Hi all,
Trying to chase down design calculations for stress in a 'band' joining two pipe lengths together.
Stress in the weld.
Stress in the pipe (because its going to be in torsion as the load tries to pull the welds into the pipe)
The pipes are butted up to each other. The band is lap welded around the full circumference.
Pipe hangs vertically from the roof and supports a 1/2 ton load.
A cross section of it looks something like....
I told them to fully butt weld
Use a single piece
Or taper and weld
Think of a designer fireplace that hangs from the ceiling with no support at the base and you will get the idea.
They want what they want I guess.
I have a few figures down already but would like feedback on how others approach it, standard equations from reference material etc.
Thanks in advance!
Trying to chase down design calculations for stress in a 'band' joining two pipe lengths together.
Stress in the weld.
Stress in the pipe (because its going to be in torsion as the load tries to pull the welds into the pipe)
The pipes are butted up to each other. The band is lap welded around the full circumference.
Pipe hangs vertically from the roof and supports a 1/2 ton load.
A cross section of it looks something like....
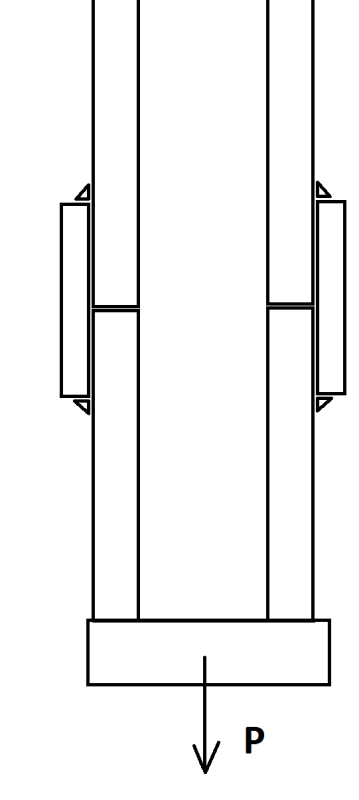
I told them to fully butt weld
Use a single piece
Or taper and weld
Think of a designer fireplace that hangs from the ceiling with no support at the base and you will get the idea.
They want what they want I guess.
I have a few figures down already but would like feedback on how others approach it, standard equations from reference material etc.
Thanks in advance!