in function-expression references.
command: DEACTIVATE/SFORCE,ID=1
Deactivated model.testrig.sse_steering_force, force/torque values will be zero in function-expression references.
command: DEACTIVATE/JPRIM,ID=6
Deactivated model.fsae_front_tire.jolper_sse_jprim, force/torque values will be zero in function-expression references.
command: DEACTIVATE/JPRIM,ID=7
Deactivated model.fsae_front_tire.jorper_sse_jprim, force/torque values will be zero in function-expression references.
command: DEACTIVATE/JPRIM,ID=8
Deactivated model.fsae_rear_tire.jolper_sse_jprim, force/torque values will be zero in function-expression references.
command: DEACTIVATE/JPRIM,ID=9
Deactivated model.fsae_rear_tire.jorper_sse_jprim, force/torque values will be zero in function-expression references.
fdm::ActVar
Setting function on: driver_demand::clutch
command: VARIABLE/100, FUNCTION=0.0
command: ACTIVATE/JPRIM,ID=2
command: ACTIVATE/SFORCE,ID=1
command: ACTIVATE/JPRIM,ID=6
command: ACTIVATE/JPRIM,ID=7
command: ACTIVATE/JPRIM,ID=8
command: ACTIVATE/JPRIM,ID=9
command: DEACTIVATE/MOTION,ID=4
Deactivated model.testrig.jms_steering_wheel_angle.motion, force/torque values will be zero in function-expression references.
acar/vdm_gra_mod
Setting gravity vector in g's to: 0.00000E+00 0.00000E+00 -1.00000E+00
command: accgrav/igrav= 0.00000E+00,jgrav= 0.00000E+00,kgrav=-9.80665E+03
Apply a two steps statics:
Begin Static Solution
STATICS: Original static solver will be used with the Sparse linear solver.
Static Solution converged in 8 iterations
Residual imbalance is less than 8.61626E-06
End Static Solution
command: sim/sta
Begin Static Solution
STATICS: Original static solver will be used with the Sparse linear solver.
Static Solution converged in 2 iterations
Residual imbalance is less than 2.15912E-10
End Static Solution
Simulate status=0
acar/vdm_gra_mod
Setting gravity vector in g's to: 0.00000E+00 0.00000E+00 -1.00000E+00
command: accgrav/igrav= 0.00000E+00,jgrav= 0.00000E+00,kgrav=-9.80665E+03
command: DEACTIVATE/JPRIM,ID=2
Deactivated model.testrig.josinl_body_stake, force/torque values will be zero in function-expression references.
command: DEACTIVATE/SFORCE,ID=1
Deactivated model.testrig.sse_steering_force, force/torque values will be zero in function-expression references.
command: DEACTIVATE/JPRIM,ID=6
Deactivated model.fsae_front_tire.jolper_sse_jprim, force/torque values will be zero in function-expression references.
command: DEACTIVATE/JPRIM,ID=7
Deactivated model.fsae_front_tire.jorper_sse_jprim, force/torque values will be zero in function-expression references.
command: DEACTIVATE/JPRIM,ID=8
Deactivated model.fsae_rear_tire.jolper_sse_jprim, force/torque values will be zero in function-expression references.
command: DEACTIVATE/JPRIM,ID=9
Deactivated model.fsae_rear_tire.jorper_sse_jprim, force/torque values will be zero in function-expression references.
command: ACTIVATE/MOTION,ID=4
command: MOTION/4,FUNC=1.938668222799135E-04
fdm::ActVar
Setting function on: driver_demand::steering
command: VARIABLE/92, FUNCTION=0.00019386682227991346
command: DEACTIVATE/SFORCE, ID=2
Deactivated model.testrig.jfs_steering_wheel_torque.force, force/torque values will be zero in function-expression references.
fdm::ActJoiMot
Connecting: driver_demand::steering
To : steering::steering_wheel_angle
fdm::ActJoiMot
Setting function on: steering::steering_wheel_angle
command: MOTION/4, FUNCTION=VARVAL(92)
vdm:

Setting up for minimaneuver: ADAMS_SMART_DRIVER
Note: quantities are expressed in S.I. [m, kg, s, rad].
Maneuver Name : ADAMS_SMART_DRIVER
abort time : 600.000000
sample period : 0.010000
- Demand : steering
actuator_type : ROTATION
control_method : MACHINE
- Demand : throttle
control_method : MACHINE
- Demand : braking
control_method : MACHINE
- Demand : gear
control_method : MACHINE
- Demand : clutch
control_method : MACHINE
- Machine control parameters
steer_control : PATH
speed_control : MAP
- End condition #1
type : TIME
test : >>
trigger value : 600.000000
allowed error : 0.000000
filter time : 0.000000
delay : 0.000000
group : __NO_GROUP__
vdm:


Info: Setting Steering IC: 0.000193867 (radians)
fdm::ActVar
Setting function on: driver_demand::steering
command: VARIABLE/92, FUNCTION=USER(985,0), ROUTINE=abgVDM::VAR985
vdm:


Info: Setting Throttle IC: 3.75211
vdm:


Info: Setting Brake IC: 6.82922e-18
fdm::ActVar
Setting function on: driver_demand::throttle
command: VARIABLE/94, FUNCTION=USER(985,1), ROUTINE=abgVDM::VAR985
fdm::ActVar
Setting function on: driver_demand::brake
command: VARIABLE/96, FUNCTION=USER(985,2), ROUTINE=abgVDM::VAR985
vdm:


Info: Setting Gear IC: 6
vdm:


Info: Setting Clutch IC: 0
fdm::ActVar
Setting function on: driver_demand::gear
command: VARIABLE/98, FUNCTION=USER(985,3), ROUTINE=abgVDM::VAR985
fdm::ActVar
Setting function on: driver_demand::clutch
command: VARIABLE/100, FUNCTION=USER(985,4), ROUTINE=abgVDM::VAR985
command: SIMULATE/DYNAMIC, DUR=600, DTOUT=0.01
Begin Simulation
****** Performing Dynamic Simulation using Gstiff I3 Integrator ******
The system is modelled with INDEX-3 DAEs.
The integrator is GSTIFF, CORRECTOR = modified
Integration error = 1.000000E-02
Simulation Step Function Cumulative Integration CPU
Time Size Evaluations Steps Taken Order time
___________ ___________ ___________ ___________ _________ ________
0.00000E+00 5.00000E-04 0 0 1 3.58
STFINT:MIN_STEP_SIZE HMIN=1.000000000E-08; Reached At Time=5.624000000E+01.
The integrator could not advance the simulation.
An attempt to further decrease the integration step-size failed.
Suggested course of action:
1. Decrease the value of HMIN.
2. Relax the accuracy requirements (ERROR) on the integrator.
3. Increase the number of iterations allowed for convergence.
4. Revisit the way the mechanical system has been modeled.
Last good step-size: 2.583806597E-08.
---- START: WARNING ----
Right road edge passed!
Tire id: 1
Simulation time is 5.711000000E+01
---- END: WARNING ----
---- START: WARNING ----
Right road edge passed!
Tire id: 3
Simulation time is 5.718785764E+01
---- END: WARNING ----
---- START: WARNING ----
Right road edge passed!
Tire id: 0
Simulation time is 5.719858881E+01
---- END: WARNING ----
STFINT:MIN_STEP_SIZE HMIN=1.000000000E-08; Reached At Time=5.723000000E+01.
The integrator could not advance the simulation.
An attempt to further decrease the integration step-size failed.
Suggested course of action:
1. Decrease the value of HMIN.
2. Relax the accuracy requirements (ERROR) on the integrator.
3. Increase the number of iterations allowed for convergence.
4. Revisit the way the mechanical system has been modeled.
Last good step-size: 1.222581343E-08.
STFINT:MIN_STEP_SIZE HMIN=1.000000000E-08; Reached At Time=5.735000000E+01.
The integrator could not advance the simulation.
An attempt to further decrease the integration step-size failed.
Suggested course of action:
1. Decrease the value of HMIN.
2. Relax the accuracy requirements (ERROR) on the integrator.
3. Increase the number of iterations allowed for convergence.
4. Revisit the way the mechanical system has been modeled.
Last good step-size: 3.138854719E-08.
STFINT:MIN_STEP_SIZE HMIN=1.000000000E-08; Reached At Time=5.736000000E+01.
The integrator could not advance the simulation.
An attempt to further decrease the integration step-size failed.
Suggested course of action:
1. Decrease the value of HMIN.
2. Relax the accuracy requirements (ERROR) on the integrator.
3. Increase the number of iterations allowed for convergence.
4. Revisit the way the mechanical system has been modeled.
Last good step-size: 1.580239414E-08.
STFINT:MIN_STEP_SIZE HMIN=1.000000000E-08; Reached At Time=5.742000000E+01.
The integrator could not advance the simulation.
An attempt to further decrease the integration step-size failed.
Suggested course of action:
1. Decrease the value of HMIN.
2. Relax the accuracy requirements (ERROR) on the integrator.
3. Increase the number of iterations allowed for convergence.
4. Revisit the way the mechanical system has been modeled.
Last good step-size: 1.033525721E-08.
STFINT:MIN_STEP_SIZE HMIN=1.000000000E-08; Reached At Time=5.743000000E+01.
The integrator could not advance the simulation.
An attempt to further decrease the integration step-size failed.
Suggested course of action:
1. Decrease the value of HMIN.
2. Relax the accuracy requirements (ERROR) on the integrator.
3. Increase the number of iterations allowed for convergence.
4. Revisit the way the mechanical system has been modeled.
Last good step-size: 1.359623232E-08.
STFINT:MIN_STEP_SIZE HMIN=1.000000000E-08; Reached At Time=5.755000000E+01.
The integrator could not advance the simulation.
An attempt to further decrease the integration step-size failed.
Suggested course of action:
1. Decrease the value of HMIN.
2. Relax the accuracy requirements (ERROR) on the integrator.
3. Increase the number of iterations allowed for convergence.
4. Revisit the way the mechanical system has been modeled.
Last good step-size: 1.093545622E-08.
STFINT:MIN_STEP_SIZE HMIN=1.000000000E-08; Reached At Time=5.762000000E+01.
The integrator could not advance the simulation.
An attempt to further decrease the integration step-size failed.
Suggested course of action:
1. Decrease the value of HMIN.
2. Relax the accuracy requirements (ERROR) on the integrator.
3. Increase the number of iterations allowed for convergence.
4. Revisit the way the mechanical system has been modeled.
Last good step-size: 1.346948258E-08.
STFINT:MIN_STEP_SIZE HMIN=1.000000000E-08; Reached At Time=5.773000000E+01.
The integrator could not advance the simulation.
An attempt to further decrease the integration step-size failed.
Suggested course of action:
1. Decrease the value of HMIN.
2. Relax the accuracy requirements (ERROR) on the integrator.
3. Increase the number of iterations allowed for convergence.
4. Revisit the way the mechanical system has been modeled.
Last good step-size: 1.348904494E-08.
STFINT:MIN_STEP_SIZE HMIN=1.000000000E-08; Reached At Time=5.784000000E+01.
The integrator could not advance the simulation.
An attempt to further decrease the integration step-size failed.
Suggested course of action:
1. Decrease the value of HMIN.
2. Relax the accuracy requirements (ERROR) on the integrator.
3. Increase the number of iterations allowed for convergence.
4. Revisit the way the mechanical system has been modeled.
Last good step-size: 1.120464558E-08.
STFINT:MIN_STEP_SIZE HMIN=1.000000000E-08; Reached At Time=5.785000000E+01.
The integrator could not advance the simulation.
An attempt to further decrease the integration step-size failed.
Suggested course of action:
1. Decrease the value of HMIN.
2. Relax the accuracy requirements (ERROR) on the integrator.
3. Increase the number of iterations allowed for convergence.
4. Revisit the way the mechanical system has been modeled.
Last good step-size: 1.571685596E-08.
STFINT:MIN_STEP_SIZE HMIN=1.000000000E-08; Reached At Time=5.790000000E+01.
The integrator could not advance the simulation.
An attempt to further decrease the integration step-size failed.
Suggested course of action:
1. Decrease the value of HMIN.
2. Relax the accuracy requirements (ERROR) on the integrator.
3. Increase the number of iterations allowed for convergence.
4. Revisit the way the mechanical system has been modeled.
Last good step-size: 1.576183364E-08.
STFINT:MIN_STEP_SIZE HMIN=1.000000000E-08; Reached At Time=5.794000000E+01.
The integrator could not advance the simulation.
An attempt to further decrease the integration step-size failed.
Suggested course of action:
1. Decrease the value of HMIN.
2. Relax the accuracy requirements (ERROR) on the integrator.
3. Increase the number of iterations allowed for convergence.
4. Revisit the way the mechanical system has been modeled.
Last good step-size: 1.136120897E-08.
STFINT:MIN_STEP_SIZE HMIN=1.000000000E-08; Reached At Time=5.795000000E+01.
The integrator could not advance the simulation.
An attempt to further decrease the integration step-size failed.
Suggested course of action:
1. Decrease the value of HMIN.
2. Relax the accuracy requirements (ERROR) on the integrator.
3. Increase the number of iterations allowed for convergence.
4. Revisit the way the mechanical system has been modeled.
Last good step-size: 1.466259889E-08.
STFINT:MIN_STEP_SIZE HMIN=1.000000000E-08; Reached At Time=5.802000000E+01.
The integrator could not advance the simulation.
An attempt to further decrease the integration step-size failed.
Suggested course of action:
1. Decrease the value of HMIN.
2. Relax the accuracy requirements (ERROR) on the integrator.
3. Increase the number of iterations allowed for convergence.
4. Revisit the way the mechanical system has been modeled.
Last good step-size: 1.635581835E-08.
STFINT:MIN_STEP_SIZE HMIN=1.000000000E-08; Reached At Time=5.803000000E+01.
The integrator could not advance the simulation.
An attempt to further decrease the integration step-size failed.
Suggested course of action:
1. Decrease the value of HMIN.
2. Relax the accuracy requirements (ERROR) on the integrator.
3. Increase the number of iterations allowed for convergence.
4. Revisit the way the mechanical system has been modeled.
Last good step-size: 2.579866606E-08.
STFINT:MIN_STEP_SIZE HMIN=1.000000000E-08; Reached At Time=5.812000000E+01.
The integrator could not advance the simulation.
An attempt to further decrease the integration step-size failed.
Suggested course of action:
1. Decrease the value of HMIN.
2. Relax the accuracy requirements (ERROR) on the integrator.
3. Increase the number of iterations allowed for convergence.
4. Revisit the way the mechanical system has been modeled.
Last good step-size: 3.091593569E-08.
STFINT:MIN_STEP_SIZE HMIN=1.000000000E-08; Reached At Time=5.813000000E+01.
The integrator could not advance the simulation.
An attempt to further decrease the integration step-size failed.
Suggested course of action:
1. Decrease the value of HMIN.
2. Relax the accuracy requirements (ERROR) on the integrator.
3. Increase the number of iterations allowed for convergence.
4. Revisit the way the mechanical system has been modeled.
Last good step-size: 1.268633957E-08.
STFINT:MIN_STEP_SIZE HMIN=1.000000000E-08; Reached At Time=5.814000000E+01.
The integrator could not advance the simulation.
An attempt to further decrease the integration step-size failed.
Suggested course of action:
1. Decrease the value of HMIN.
2. Relax the accuracy requirements (ERROR) on the integrator.
3. Increase the number of iterations allowed for convergence.
4. Revisit the way the mechanical system has been modeled.
Last good step-size: 2.774257941E-08.
STFINT:MIN_STEP_SIZE HMIN=1.000000000E-08; Reached At Time=5.847000000E+01.
The integrator could not advance the simulation.
An attempt to further decrease the integration step-size failed.
Suggested course of action:
1. Decrease the value of HMIN.
2. Relax the accuracy requirements (ERROR) on the integrator.
3. Increase the number of iterations allowed for convergence.
4. Revisit the way the mechanical system has been modeled.
Last good step-size: 1.352924459E-08.
STFINT:MIN_STEP_SIZE HMIN=1.000000000E-08; Reached At Time=5.852000000E+01.
The integrator could not advance the simulation.
An attempt to further decrease the integration step-size failed.
Suggested course of action:
1. Decrease the value of HMIN.
2. Relax the accuracy requirements (ERROR) on the integrator.
3. Increase the number of iterations allowed for convergence.
4. Revisit the way the mechanical system has been modeled.
Last good step-size: 1.317684002E-08.
STFINT:MIN_STEP_SIZE HMIN=1.000000000E-08; Reached At Time=5.854000000E+01.
The integrator could not advance the simulation.
An attempt to further decrease the integration step-size failed.
Suggested course of action:
1. Decrease the value of HMIN.
2. Relax the accuracy requirements (ERROR) on the integrator.
3. Increase the number of iterations allowed for convergence.
4. Revisit the way the mechanical system has been modeled.
Last good step-size: 1.021133813E-08.
STFINT:MIN_STEP_SIZE HMIN=1.000000000E-08; Reached At Time=5.855000000E+01.
The integrator could not advance the simulation.
An attempt to further decrease the integration step-size failed.
Suggested course of action:
1. Decrease the value of HMIN.
2. Relax the accuracy requirements (ERROR) on the integrator.
3. Increase the number of iterations allowed for convergence.
4. Revisit the way the mechanical system has been modeled.
Last good step-size: 1.751435948E-08.
STFINT:MIN_STEP_SIZE HMIN=1.000000000E-08; Reached At Time=5.856000000E+01.
The integrator could not advance the simulation.
An attempt to further decrease the integration step-size failed.
Suggested course of action:
1. Decrease the value of HMIN.
2. Relax the accuracy requirements (ERROR) on the integrator.
3. Increase the number of iterations allowed for convergence.
4. Revisit the way the mechanical system has been modeled.
Last good step-size: 2.504145194E-08.
STFINT:MIN_STEP_SIZE HMIN=1.000000000E-08; Reached At Time=5.863000000E+01.
The integrator could not advance the simulation.
An attempt to further decrease the integration step-size failed.
Suggested course of action:
1. Decrease the value of HMIN.
2. Relax the accuracy requirements (ERROR) on the integrator.
3. Increase the number of iterations allowed for convergence.
4. Revisit the way the mechanical system has been modeled.
Last good step-size: 1.360748988E-08.
STFINT:MIN_STEP_SIZE HMIN=1.000000000E-08; Reached At Time=5.865000000E+01.
The integrator could not advance the simulation.
An attempt to further decrease the integration step-size failed.
Suggested course of action:
1. Decrease the value of HMIN.
2. Relax the accuracy requirements (ERROR) on the integrator.
3. Increase the number of iterations allowed for convergence.
4. Revisit the way the mechanical system has been modeled.
Last good step-size: 1.181008889E-08.
STFINT:MIN_STEP_SIZE HMIN=1.000000000E-08; Reached At Time=5.867000000E+01.
The integrator could not advance the simulation.
An attempt to further decrease the integration step-size failed.
Suggested course of action:
1. Decrease the value of HMIN.
2. Relax the accuracy requirements (ERROR) on the integrator.
3. Increase the number of iterations allowed for convergence.
4. Revisit the way the mechanical system has been modeled.
Last good step-size: 2.629760666E-08.
STFINT:MIN_STEP_SIZE HMIN=1.000000000E-08; Reached At Time=5.869000000E+01.
The integrator could not advance the simulation.
An attempt to further decrease the integration step-size failed.
Suggested course of action:
1. Decrease the value of HMIN.
2. Relax the accuracy requirements (ERROR) on the integrator.
3. Increase the number of iterations allowed for convergence.
4. Revisit the way the mechanical system has been modeled.
Last good step-size: 1.227114873E-08.
STFINT:MIN_STEP_SIZE HMIN=1.000000000E-08; Reached At Time=5.870000000E+01.
The integrator could not advance the simulation.
An attempt to further decrease the integration step-size failed.
Suggested course of action:
1. Decrease the value of HMIN.
2. Relax the accuracy requirements (ERROR) on the integrator.
3. Increase the number of iterations allowed for convergence.
4. Revisit the way the mechanical system has been modeled.
Last good step-size: 1.398442324E-08.
STFINT:MIN_STEP_SIZE HMIN=1.000000000E-08; Reached At Time=5.872000000E+01.
The integrator could not advance the simulation.
An attempt to further decrease the integration step-size failed.
Suggested course of action:
1. Decrease the value of HMIN.
2. Relax the accuracy requirements (ERROR) on the integrator.
3. Increase the number of iterations allowed for convergence.
4. Revisit the way the mechanical system has been modeled.
Last good step-size: 2.456432940E-08.
STFINT:MIN_STEP_SIZE HMIN=1.000000000E-08; Reached At Time=5.877000000E+01.
The integrator could not advance the simulation.
An attempt to further decrease the integration step-size failed.
Suggested course of action:
1. Decrease the value of HMIN.
2. Relax the accuracy requirements (ERROR) on the integrator.
3. Increase the number of iterations allowed for convergence.
4. Revisit the way the mechanical system has been modeled.
Last good step-size: 1.612340668E-08.
STFINT:MIN_STEP_SIZE HMIN=1.000000000E-08; Reached At Time=5.878000000E+01.
The integrator could not advance the simulation.
An attempt to further decrease the integration step-size failed.
Suggested course of action:
1. Decrease the value of HMIN.
2. Relax the accuracy requirements (ERROR) on the integrator.
3. Increase the number of iterations allowed for convergence.
4. Revisit the way the mechanical system has been modeled.
Last good step-size: 1.364133387E-08.
STFINT:MIN_STEP_SIZE HMIN=1.000000000E-08; Reached At Time=5.882000000E+01.
The integrator could not advance the simulation.
An attempt to further decrease the integration step-size failed.
Suggested course of action:
1. Decrease the value of HMIN.
2. Relax the accuracy requirements (ERROR) on the integrator.
3. Increase the number of iterations allowed for convergence.
4. Revisit the way the mechanical system has been modeled.
Last good step-size: 2.966662959E-08.
STFINT:MIN_STEP_SIZE HMIN=1.000000000E-08; Reached At Time=5.884000000E+01.
The integrator could not advance the simulation.
An attempt to further decrease the integration step-size failed.
Suggested course of action:
1. Decrease the value of HMIN.
2. Relax the accuracy requirements (ERROR) on the integrator.
3. Increase the number of iterations allowed for convergence.
4. Revisit the way the mechanical system has been modeled.
Last good step-size: 1.559977286E-08.
STFINT:MIN_STEP_SIZE HMIN=1.000000000E-08; Reached At Time=5.887000000E+01.
The integrator could not advance the simulation.
An attempt to further decrease the integration step-size failed.
Suggested course of action:
1. Decrease the value of HMIN.
2. Relax the accuracy requirements (ERROR) on the integrator.
3. Increase the number of iterations allowed for convergence.
4. Revisit the way the mechanical system has been modeled.
Last good step-size: 1.023119753E-08.
STFINT:MIN_STEP_SIZE HMIN=1.000000000E-08; Reached At Time=5.888000000E+01.
The integrator could not advance the simulation.
An attempt to further decrease the integration step-size failed.
Suggested course of action:
1. Decrease the value of HMIN.
2. Relax the accuracy requirements (ERROR) on the integrator.
3. Increase the number of iterations allowed for convergence.
4. Revisit the way the mechanical system has been modeled.
Last good step-size: 1.511731316E-08.
STFINT:MIN_STEP_SIZE HMIN=1.000000000E-08; Reached At Time=5.890000000E+01.
The integrator could not advance the simulation.
An attempt to further decrease the integration step-size failed.
Suggested course of action:
1. Decrease the value of HMIN.
2. Relax the accuracy requirements (ERROR) on the integrator.
3. Increase the number of iterations allowed for convergence.
4. Revisit the way the mechanical system has been modeled.
Last good step-size: 1.157932692E-08.
STFINT:MIN_STEP_SIZE HMIN=1.000000000E-08; Reached At Time=5.891000000E+01.
The integrator could not advance the simulation.
An attempt to further decrease the integration step-size failed.
Suggested course of action:
1. Decrease the value of HMIN.
2. Relax the accuracy requirements (ERROR) on the integrator.
3. Increase the number of iterations allowed for convergence.
4. Revisit the way the mechanical system has been modeled.
Last good step-size: 1.318509821E-08.
STFINT:MIN_STEP_SIZE HMIN=1.000000000E-08; Reached At Time=5.892000000E+01.
The integrator could not advance the simulation.
An attempt to further decrease the integration step-size failed.
Suggested course of action:
1. Decrease the value of HMIN.
2. Relax the accuracy requirements (ERROR) on the integrator.
3. Increase the number of iterations allowed for convergence.
4. Revisit the way the mechanical system has been modeled.
Last good step-size: 2.101033921E-08.
STFINT:MIN_STEP_SIZE HMIN=1.000000000E-08; Reached At Time=5.908000000E+01.
The integrator could not advance the simulation.
An attempt to further decrease the integration step-size failed.
Suggested course of action:
1. Decrease the value of HMIN.
2. Relax the accuracy requirements (ERROR) on the integrator.
3. Increase the number of iterations allowed for convergence.
4. Revisit the way the mechanical system has been modeled.
Last good step-size: 2.915244809E-08.
STFINT:MIN_STEP_SIZE HMIN=1.000000000E-08; Reached At Time=5.909000000E+01.
The integrator could not advance the simulation.
An attempt to further decrease the integration step-size failed.
Suggested course of action:
1. Decrease the value of HMIN.
2. Relax the accuracy requirements (ERROR) on the integrator.
3. Increase the number of iterations allowed for convergence.
4. Revisit the way the mechanical system has been modeled.
Last good step-size: 3.915533188E-08.
STFINT:MIN_STEP_SIZE HMIN=1.000000000E-08; Reached At Time=5.910000000E+01.
The integrator could not advance the simulation.
An attempt to further decrease the integration step-size failed.
Suggested course of action:
1. Decrease the value of HMIN.
2. Relax the accuracy requirements (ERROR) on the integrator.
3. Increase the number of iterations allowed for convergence.
4. Revisit the way the mechanical system has been modeled.
Last good step-size: 1.163095477E-08.
STFINT:MIN_STEP_SIZE HMIN=1.000000000E-08; Reached At Time=5.910010344E+01.
The integrator could not advance the simulation.
An attempt to further decrease the integration step-size failed.
Suggested course of action:
1. Decrease the value of HMIN.
2. Relax the accuracy requirements (ERROR) on the integrator.
3. Increase the number of iterations allowed for convergence.
4. Revisit the way the mechanical system has been modeled.
Last good step-size: 3.452081530E-08.
STFINT:MIN_STEP_SIZE HMIN=1.000000000E-08; Reached At Time=5.911000000E+01.
The integrator could not advance the simulation.
An attempt to further decrease the integration step-size failed.
Suggested course of action:
1. Decrease the value of HMIN.
2. Relax the accuracy requirements (ERROR) on the integrator.
3. Increase the number of iterations allowed for convergence.
4. Revisit the way the mechanical system has been modeled.
Last good step-size: 1.536897407E-08.
STFINT:MIN_STEP_SIZE HMIN=1.000000000E-08; Reached At Time=5.912000000E+01.
The integrator could not advance the simulation.
An attempt to further decrease the integration step-size failed.
Suggested course of action:
1. Decrease the value of HMIN.
2. Relax the accuracy requirements (ERROR) on the integrator.
3. Increase the number of iterations allowed for convergence.
4. Revisit the way the mechanical system has been modeled.
Last good step-size: 3.469928182E-08.
STFINT:MIN_STEP_SIZE HMIN=1.000000000E-08; Reached At Time=5.913000000E+01.
The integrator could not advance the simulation.
An attempt to further decrease the integration step-size failed.
Suggested course of action:
1. Decrease the value of HMIN.
2. Relax the accuracy requirements (ERROR) on the integrator.
3. Increase the number of iterations allowed for convergence.
4. Revisit the way the mechanical system has been modeled.
Last good step-size: 1.898442316E-08.
STFINT:MIN_STEP_SIZE HMIN=1.000000000E-08; Reached At Time=5.914000000E+01.
The integrator could not advance the simulation.
An attempt to further decrease the integration step-size failed.
Suggested course of action:
1. Decrease the value of HMIN.
2. Relax the accuracy requirements (ERROR) on the integrator.
3. Increase the number of iterations allowed for convergence.
4. Revisit the way the mechanical system has been modeled.
Last good step-size: 3.679658324E-08.
STFINT:MIN_STEP_SIZE HMIN=1.000000000E-08; Reached At Time=5.915000000E+01.
The integrator could not advance the simulation.
An attempt to further decrease the integration step-size failed.
Suggested course of action:
1. Decrease the value of HMIN.
2. Relax the accuracy requirements (ERROR) on the integrator.
3. Increase the number of iterations allowed for convergence.
4. Revisit the way the mechanical system has been modeled.
Last good step-size: 3.735121450E-08.
STFINT:MIN_STEP_SIZE HMIN=1.000000000E-08; Reached At Time=5.916000000E+01.
The integrator could not advance the simulation.
An attempt to further decrease the integration step-size failed.
Suggested course of action:
1. Decrease the value of HMIN.
2. Relax the accuracy requirements (ERROR) on the integrator.
3. Increase the number of iterations allowed for convergence.
4. Revisit the way the mechanical system has been modeled.
Last good step-size: 1.978423952E-08.
STFINT:MIN_STEP_SIZE HMIN=1.000000000E-08; Reached At Time=5.917000000E+01.
The integrator could not advance the simulation.
An attempt to further decrease the integration step-size failed.
Suggested course of action:
1. Decrease the value of HMIN.
2. Relax the accuracy requirements (ERROR) on the integrator.
3. Increase the number of iterations allowed for convergence.
4. Revisit the way the mechanical system has been modeled.
Last good step-size: 3.231917852E-08.
STFINT:MIN_STEP_SIZE HMIN=1.000000000E-08; Reached At Time=5.918000000E+01.
The integrator could not advance the simulation.
An attempt to further decrease the integration step-size failed.
Suggested course of action:
1. Decrease the value of HMIN.
2. Relax the accuracy requirements (ERROR) on the integrator.
3. Increase the number of iterations allowed for convergence.
4. Revisit the way the mechanical system has been modeled.
Last good step-size: 4.126851332E-08.
STFINT:MIN_STEP_SIZE HMIN=1.000000000E-08; Reached At Time=5.919000000E+01.
The integrator could not advance the simulation.
An attempt to further decrease the integration step-size failed.
Suggested course of action:
1. Decrease the value of HMIN.
2. Relax the accuracy requirements (ERROR) on the integrator.
3. Increase the number of iterations allowed for convergence.
4. Revisit the way the mechanical system has been modeled.
Last good step-size: 1.586853770E-08.
STFINT:MIN_STEP_SIZE HMIN=1.000000000E-08; Reached At Time=5.920000000E+01.
The integrator could not advance the simulation.
An attempt to further decrease the integration step-size failed.
Suggested course of action:
1. Decrease the value of HMIN.
2. Relax the accuracy requirements (ERROR) on the integrator.
3. Increase the number of iterations allowed for convergence.
4. Revisit the way the mechanical system has been modeled.
Last good step-size: 2.567768974E-08.
STFINT:MIN_STEP_SIZE HMIN=1.000000000E-08; Reached At Time=5.921000000E+01.
The integrator could not advance the simulation.
An attempt to further decrease the integration step-size failed.
Suggested course of action:
1. Decrease the value of HMIN.
2. Relax the accuracy requirements (ERROR) on the integrator.
3. Increase the number of iterations allowed for convergence.
4. Revisit the way the mechanical system has been modeled.
Last good step-size: 3.296201693E-08.
STFINT:MIN_STEP_SIZE HMIN=1.000000000E-08; Reached At Time=5.922000000E+01.
The integrator could not advance the simulation.
An attempt to further decrease the integration step-size failed.
Suggested course of action:
1. Decrease the value of HMIN.
2. Relax the accuracy requirements (ERROR) on the integrator.
3. Increase the number of iterations allowed for convergence.
4. Revisit the way the mechanical system has been modeled.
Last good step-size: 2.671155612E-08.
STFINT:MIN_STEP_SIZE HMIN=1.000000000E-08; Reached At Time=5.923000000E+01.
The integrator could not advance the simulation.
An attempt to further decrease the integration step-size failed.
Suggested course of action:
1. Decrease the value of HMIN.
2. Relax the accuracy requirements (ERROR) on the integrator.
3. Increase the number of iterations allowed for convergence.
4. Revisit the way the mechanical system has been modeled.
Last good step-size: 1.637524089E-08.
STFINT:MIN_STEP_SIZE HMIN=1.000000000E-08; Reached At Time=5.924000000E+01.
The integrator could not advance the simulation.
An attempt to further decrease the integration step-size failed.
Suggested course of action:
1. Decrease the value of HMIN.
2. Relax the accuracy requirements (ERROR) on the integrator.
3. Increase the number of iterations allowed for convergence.
4. Revisit the way the mechanical system has been modeled.
Last good step-size: 1.062767277E-08.
STFINT:MIN_STEP_SIZE HMIN=1.000000000E-08; Reached At Time=5.925000000E+01.
The integrator could not advance the simulation.
An attempt to further decrease the integration step-size failed.
Suggested course of action:
1. Decrease the value of HMIN.
2. Relax the accuracy requirements (ERROR) on the integrator.
3. Increase the number of iterations allowed for convergence.
4. Revisit the way the mechanical system has been modeled.
Last good step-size: 2.008101422E-08.
STFINT:MIN_STEP_SIZE HMIN=1.000000000E-08; Reached At Time=5.926000000E+01.
The integrator could not advance the simulation.
An attempt to further decrease the integration step-size failed.
Suggested course of action:
1. Decrease the value of HMIN.
2. Relax the accuracy requirements (ERROR) on the integrator.
3. Increase the number of iterations allowed for convergence.
4. Revisit the way the mechanical system has been modeled.
Last good step-size: 1.045900172E-08.
STFINT:MIN_STEP_SIZE HMIN=1.000000000E-08; Reached At Time=5.926999944E+01.
The integrator could not advance the simulation.
An attempt to further decrease the integration step-size failed.
Suggested course of action:
1. Decrease the value of HMIN.
2. Relax the accuracy requirements (ERROR) on the integrator.
3. Increase the number of iterations allowed for convergence.
4. Revisit the way the mechanical system has been modeled.
Last good step-size: 1.210867447E-08.
---- START: ERROR ----
The integrator is unable to proceed. Possible Causes:
(1) The accuracy required for the numerical solution can not be attained.
Relax (increase) the value of the acceptable integration ERROR.
(2) Incompatible redundant constraints, a lock up, or a bifurcation
situation. The latter two indicate a mechanism design problem.
(3) The system includes a zero (or relatively small) mass on a part with
an unconstrained translational degree of freedom.
Make sure you have mass on all parts with translational degrees of freedom.
(4) The system includes a zero (or relatively small) inertia on a part
with an unconstrained rotational degree of freedom.
Make sure you have inertias on all parts with rotational degrees of freedom.
(5) An Adams element has a function expression that equals exactly itself.
For example,
SFORCE/id1,I=id2,J=id3,ROT,FUNC=SFORCE(id1,jflag,comp,rm),and
DIFF/id4,IMPLICIT,IC=0,FUNC=DIF1(id4).
Similarly,
VARIABLE/id5, FUNC=VARVAL(id5)*TIME
equals itself at 1 second. Avoid setting an Adams element equal to itself.
Simulation time is 5.927542149E+01
Simulation time is 5.927542149E+01
---- END: ERROR ----
Dynamic Solution stopped.
End Simulation
Simulate status=-124
---- START: ERROR ----
SIMULATE command failed for minimaneuver: ADAMS_SMART_DRIVER
Aborting Execution.
Simulation time is 5.927542149E+01
---- END: ERROR ----
---- START: ERROR ----
Adams Solver (C++) run terminating due to STOP requested by user.
Simulation time is 5.927542149E+01
---- END: ERROR ----
Termination status=-995
Terminating Adams Car usersubs...
Finished -----
Elapsed time = 1055.54s, CPU time = 1073.20s, 101.67%
Simulation is complete.

As you can see our model, goes out in last corner.
I hope to see your help.