I’m working on shear allowable strength for joints for a few combinations of fasteners and sheet materials. I want to use MMPDS as the main sours of data. Now I take data from MMPDS and draw a diagram. The diagram shows how shear allowable strength depends on a thickness of sheet material. This diagram is typical and can be easily found in lots of books. I put 4 points on the diagram, which are A B C D. Zone between points A and B are bearing critical zone. Zone CD is shear critical. This is clear. And zone between points B and C called transition zone.
Question 1. What kind of failure occurs in this transitional zone?
Question 2. Why the curve changes its inclination so rapidly at point B?
Question 1. What kind of failure occurs in this transitional zone?
Question 2. Why the curve changes its inclination so rapidly at point B?
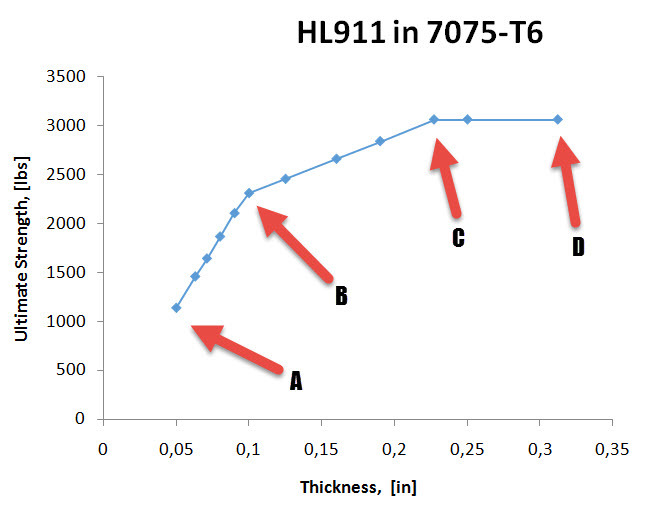