Hi guys, I'm reviewing a vessel design (VIII-1) and was hoping to get some assistance/back-check on something I cant seem to get my head around. Couldn't find any related older topics ..
A female threaded nut (pos 3) is used to push an insert (pos 8) on the shell (pos 1). The sealing is achieved by an O-ring (pos 4) between pos 1 and 8. The shell also has straight threads that mate with the nut, indicated in red.
I'm not overly familiar with app Y, but understand from the scope that App Y is for flanges that have metal-to-metal contact outside the bolt circle. Considering the threads as my 'bolt circle', I'm thinking this design doesn't satisfy that condition of metal-to-metal contact outside the bcd. This more seems like a loose flange type design, e.g. per figure 2-4 (1), since the nut acts as a flange pressing the insert (a lap) to the counterpart.
Any thoughts or confirmation this should be considered a loose type flange per fig 2-4 (1)?
Huub
- You never get what you expect, you only get what you inspect.
A female threaded nut (pos 3) is used to push an insert (pos 8) on the shell (pos 1). The sealing is achieved by an O-ring (pos 4) between pos 1 and 8. The shell also has straight threads that mate with the nut, indicated in red.
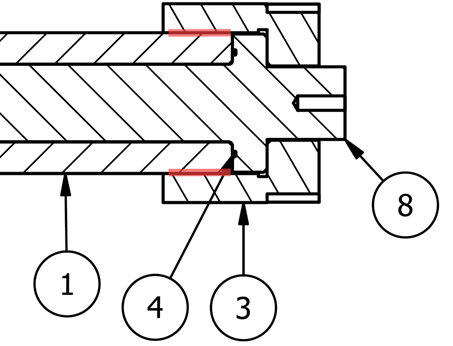
I'm not overly familiar with app Y, but understand from the scope that App Y is for flanges that have metal-to-metal contact outside the bolt circle. Considering the threads as my 'bolt circle', I'm thinking this design doesn't satisfy that condition of metal-to-metal contact outside the bcd. This more seems like a loose flange type design, e.g. per figure 2-4 (1), since the nut acts as a flange pressing the insert (a lap) to the counterpart.
Any thoughts or confirmation this should be considered a loose type flange per fig 2-4 (1)?
Huub
- You never get what you expect, you only get what you inspect.