KootK
Structural
- Oct 16, 2001
- 18,563
Disclaimer: this is a lazy man's post. I am indeed asking responders to do research that I could surely do myself given enough time and fee (I long ago ran out of both).
I need to design the aluminum thing shown below for wind and guardrail-ish loads (related to another recent thread of mine). Biaxial flexure on an unbraced z-ish section. A common configuration is coming up failing badly (even just wind), I've got twenty pages of near meaningless aluminum calcs that read like Egyptian hieroglyph, and I've been rotating axes like I was back in second year college. I just feels as though it should not be this hard.
So, my desperate questions are:
1) Wind. Folks seem to agree on treating the thing as solid. However, with that decision taken, do you then apply that same horizontal wind load to the blade as a 45 degree load? Wind does only act perpendicularly to surfaces after all. It makes a big difference as 25 psf "wall" load then becomes 25 PSF weak-ish axis load.
2) Is there any better design resource to be using other than the Aluminum Association's Aluminum Design Manual. I'd sacrifice a thumb for a damn table of flexural capacities.
3) As much as it shames me to ask this, anybody got a worked example that they could point me to?
I like to debate structural engineering theory -- a lot. If I challenge you on something, know that I'm doing so because I respect your opinion enough to either change it or adopt it.
I need to design the aluminum thing shown below for wind and guardrail-ish loads (related to another recent thread of mine). Biaxial flexure on an unbraced z-ish section. A common configuration is coming up failing badly (even just wind), I've got twenty pages of near meaningless aluminum calcs that read like Egyptian hieroglyph, and I've been rotating axes like I was back in second year college. I just feels as though it should not be this hard.
So, my desperate questions are:
1) Wind. Folks seem to agree on treating the thing as solid. However, with that decision taken, do you then apply that same horizontal wind load to the blade as a 45 degree load? Wind does only act perpendicularly to surfaces after all. It makes a big difference as 25 psf "wall" load then becomes 25 PSF weak-ish axis load.
2) Is there any better design resource to be using other than the Aluminum Association's Aluminum Design Manual. I'd sacrifice a thumb for a damn table of flexural capacities.
3) As much as it shames me to ask this, anybody got a worked example that they could point me to?
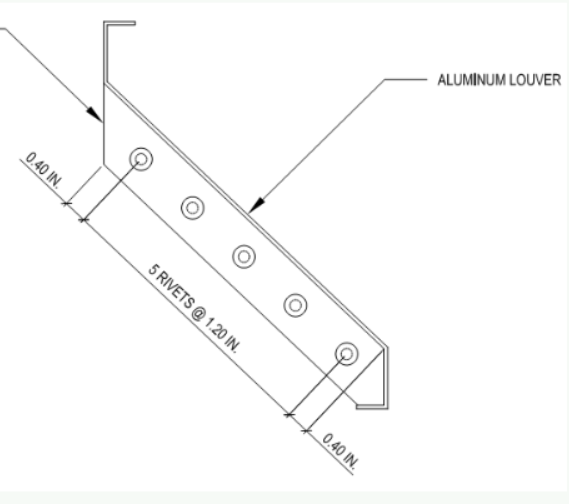
I like to debate structural engineering theory -- a lot. If I challenge you on something, know that I'm doing so because I respect your opinion enough to either change it or adopt it.