Hi,
I have a mechanism with a disc that has a slot in it. An arm is connected to the slot with a sliding connection. The arm is held at one end with a fixed pivot position. When the disc rotates the arm can move up and down within the slot and its angular position is related to the angular rotation of the disc. Images are below.
I have two questions that I am struggling with:
1. If I apply a torque to rotate the disc how do I calculate the force that is applied to the arm
2. Is there an optimum design of the slot which maximizes the force transfer (curved, straight, 45° to arm axis etc..)
Thanks
I have a mechanism with a disc that has a slot in it. An arm is connected to the slot with a sliding connection. The arm is held at one end with a fixed pivot position. When the disc rotates the arm can move up and down within the slot and its angular position is related to the angular rotation of the disc. Images are below.
I have two questions that I am struggling with:
1. If I apply a torque to rotate the disc how do I calculate the force that is applied to the arm
2. Is there an optimum design of the slot which maximizes the force transfer (curved, straight, 45° to arm axis etc..)
Thanks
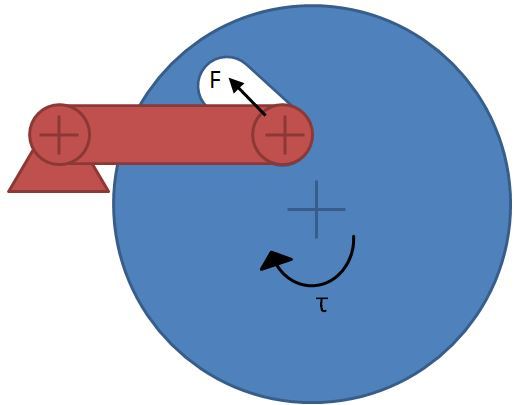
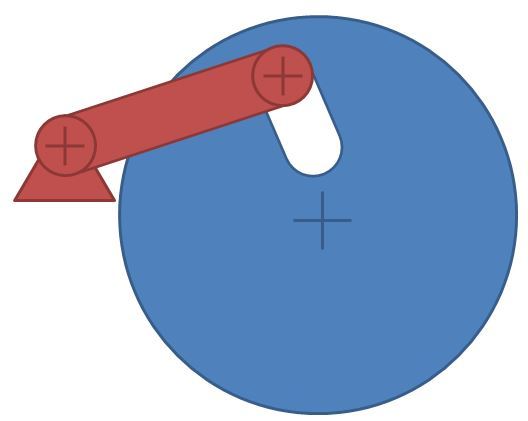