MegaStructures
Structural
what is the best way to simulate a pinned joint on a solid model? I am analyzing a ball joint and need to set a constraint that will allow the solid to rotate, but not translate. If I set a pinned constraint by surface the solid will not be able to rotate. I would like to do this without using linear contact. Any help is appreciated.
Edit the image shown is an example only. The ball joint I have cannot be constrained on the shaft as it is part of a larger model and it needs to be constrained at the correct interface.
Edit the image shown is an example only. The ball joint I have cannot be constrained on the shaft as it is part of a larger model and it needs to be constrained at the correct interface.
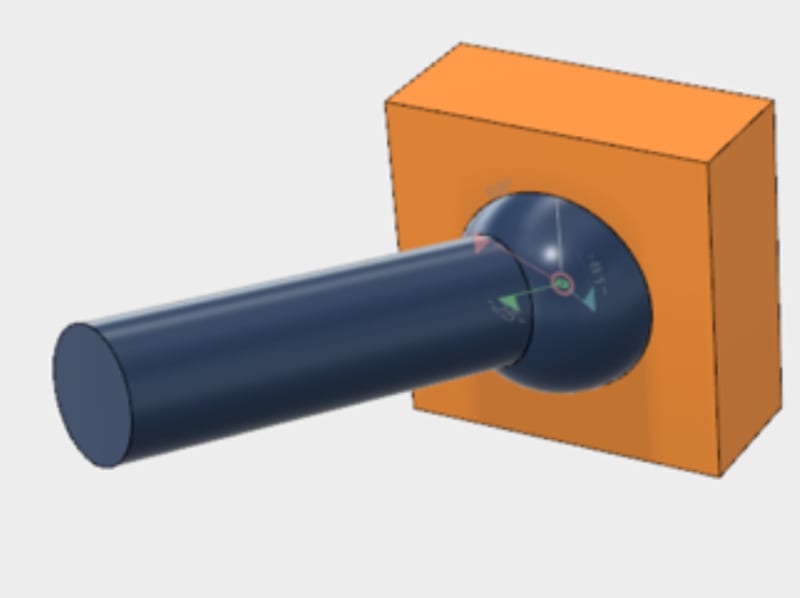