mechengineer
Mechanical
Link
I take the connection of shell to flat cover as an example to show my idea,
a) Considering the reinforcement effect at the transition connection by the thick cover, it requests that area B > area A, so that get the 'average stress' at the slope transition is not larger that the hoope stress in the cylinder wall.
b) the maximum longitudinal stress at the small end of the transition shall not be larger that the longitudinal stress at the cylinder wall (pr/4t).
If the above 'a' and 'b' are satidfied, I think that may allow the thcinkness at the small end of transition being smaller than cylinders shell thickness, but not more than 1/2 of cylinder thickness.
I take the connection of shell to flat cover as an example to show my idea,
a) Considering the reinforcement effect at the transition connection by the thick cover, it requests that area B > area A, so that get the 'average stress' at the slope transition is not larger that the hoope stress in the cylinder wall.
b) the maximum longitudinal stress at the small end of the transition shall not be larger that the longitudinal stress at the cylinder wall (pr/4t).
If the above 'a' and 'b' are satidfied, I think that may allow the thcinkness at the small end of transition being smaller than cylinders shell thickness, but not more than 1/2 of cylinder thickness.
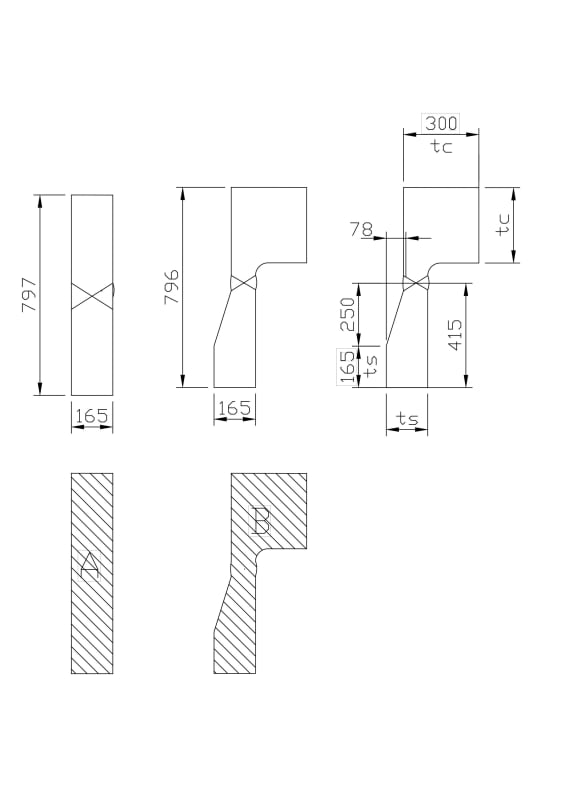