danschwind
Mechanical
Dear colleagues,
I am studying an issue for my client and I have stressed my ability to search any existing solution for it.
The issue:
My client owns hundreds (literally) of API 650 vertical storage tanks at various fuel terminals nation-wide (not USA!). As a premise, they are all fixed conical-roof.
Over time, dirt collects on the tank’s roof and whenever there is rain, this dirt drips on the tank’s shell and the tank’s get visibly dirty. This require constant maintenance by cleaning and increases the rate at which the tanks are repainted.
Their wish:
They requested me to find a solution in the form of a barrier for this rainwater to not be able to drip on the tank’s shell. They suggested some sort of gutter that would be installed on the transition of the shell and roof, something like this:
On existing tanks, it would be joined through some sort of cold welding to the shell, to avoid hot work. On future tanks they could be welded normally.
The problems I have identified:
As another premise, all the tanks have a cooling sprinkler ring (sorry if this has a more specific name that I am unaware of) on the top of the shell, as shown in the first picture. The gutter option may interfere with the functioning of those cooling sprinklers.
I then thought of something like this, which I named a “barrier”:
Which would also be joined through cold welding, albeit now to the roof.
My opinion:
I don’t like either solution. Both would retain some water that would slowly evaporate. The barrier would not be able to be installed right after the exit from the stairs, so it would only partially block the rainwater. The gutter may interfere with the sprinkler ring and would be really painful to install (there are many things extruding out of the tank’s circumference to interfere with the gutter) and would also interfere with the stair.
Tank Data:
Diameter: 5,73m to 19,10m
Height: 7,32m to 17,08m
Thickness of last shell plate: 1/4”
Thickness of roof: 3/16”
Fluids stored: Gasoline, Diesel, Ethanol, Water (fire fighting tank)
Reference for cleanliness:
My question:
Any of you guys saw or developed a solution for this? As I’ve said before, I’ve depleted my benchmarking capabilities and kind of come to a conclusion that this is either a “non-issue” for everyone else and therefore no one bothered to sort out or it is something that really has no feasible solution.
I am also not sure whether any of this would comply with API 650. I admit I haven’t read it entirely because, well, it’s huge. But I did an overall search for topics within the standard that would deny any accessory like this one and couldn’t find any.
By the way, I’m not worried about sizing the solution (i.e. the gutter size, the pipe diameter, etc), only the concept is important to me now.
If any of you guys has any thoughts on this, they are most welcomed and I thank you all in advance![[smile] [smile] [smile]](/data/assets/smilies/smile.gif)
I am studying an issue for my client and I have stressed my ability to search any existing solution for it.
The issue:
My client owns hundreds (literally) of API 650 vertical storage tanks at various fuel terminals nation-wide (not USA!). As a premise, they are all fixed conical-roof.
Over time, dirt collects on the tank’s roof and whenever there is rain, this dirt drips on the tank’s shell and the tank’s get visibly dirty. This require constant maintenance by cleaning and increases the rate at which the tanks are repainted.
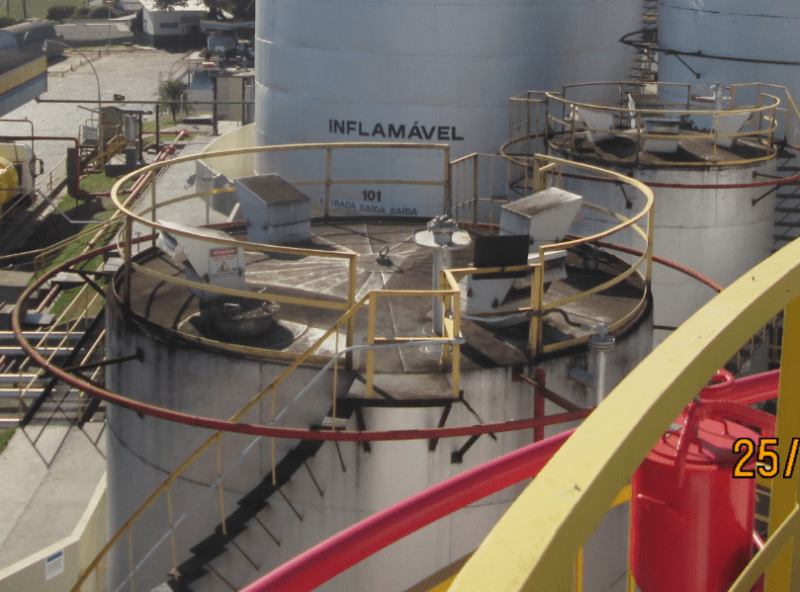
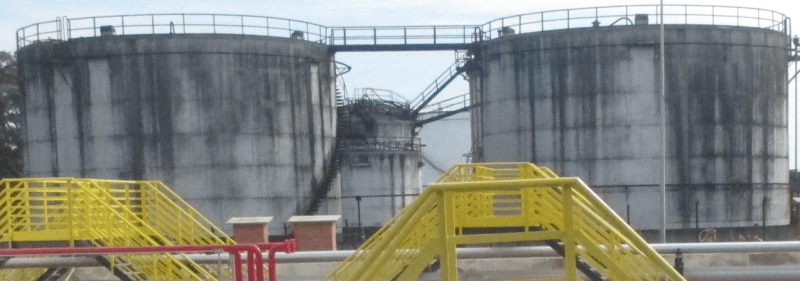
Their wish:
They requested me to find a solution in the form of a barrier for this rainwater to not be able to drip on the tank’s shell. They suggested some sort of gutter that would be installed on the transition of the shell and roof, something like this:
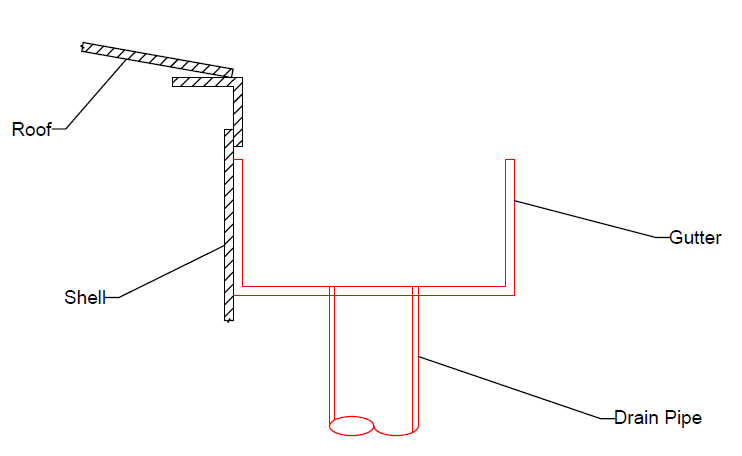
On existing tanks, it would be joined through some sort of cold welding to the shell, to avoid hot work. On future tanks they could be welded normally.
The problems I have identified:
As another premise, all the tanks have a cooling sprinkler ring (sorry if this has a more specific name that I am unaware of) on the top of the shell, as shown in the first picture. The gutter option may interfere with the functioning of those cooling sprinklers.
I then thought of something like this, which I named a “barrier”:
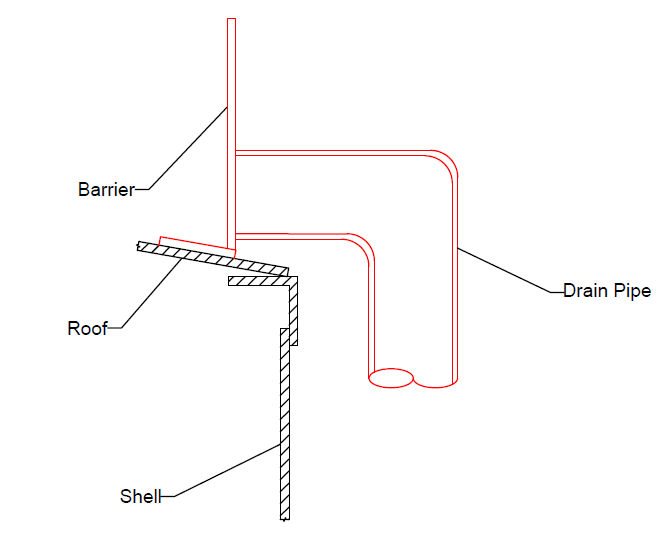
Which would also be joined through cold welding, albeit now to the roof.
My opinion:
I don’t like either solution. Both would retain some water that would slowly evaporate. The barrier would not be able to be installed right after the exit from the stairs, so it would only partially block the rainwater. The gutter may interfere with the sprinkler ring and would be really painful to install (there are many things extruding out of the tank’s circumference to interfere with the gutter) and would also interfere with the stair.
Tank Data:
Diameter: 5,73m to 19,10m
Height: 7,32m to 17,08m
Thickness of last shell plate: 1/4”
Thickness of roof: 3/16”
Fluids stored: Gasoline, Diesel, Ethanol, Water (fire fighting tank)
Reference for cleanliness:
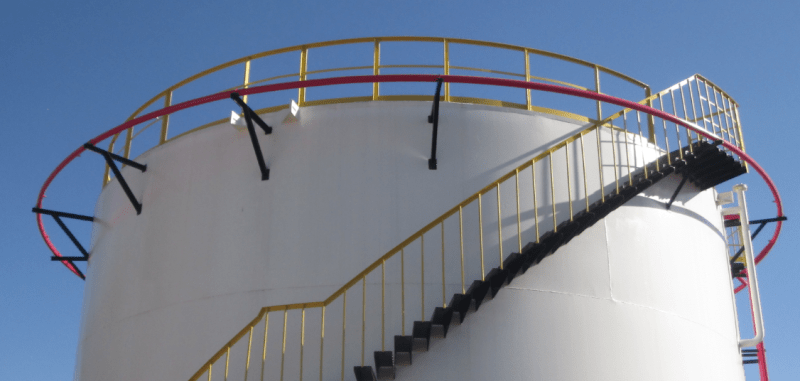
My question:
Any of you guys saw or developed a solution for this? As I’ve said before, I’ve depleted my benchmarking capabilities and kind of come to a conclusion that this is either a “non-issue” for everyone else and therefore no one bothered to sort out or it is something that really has no feasible solution.
I am also not sure whether any of this would comply with API 650. I admit I haven’t read it entirely because, well, it’s huge. But I did an overall search for topics within the standard that would deny any accessory like this one and couldn’t find any.
By the way, I’m not worried about sizing the solution (i.e. the gutter size, the pipe diameter, etc), only the concept is important to me now.
If any of you guys has any thoughts on this, they are most welcomed and I thank you all in advance
![[smile] [smile] [smile]](/data/assets/smilies/smile.gif)