AppletonBowen
Mechanical
Good morning Guys,
I have a question regarding ASME BPVC Sec VIII-1 Appendix Y flanges (Flat Face).
I am in the process of recalc'ing some fairly well-used pressure test equipment, used regularly up to 450bar.
The vessel is constructed from a cylinder with an flanged face fully constrained within the cylinder body - i.e. A=B+2g (see image).
As such, when I calculate these flanges as an App.2, I usually pick some arbitrary thickness, t. Typically I choose a thickness which is approximately the bolt hole depth. I have not had issue with App.2 flange calculations - although would welcome any suggestions of a better method if anyone has any ideas?
The issue I am having with these App. Y flanges is that, because the stresses in the Flange II are a product of the relative stiffnesses, my usual method of t=approx bolt depth, will yield seemingly sensible stresses, however, if I increase the Flange I thickness to ~2x, the Flange II stresses go wild - I believe due to the hugely increased calculated stiffness of the Flange I.
Has anyone got any ideas when trying to calculate bolted connections with no 'flanged' section (i.e. A=B+2g as in image?)
Any help much appreciated.
Rob
I have a question regarding ASME BPVC Sec VIII-1 Appendix Y flanges (Flat Face).
I am in the process of recalc'ing some fairly well-used pressure test equipment, used regularly up to 450bar.
The vessel is constructed from a cylinder with an flanged face fully constrained within the cylinder body - i.e. A=B+2g (see image).
As such, when I calculate these flanges as an App.2, I usually pick some arbitrary thickness, t. Typically I choose a thickness which is approximately the bolt hole depth. I have not had issue with App.2 flange calculations - although would welcome any suggestions of a better method if anyone has any ideas?
The issue I am having with these App. Y flanges is that, because the stresses in the Flange II are a product of the relative stiffnesses, my usual method of t=approx bolt depth, will yield seemingly sensible stresses, however, if I increase the Flange I thickness to ~2x, the Flange II stresses go wild - I believe due to the hugely increased calculated stiffness of the Flange I.
Has anyone got any ideas when trying to calculate bolted connections with no 'flanged' section (i.e. A=B+2g as in image?)
Any help much appreciated.
Rob
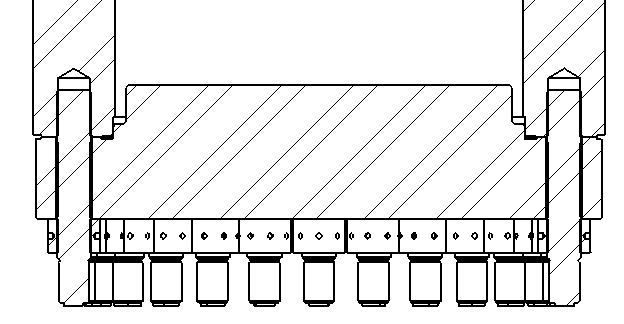