Veer007
Civil/Environmental
- Sep 7, 2016
- 379
Hello guys, Please refer to the snap below, which option actually seems correct as I'm worried about beam slopes at the end if I weld a beam and cast-ins?
Thanks in advance!!
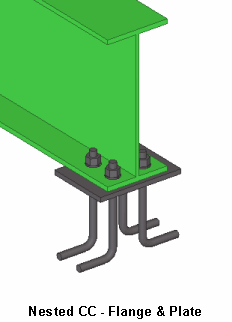
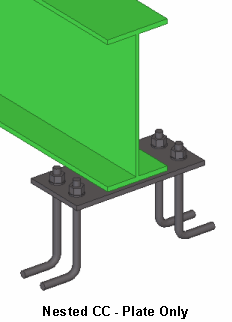
Thanks in advance!!