Hello,
I would like to understand how can be inputed the following load cases in PV Elite for a fixed tubesheet:
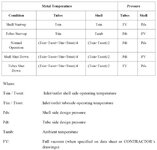
PV Elite has two main windows for these data:
(1) General windows "Load Cases":
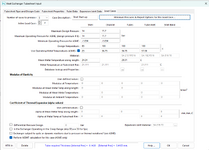
(2) Minimum Pressures & Report Options for this Load Case:
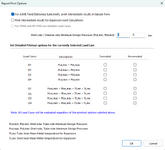
I assumed that, according to the first table in the post, in the "Load Cases" screen, it is necessary to set 5 as the "Number of cases to process" and first fill in the data in the "Load Cases" screen. For this reason, I would need some help: for example, considering only the "Shell Start-up" case, where we need to take into account the inlet temperature on the shell side for tubes and shell (20 °C), while for the pressures, we need to enter the design pressure on the shell side (14 barg) and FV on the tube side. Is it correct to fill in the first screen as shown below?
The question is whether Full Vacuum pressures need to be specified with the "-" sign in the "Load Cases" screen.
Additionally, in the "Minimum Pressures & Report ..." screen, is it necessary to specify the minimum design pressures again (respectively, for the Shell Start-up case, 14 barg on the shell side and -1.034 barg on the tube side)?
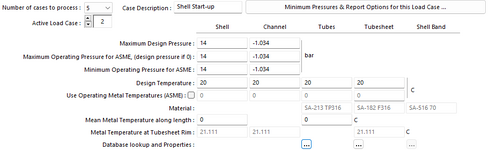
and for the second pop-up window I selected all the items:
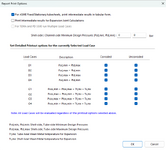
Could you please help?
Thanks in advance
I would like to understand how can be inputed the following load cases in PV Elite for a fixed tubesheet:
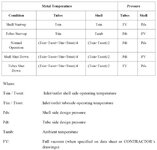
PV Elite has two main windows for these data:
(1) General windows "Load Cases":
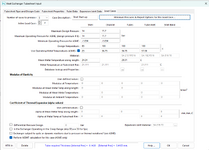
(2) Minimum Pressures & Report Options for this Load Case:
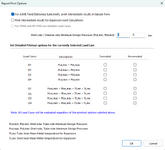
I assumed that, according to the first table in the post, in the "Load Cases" screen, it is necessary to set 5 as the "Number of cases to process" and first fill in the data in the "Load Cases" screen. For this reason, I would need some help: for example, considering only the "Shell Start-up" case, where we need to take into account the inlet temperature on the shell side for tubes and shell (20 °C), while for the pressures, we need to enter the design pressure on the shell side (14 barg) and FV on the tube side. Is it correct to fill in the first screen as shown below?
The question is whether Full Vacuum pressures need to be specified with the "-" sign in the "Load Cases" screen.
Additionally, in the "Minimum Pressures & Report ..." screen, is it necessary to specify the minimum design pressures again (respectively, for the Shell Start-up case, 14 barg on the shell side and -1.034 barg on the tube side)?
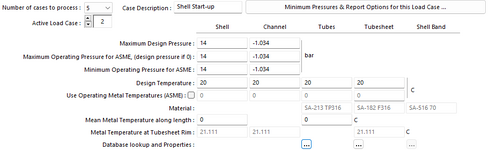
and for the second pop-up window I selected all the items:
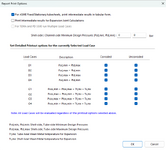
Could you please help?
Thanks in advance