Hi everyone, I've recently been using Abaqus/Explicit to do a finite element simulation of 2D metal cutting using the ALE method, and I've seen a blogger on YouTube do a similar simulation( Still, his results are much more normal than mine. Doesn't ALE normally allow for mesh adaptation? Why is it that when I use ALE to simulate the cutting process, I can't get the chips at all? The tool isn't able to remove the chips from the workpiece. Rather, it only creates a bend in the area over workpiece. The mesh in the workpiece and tool contact area is not adaptive either; it is still badly distorted. I have followed in the Step module: Other→ALE Adaptive Mesh Domain→Edit, toggle on "Use the ALE adaptive mesh domain below" and click Edit to select the region ( undeformed chip region) and turn off the "distortion control" for the workpiece mesh. I also switch to the "ALE Adaptive Mesh Controls" and set. In the attachment is my .inp file. Where did I set it wrong? Please help me. Thank you very much!
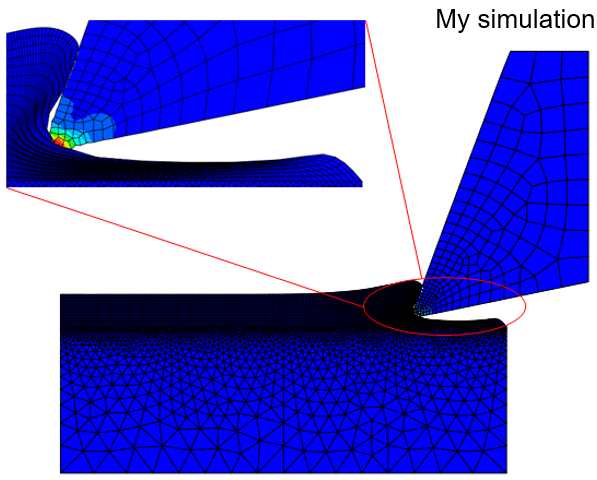
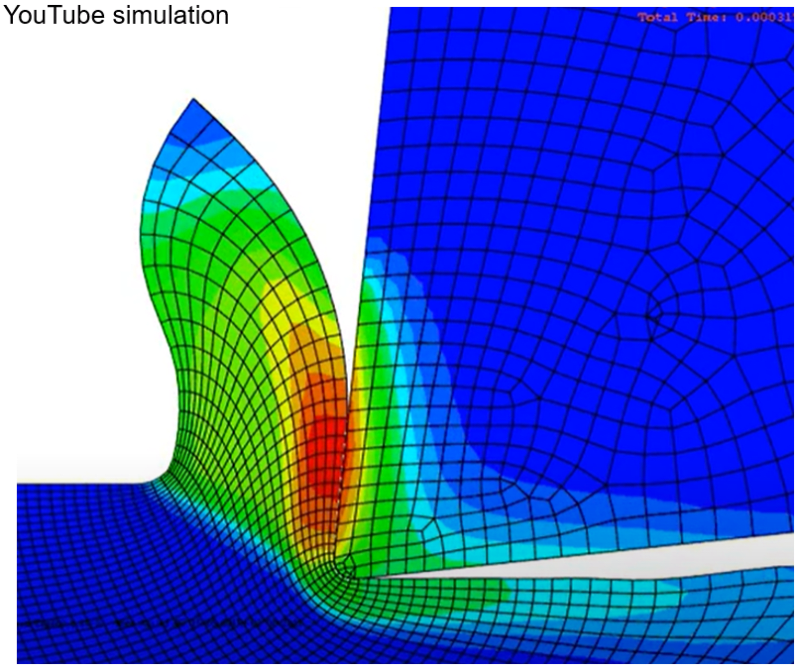