Hello everyone!
which tool would you use to extract this bearings? they are 6x19x6mm (brand NMB type 626s)
They are in a bldc motor from a vacuum cleaner which is soldered and there is no way to open the motor without breaking it.
As you can see there is no gap to attach claws from outside so it have to be removed from the inside between the small balls
i can't find such a small extractor anywhere please can you help me?
thank you
which tool would you use to extract this bearings? they are 6x19x6mm (brand NMB type 626s)
They are in a bldc motor from a vacuum cleaner which is soldered and there is no way to open the motor without breaking it.
As you can see there is no gap to attach claws from outside so it have to be removed from the inside between the small balls
i can't find such a small extractor anywhere please can you help me?
thank you
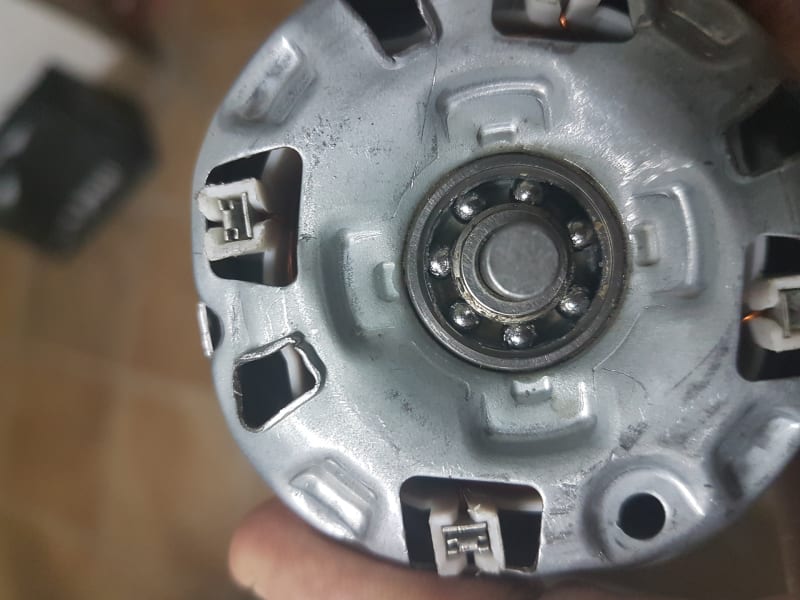
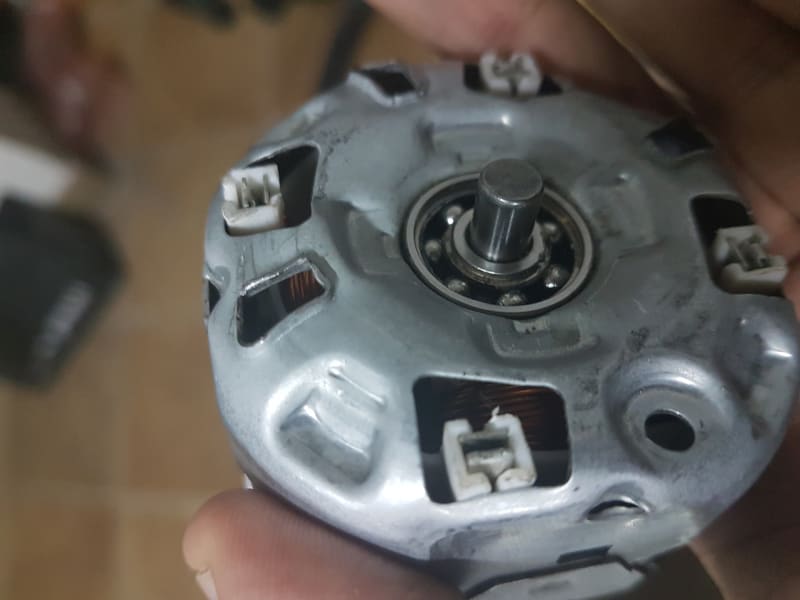