-
1
- #1
kingnero
Mechanical
- Aug 15, 2009
- 1,765
Saw this picture on a social media channel few days ago.
What is the middle bolt row (inbetween both C channels) for?
In europe, there are two kinds of C channels: with parallel and tapered flanges. Anybody cares to guess about those? I don't dare to tell from the pictures, but I don't see tapered washers...
What is the middle bolt row (inbetween both C channels) for?
In europe, there are two kinds of C channels: with parallel and tapered flanges. Anybody cares to guess about those? I don't dare to tell from the pictures, but I don't see tapered washers...
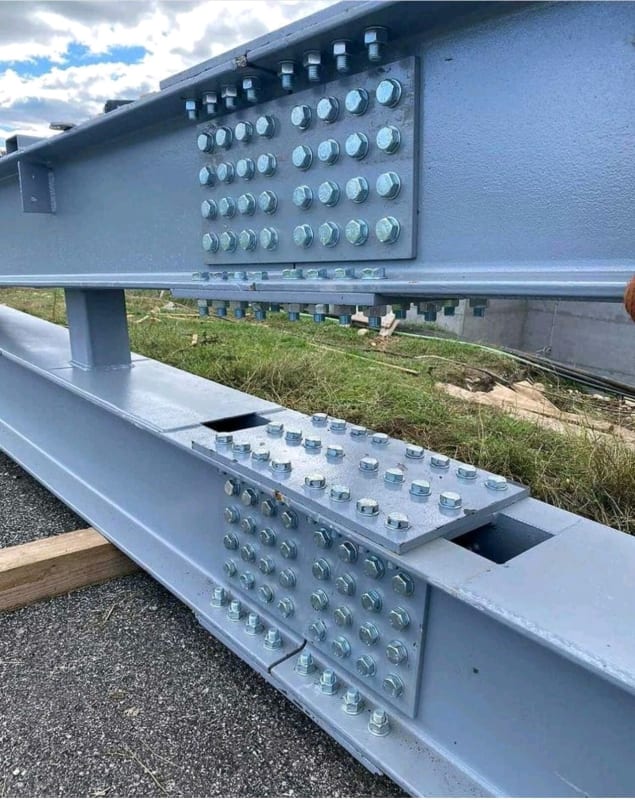