SprinklerDesigner2
Mechanical
Assume city water supply with results obtained by a flow test.
In the absence of a fire booster pump other than the finished floor of the building, which I always assign an elevation of 0.00 feet, the only elevation that I am concerned with is the elevation of the source node relative to the finished floor of the building.
The source elevation will be the elevation of the 2 1/2" hydrant butt where we obtained our static and residual pressures.
In the drawing below my source elevation is 8.25' above the finished floor of the building.
If this were a dead end main our source would be the hydrant tee assuming the flow from from the fire hydrant to the 8"x8" tapping sleeve. When calculating we would flow our water to the hydrant tee. We all know if it were a dead end main we would want to flow the hydrant downstream the tapping valve but, in this case, let's assume the hydrant shown is the last on the line. If the flow was the other direction, if the hydrant was downstream the tap, we would calculate to the tap.
Actually, if we wanted to get really technical if the hydrant was downstream the tap I would actually be able to add the friction loss developed between the hydrant and the tee but nobody does this.... well, I did once but I needed the extra pressure.
Anyway, assuming a circulating main my source node would be the tapping sleeve but the elevation of the sleeve wouldn't be 5' under the ground but would be the exact same elevation as the hydrant butt used to obtain static and residual pressures.
For our purposes once the source elevation is assigned to 8.25' AFF the calculations would be correct and it really doesn't matter how deep that tapping sleeve is because it doesn't have an impact. For all I are that tapping sleeve could be 100' under the ground relative to the hydrant butt because the reality is the only elevations that matter to us in this scenario is the elevation of the hydrant butt relative to the finished floor of the building.
As far as we are concerned the elevation of the pit with double check makes no difference... it could be 10' higher than the hydrant butt or 10' lower and it doesn't matter.
I've heard of some designers showing the tapping valve and sleeve 6' underground, which might place it 7' below the finished floor of the building, and then what they do is draw a pipe that doesn't exist from the tapping sleeve to the source which is at the same elevation of as the hydrant butt.
To me the proper fix would be to place the tapping sleeve at the same elevation as the hydrant butt which, in this case, would place the tapping sleeve 8.25' AFF and could easily be above the ground level where the tap actually is.
Yeah, I am just starting to learn AutoSprink and I am thinking there has to be a way to assign an elevation to the source node or blue ball.
I wonder what Travis does?
In the absence of a fire booster pump other than the finished floor of the building, which I always assign an elevation of 0.00 feet, the only elevation that I am concerned with is the elevation of the source node relative to the finished floor of the building.
The source elevation will be the elevation of the 2 1/2" hydrant butt where we obtained our static and residual pressures.
In the drawing below my source elevation is 8.25' above the finished floor of the building.
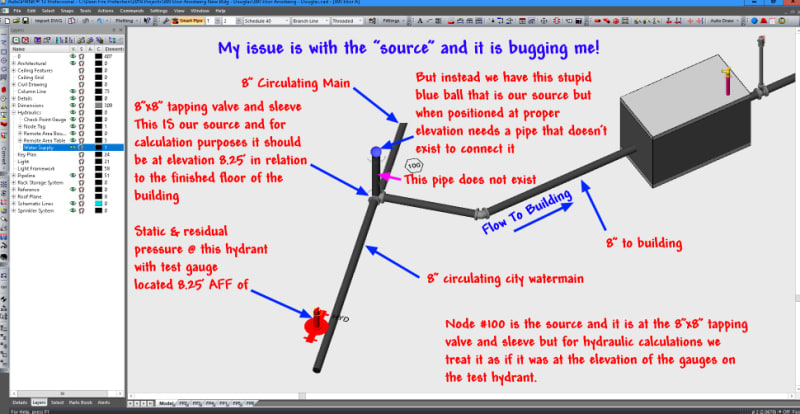
If this were a dead end main our source would be the hydrant tee assuming the flow from from the fire hydrant to the 8"x8" tapping sleeve. When calculating we would flow our water to the hydrant tee. We all know if it were a dead end main we would want to flow the hydrant downstream the tapping valve but, in this case, let's assume the hydrant shown is the last on the line. If the flow was the other direction, if the hydrant was downstream the tap, we would calculate to the tap.
Actually, if we wanted to get really technical if the hydrant was downstream the tap I would actually be able to add the friction loss developed between the hydrant and the tee but nobody does this.... well, I did once but I needed the extra pressure.
Anyway, assuming a circulating main my source node would be the tapping sleeve but the elevation of the sleeve wouldn't be 5' under the ground but would be the exact same elevation as the hydrant butt used to obtain static and residual pressures.
For our purposes once the source elevation is assigned to 8.25' AFF the calculations would be correct and it really doesn't matter how deep that tapping sleeve is because it doesn't have an impact. For all I are that tapping sleeve could be 100' under the ground relative to the hydrant butt because the reality is the only elevations that matter to us in this scenario is the elevation of the hydrant butt relative to the finished floor of the building.
As far as we are concerned the elevation of the pit with double check makes no difference... it could be 10' higher than the hydrant butt or 10' lower and it doesn't matter.
I've heard of some designers showing the tapping valve and sleeve 6' underground, which might place it 7' below the finished floor of the building, and then what they do is draw a pipe that doesn't exist from the tapping sleeve to the source which is at the same elevation of as the hydrant butt.
To me the proper fix would be to place the tapping sleeve at the same elevation as the hydrant butt which, in this case, would place the tapping sleeve 8.25' AFF and could easily be above the ground level where the tap actually is.
Yeah, I am just starting to learn AutoSprink and I am thinking there has to be a way to assign an elevation to the source node or blue ball.
I wonder what Travis does?