BlasMolero
Mechanical
Hello!,
I should like to send a request to the FEMAP community at ENG-TIPS to share a Femap API to perform the NEUBER's Correction to reduce the apparent high stresses caused by geometric stress concentrations in the fine mesh of the Finite Element model results after running Simcenter Nastran (SOL101) linear static solver.
Please note after solving a linear static analysis using a refined mesh with an excellent quality the linear static results includes geometric Kt effects reporting high elastic stress values.
[highlight #FCE94F]Using these stress results to size the component or select a material is incorrect[/highlight]. It will be conservative and the part will be heavy.
The alternative is to run a fully nonlinear analysis activating all nonlinearities of material & geometry (large displacement effects & contact), yes, but the cost in solution time & computation resources is important compared with a fast linear static analysis.
THE NEUBER METHOD
Using the documentation of the winLIFE Fatigue Analysis code that I run with FEMAP (see I will explain the different types of stresses used in a fatigue analysis computation:
[ul]
[li]Nominal Stress[/li]
[li]Local Elastic Stress[/li]
[li]Local Real Stress[/li]
[/ul]
A simple rectangular plate with a hole is under study (see figure below) loaded by two opposite force F in the longitudinal direction. Also below is the material stress-strain curve, that includes the real nonlinear stress-strain curve (in red) and the linear elastic stress-strain curve based in Hooke's Law (in blue).
• The "Nominal Stress Sn" located on the real stress-strain curve (Point P1) can be transformed by the Neuber hyperbola into an equivalent "Elastic Stress Sn*" (Point P2).
• Multiplying this stress with the factor Kt the "Elastic Stress Smax*" in the notch is got (Point P3).
• This again can be transformed by a Neuber hyperbola into the "Real Stress Smax" (Point P4).
• To predict the stress reduction the Neuber’s theory is used. The "Real Stress Smax" is calculated bearing in mind the stress reduction through plastic deformation.
• For the construction of Neuber curves is required to have the linear elastic stress-strain curve, the real cyclic stress-strain curve and the two hyperbolas.
• Neuber’s rule helps to predict the "Real Stress Smax" considering plastic deformation using only calculated elastic stresses, this is the key.
To learn more:
Best regards,
Blas.
~~~~~~~~~~~~~~~~~~~~~~
Blas Molero Hidalgo
Ingeniero Industrial
Director
IBERISA
48004 BILBAO (SPAIN)
WEB: Blog de FEMAP & NX Nastran:
I should like to send a request to the FEMAP community at ENG-TIPS to share a Femap API to perform the NEUBER's Correction to reduce the apparent high stresses caused by geometric stress concentrations in the fine mesh of the Finite Element model results after running Simcenter Nastran (SOL101) linear static solver.
Please note after solving a linear static analysis using a refined mesh with an excellent quality the linear static results includes geometric Kt effects reporting high elastic stress values.
[highlight #FCE94F]Using these stress results to size the component or select a material is incorrect[/highlight]. It will be conservative and the part will be heavy.
The alternative is to run a fully nonlinear analysis activating all nonlinearities of material & geometry (large displacement effects & contact), yes, but the cost in solution time & computation resources is important compared with a fast linear static analysis.
THE NEUBER METHOD
Using the documentation of the winLIFE Fatigue Analysis code that I run with FEMAP (see I will explain the different types of stresses used in a fatigue analysis computation:
[ul]
[li]Nominal Stress[/li]
[li]Local Elastic Stress[/li]
[li]Local Real Stress[/li]
[/ul]
A simple rectangular plate with a hole is under study (see figure below) loaded by two opposite force F in the longitudinal direction. Also below is the material stress-strain curve, that includes the real nonlinear stress-strain curve (in red) and the linear elastic stress-strain curve based in Hooke's Law (in blue).
• The "Nominal Stress Sn" located on the real stress-strain curve (Point P1) can be transformed by the Neuber hyperbola into an equivalent "Elastic Stress Sn*" (Point P2).
• Multiplying this stress with the factor Kt the "Elastic Stress Smax*" in the notch is got (Point P3).
• This again can be transformed by a Neuber hyperbola into the "Real Stress Smax" (Point P4).
• To predict the stress reduction the Neuber’s theory is used. The "Real Stress Smax" is calculated bearing in mind the stress reduction through plastic deformation.
• For the construction of Neuber curves is required to have the linear elastic stress-strain curve, the real cyclic stress-strain curve and the two hyperbolas.
• Neuber’s rule helps to predict the "Real Stress Smax" considering plastic deformation using only calculated elastic stresses, this is the key.
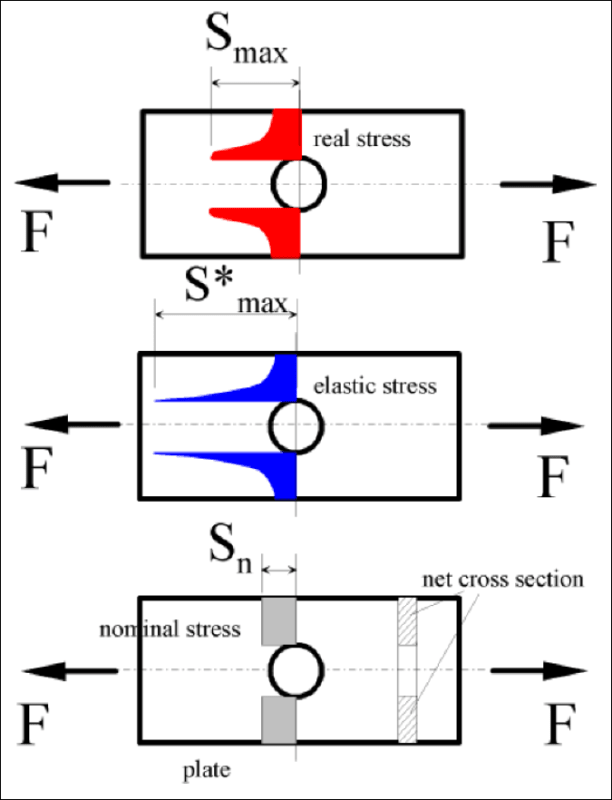
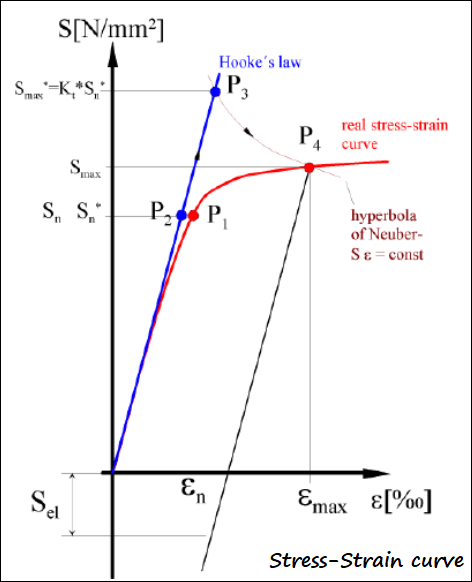
To learn more:
Best regards,
Blas.
~~~~~~~~~~~~~~~~~~~~~~
Blas Molero Hidalgo
Ingeniero Industrial
Director
IBERISA
48004 BILBAO (SPAIN)
WEB: Blog de FEMAP & NX Nastran: