Znjmech
Mechanical
- Dec 19, 2016
- 94
Hello All
Apart from what the functioning and conditions are. I'd like to ask you guys , if you could tell me whether this solutuon needs to be corrected to avoid leakages. Currently, the cover is to be screwed down up to the point that it doesn't press the O ring ( why ?)
while the o - ring installation is quite a nasty job, since the inside plating might be to high and the O ring might not slide at its correct position. Mean while there might occure other problems like the ovality of the container or the impreciseness of the threading.
Is there any improvement in the geometry of this design that could reduce the effects that I mentioned to reduce the leakage?
Apart from what the functioning and conditions are. I'd like to ask you guys , if you could tell me whether this solutuon needs to be corrected to avoid leakages. Currently, the cover is to be screwed down up to the point that it doesn't press the O ring ( why ?)
while the o - ring installation is quite a nasty job, since the inside plating might be to high and the O ring might not slide at its correct position. Mean while there might occure other problems like the ovality of the container or the impreciseness of the threading.
Is there any improvement in the geometry of this design that could reduce the effects that I mentioned to reduce the leakage?
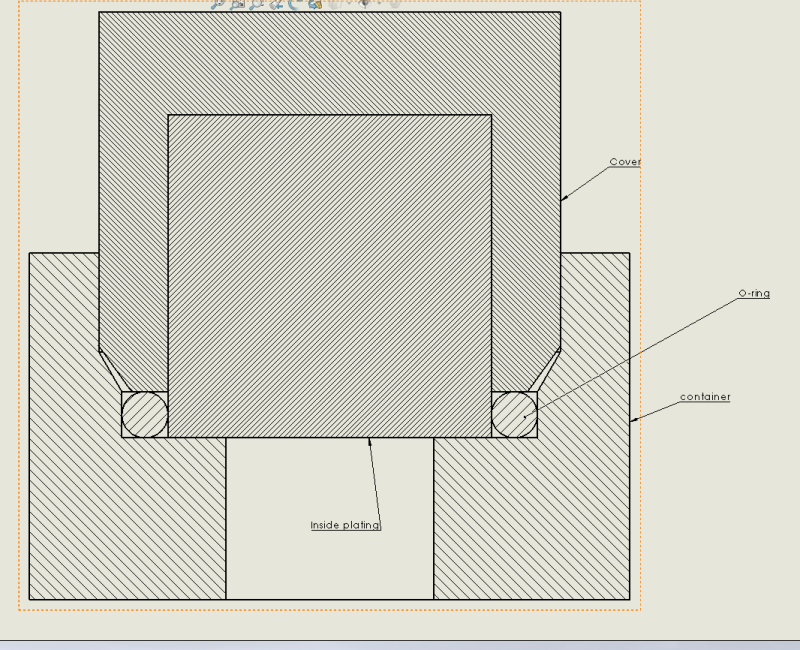