Dear All,
We recently observed some cracks on one of our Ammonia Let Down Vessel. Mentioned below are brief details of the equipment:
Service: Ammonia
Shell Material: A516 Gr. 60 N
Operating Temperature : 2oC
Operating Pressure: 26 kg/cm2 g
Shell Thickness: 32 mm
PWHT: Yes
Vessel Orientation: Horizontal
While Ammonia SCC is the common cause of cracks observed on Ammonia service equipment, the orientation and shape of these cracks is somewhat different than what we have observed in the past. Depth of the crack varied between 8 mm to 15 mm. Spot hardness was measured on the vessel and while most of the readings were within acceptable range, hardness readings near cracked nozzles was observed to be as high as 273 HB with an average value of 200 HB. Attached is picture of one of the nozzles with these cracks. Need your expert opinion on the possible causes of these cracks and in particularly what does the shape of cracks indicate regarding the stresses present in the vessel.
Regards,
Ahsan
We recently observed some cracks on one of our Ammonia Let Down Vessel. Mentioned below are brief details of the equipment:
Service: Ammonia
Shell Material: A516 Gr. 60 N
Operating Temperature : 2oC
Operating Pressure: 26 kg/cm2 g
Shell Thickness: 32 mm
PWHT: Yes
Vessel Orientation: Horizontal
While Ammonia SCC is the common cause of cracks observed on Ammonia service equipment, the orientation and shape of these cracks is somewhat different than what we have observed in the past. Depth of the crack varied between 8 mm to 15 mm. Spot hardness was measured on the vessel and while most of the readings were within acceptable range, hardness readings near cracked nozzles was observed to be as high as 273 HB with an average value of 200 HB. Attached is picture of one of the nozzles with these cracks. Need your expert opinion on the possible causes of these cracks and in particularly what does the shape of cracks indicate regarding the stresses present in the vessel.
Regards,
Ahsan
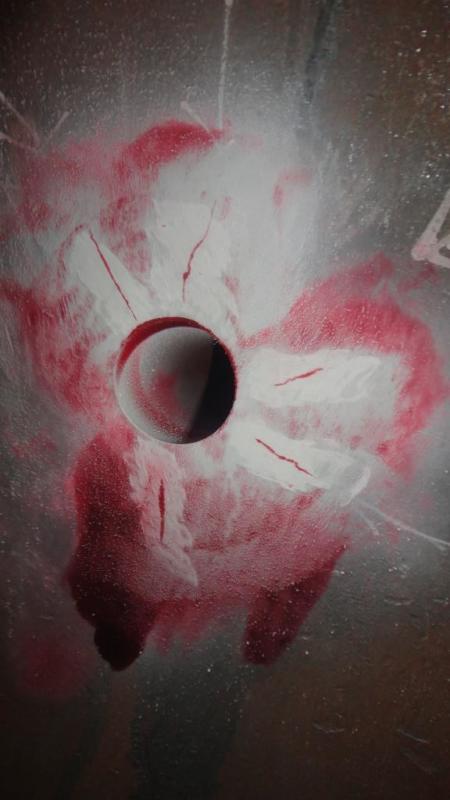