Hello,
I run a FEM analysis with ANSYS Workbench on a steel thin disk-plate (please see pic.)
. The check for the structural integrity of the disk is according to ASME codes Sec.VIII div 2 Part 5 (I assumed the codes could be applied even if my component is not a pressure vessel...), but I am not sure if I followed the right procedure. I looked at some past threads at the forum, but I didn't get a clear answer at my questions. So:
I ran an elastic analysis and made the stress intensity linearization at the cross section with the highest Stress Intensity. I found the membrane(M) and membrane+bending(M+B) stresses and they are found to be lower than the limits of 1S and 1.5S referred to ASME codes Sec.VIII div 2, 5.2.2. So I checked that my cross section is OK regarding plastic collapse. I also calculated the sum of the 3 principal stresses and it is lower than the 4S limit refered to (5.3.2). So the disk passes the local failure check.
However, through the stress linearization I observed that I have some peak stresses extended at a tiny area (1.8 % of thickness) at the upper and lower surfaces of the disk and with their value up to about 2S. What should I 'do' with these peak stresses if my load is static and therefore a fatigue analysis has no meaning..?
Moreover,if I run a elastic-plastic analysis, the ASME codes Sec.VIII div 2, 5.2.4 suggests the use of a factored load, but I do not understand the criterion for verifying that a location at my disk will not collapse through plasticity. What exactly does the 'non-convergence' of analysis mean?
Thanks a lot!
I run a FEM analysis with ANSYS Workbench on a steel thin disk-plate (please see pic.)
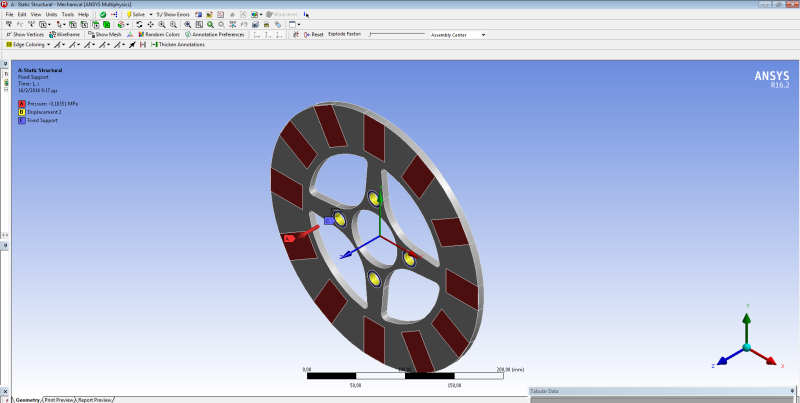
I ran an elastic analysis and made the stress intensity linearization at the cross section with the highest Stress Intensity. I found the membrane(M) and membrane+bending(M+B) stresses and they are found to be lower than the limits of 1S and 1.5S referred to ASME codes Sec.VIII div 2, 5.2.2. So I checked that my cross section is OK regarding plastic collapse. I also calculated the sum of the 3 principal stresses and it is lower than the 4S limit refered to (5.3.2). So the disk passes the local failure check.
However, through the stress linearization I observed that I have some peak stresses extended at a tiny area (1.8 % of thickness) at the upper and lower surfaces of the disk and with their value up to about 2S. What should I 'do' with these peak stresses if my load is static and therefore a fatigue analysis has no meaning..?
Moreover,if I run a elastic-plastic analysis, the ASME codes Sec.VIII div 2, 5.2.4 suggests the use of a factored load, but I do not understand the criterion for verifying that a location at my disk will not collapse through plasticity. What exactly does the 'non-convergence' of analysis mean?
Thanks a lot!