With the popularity of blade columns (wallums) with an aspect ratio over 1:4, I'd like to confirm the best way to deal with these in terms of punching shear.
At what point should you start deducting the shear going through the red hatch zone from the total punching shear (which will be assessed using the dashed shear perimeter)? It would be overly conservative to assume the total punching demand is going to be concentrated at the corners of a 2500mm x 300mm blade column.
From a purist point of view, I think you should then check each end of dashed shear perimeter separately as there may be one end receiving much more shear than the other. I know this is all heading towards the whole "...the slab will need to unzip to punch argument..."
At what point should you start deducting the shear going through the red hatch zone from the total punching shear (which will be assessed using the dashed shear perimeter)? It would be overly conservative to assume the total punching demand is going to be concentrated at the corners of a 2500mm x 300mm blade column.
From a purist point of view, I think you should then check each end of dashed shear perimeter separately as there may be one end receiving much more shear than the other. I know this is all heading towards the whole "...the slab will need to unzip to punch argument..."
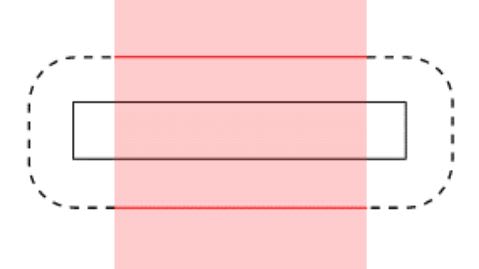