I ran across this beauty when searching for "modern rotary engine." It's specs are pretty darned close to the very popular Rotax 912/914 series engines used in light civil aviation applications: 2.8L, 110 HP @ 2450 RPM (implied 236 lb-ft torque), 220 LB dry weight, 31" diameter ( The $2,250 price is amazing and must be close to the cost of manufacture.
EDIT: As VE1BLL notes, $2250 is the down payment on the $22,500 total price. Duh.
A motorcycle using one of these engines would be a fun project! If nothing else, it would sound awesome (hear it at EDIT: It's been done, and makes it clear why Harley Davidson elected to use only two cylinders.
In case anyone is wondering, my own engine (a form of rotating cylinder radial) would have roughly the same specifications, but would have a diameter about 33% smaller, have lower emissions, and use a lot less fuel. Mine, however would not be nearly so beautiful to the eyes and ears. It's hard to beat the traditional rotary for looks and sound!
EDIT: As VE1BLL notes, $2250 is the down payment on the $22,500 total price. Duh.
A motorcycle using one of these engines would be a fun project! If nothing else, it would sound awesome (hear it at EDIT: It's been done, and makes it clear why Harley Davidson elected to use only two cylinders.
In case anyone is wondering, my own engine (a form of rotating cylinder radial) would have roughly the same specifications, but would have a diameter about 33% smaller, have lower emissions, and use a lot less fuel. Mine, however would not be nearly so beautiful to the eyes and ears. It's hard to beat the traditional rotary for looks and sound!
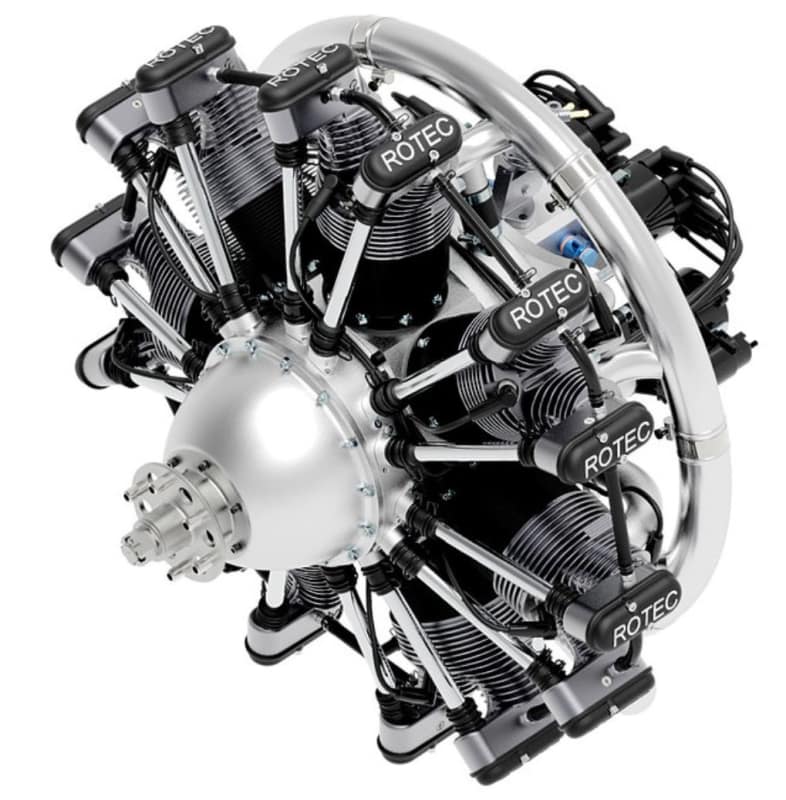
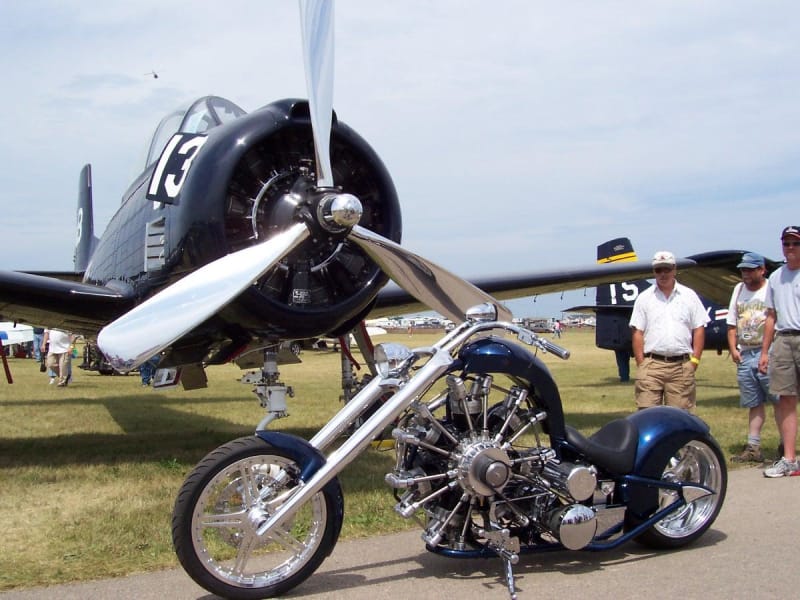