I'm trying to design a beam-thru-beam connection for a cantilevered canopy beam on the front of a building. I'm trying to frame a W4x13 (cantilever beam) and W10 into opposite sides of a W16x31 beam.
I've seen some similar connection detail approaches in a previous thread on here ( but my scenario is a little different with the beam locations relative to each other (due to where the architect wants the canopy and where the 2nd floor level is).
Is there any issue with me using end plates on each of the beams and doing a field bolted connection through the W16 and adding stiffener plates to the web of the W10 to match the flange of the W4 as shown in the attached sketch? In this case, I'm transferring tension forces frot the top flange of the W4 to the added web stiffener vs compression as shown in the above mentioned previous post.
I've seen some similar connection detail approaches in a previous thread on here ( but my scenario is a little different with the beam locations relative to each other (due to where the architect wants the canopy and where the 2nd floor level is).
Is there any issue with me using end plates on each of the beams and doing a field bolted connection through the W16 and adding stiffener plates to the web of the W10 to match the flange of the W4 as shown in the attached sketch? In this case, I'm transferring tension forces frot the top flange of the W4 to the added web stiffener vs compression as shown in the above mentioned previous post.
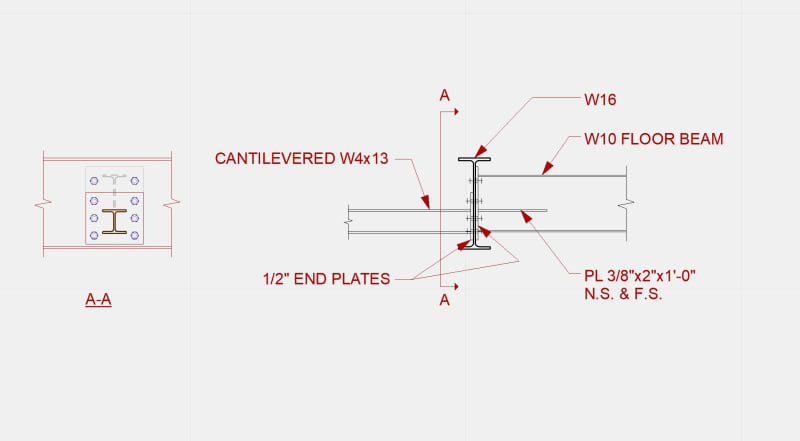