Howdy folks,
In my FEA, I am encountering a scenario in which the bolted-on assembly is experiencing lateral load due to vibrations (should be a screenshot). As the top box tips over, the bolt head essentially "digs in" on one side and pries at clamped material. The peak principal stresses are found near the edge of the bolt's contact. Would you expect this to be singular? In changing the density of the inflation region around the bolt hole, it for sure does NOT seem strongly mesh dependent (meaning I change the mesh and the results change by 5% at the most). Thoughts?
The bolt to plate contacts are all frictional. And, for clarity sake, I am dedicating a time step to applying the bolt clamp, and locking the bolt for the remaining steps.
In my FEA, I am encountering a scenario in which the bolted-on assembly is experiencing lateral load due to vibrations (should be a screenshot). As the top box tips over, the bolt head essentially "digs in" on one side and pries at clamped material. The peak principal stresses are found near the edge of the bolt's contact. Would you expect this to be singular? In changing the density of the inflation region around the bolt hole, it for sure does NOT seem strongly mesh dependent (meaning I change the mesh and the results change by 5% at the most). Thoughts?
The bolt to plate contacts are all frictional. And, for clarity sake, I am dedicating a time step to applying the bolt clamp, and locking the bolt for the remaining steps.
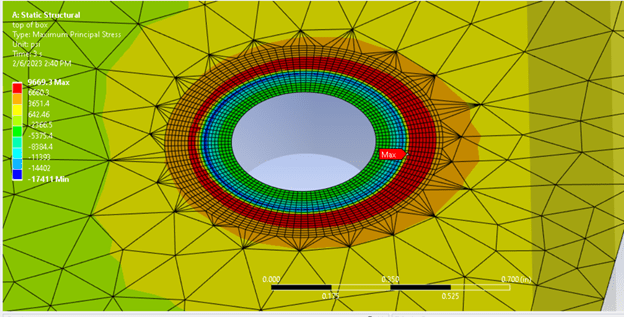
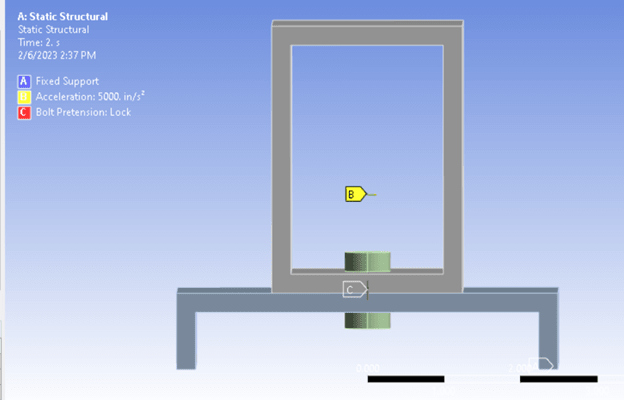