Hi community!
I'm designing a bearing housing for a pump (in reality this is not really a pump, but for simplicity, let's assume it's like a pump).
Inside the bearing housing there are a radial ball bearing (1 row) and a axial/radial ball bearing (2 raws), both with the same internal diameter, as in all generic pumps.
The level of the oil is maintained at half height of the lowest ball of the bearings.
The level of the oil is controlled with a constant oil leveler (Bull-eye from Mertens, it's the same as the watchdog): so the horizontal pipe connecting the bearing housing and the leveler is half filled, like in the following picture:
The bearing housing will have also 2 bearing isolators (type labtecta 66, from Aesseal).
After this description, here are my doubts:
I was reading this thread:
At the end of the discussion the user recommends to remove the breather, replace with a simple plug, and attach that type of oil leveler.
--------
However, when the oil gets hotter the bearing isolators will allow the air to go out of the housing;
when the pump shuts down air temperature will decrease inside the housing but bearing isolators will not allow the air to enter the housing from the outside (and this is ok if I want to prevent contamination): this will create a vacuum inside the bearing housing.
Look at the following picture:
The oil level will be in equilibrium when P1=P2+rho*g*h
rho = oil density (let's assume 800 kg/m3)
g = acceleration of gravity (9,81 m/s2)
So, let's say my air temperature reaches 70 °C when the pump is running, and I'm at atmospheric pressure (101325 Pa) (because the bearing isolators allow the air to go out): assuming h = 0,12 m:
P2 = 100383 Pa
Ok, now, let's shut down the pump, air temperature inside the bearing housing will decrease (let's say to 25 °C), but this time bearing isolators wont allow air to enter from the outside to compensate the pressure, so the bearing housing will be in vacuum.
Since P1 is lower now, (P2+rho*g*h) must decrease to have a new equilibrium, so oil level inside the leveler will decrease and oil will enter the bearing housing from the leveler reservoir, but this time there will be more oil inside the bearing housing that the perfect needed amount.
If I start up and shut down the pump n times the level inside the bearing housing will continue to grow (!!).
Is it right or am I missing something?
Does this mean that a breather (better, dust/humidity filter) is always necessary?
With a breather, pressure inside the bearing housing will be always atmospheric (regardless the temperature) and (in an ideal world, assuming no leakage) the oil level will be always perfect.
Thank you, I hope I was able to explain well my doubt.
Daniele
I'm designing a bearing housing for a pump (in reality this is not really a pump, but for simplicity, let's assume it's like a pump).
Inside the bearing housing there are a radial ball bearing (1 row) and a axial/radial ball bearing (2 raws), both with the same internal diameter, as in all generic pumps.
The level of the oil is maintained at half height of the lowest ball of the bearings.
The level of the oil is controlled with a constant oil leveler (Bull-eye from Mertens, it's the same as the watchdog): so the horizontal pipe connecting the bearing housing and the leveler is half filled, like in the following picture:
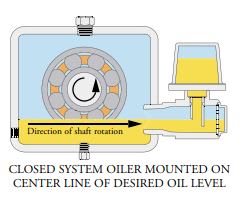
The bearing housing will have also 2 bearing isolators (type labtecta 66, from Aesseal).
After this description, here are my doubts:
I was reading this thread:
At the end of the discussion the user recommends to remove the breather, replace with a simple plug, and attach that type of oil leveler.
--------
However, when the oil gets hotter the bearing isolators will allow the air to go out of the housing;
when the pump shuts down air temperature will decrease inside the housing but bearing isolators will not allow the air to enter the housing from the outside (and this is ok if I want to prevent contamination): this will create a vacuum inside the bearing housing.
Look at the following picture:
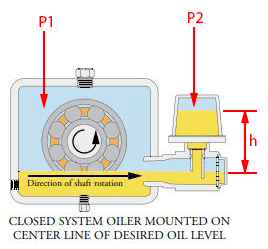
The oil level will be in equilibrium when P1=P2+rho*g*h
rho = oil density (let's assume 800 kg/m3)
g = acceleration of gravity (9,81 m/s2)
So, let's say my air temperature reaches 70 °C when the pump is running, and I'm at atmospheric pressure (101325 Pa) (because the bearing isolators allow the air to go out): assuming h = 0,12 m:
P2 = 100383 Pa
Ok, now, let's shut down the pump, air temperature inside the bearing housing will decrease (let's say to 25 °C), but this time bearing isolators wont allow air to enter from the outside to compensate the pressure, so the bearing housing will be in vacuum.
Since P1 is lower now, (P2+rho*g*h) must decrease to have a new equilibrium, so oil level inside the leveler will decrease and oil will enter the bearing housing from the leveler reservoir, but this time there will be more oil inside the bearing housing that the perfect needed amount.
If I start up and shut down the pump n times the level inside the bearing housing will continue to grow (!!).
Is it right or am I missing something?
Does this mean that a breather (better, dust/humidity filter) is always necessary?
With a breather, pressure inside the bearing housing will be always atmospheric (regardless the temperature) and (in an ideal world, assuming no leakage) the oil level will be always perfect.
Thank you, I hope I was able to explain well my doubt.
Daniele