Hello Forum,
We are designing a pressure vessel as per ASME Sec VIII Div 1. For one of the part which is neither standard nor there exist design & construction requirements for such parts in this div, hence we have to use the U-2(g) to comply with this div. Please refer below image which nearly represent the part design concept. The part is purely under bending due to pressure load. As per the FEA results, the bending stresses are very low and are within the allowable tensile stress limits as given in Sec II part D except the notch portion as shown in the picture. For this notch, can we use the higher allowable stress as per UG-23(e) i.e., localized discontinuity stress as 3 times allow stress? Although it seems to be a perfect corner at notch, there will be suitable fillet rad & same is already modelled during the FEA as well.
Do share your opinion.
GD_P
We are designing a pressure vessel as per ASME Sec VIII Div 1. For one of the part which is neither standard nor there exist design & construction requirements for such parts in this div, hence we have to use the U-2(g) to comply with this div. Please refer below image which nearly represent the part design concept. The part is purely under bending due to pressure load. As per the FEA results, the bending stresses are very low and are within the allowable tensile stress limits as given in Sec II part D except the notch portion as shown in the picture. For this notch, can we use the higher allowable stress as per UG-23(e) i.e., localized discontinuity stress as 3 times allow stress? Although it seems to be a perfect corner at notch, there will be suitable fillet rad & same is already modelled during the FEA as well.
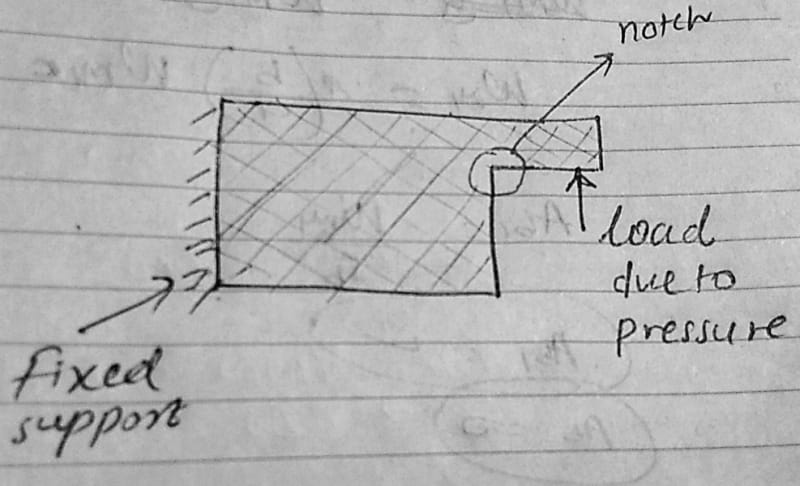
Do share your opinion.
GD_P