We have been building a simple coolant box that has two pipes going through it. One has an electric valve on it and one has a check valve. All the parts are brass. There are 4 brass 3/8 NPT female to female couplers, one on each end of each pipe. Early in the manufacture, we had returns due to (usually) one of the couplers splitting. They were not in service very long. We contacted the manufacturer to find out what they recommended for tightening. We had been using the standard recommended for NPT threads of that size, which is 2 to 3 turns from finger tight. We were surprised to find out the mfgr recommends 1 turn from finger tight. Ok, so we changed our method to that and we still see failures. Then we changed to a higher pressure rated fitting of the same type, still splitting. We changed to Loctite sealant instead of pipe tape, no change. Our customer says the coolant running in the system is just chilled water with some anti-fungal in it. We can't get an answer as to what exactly the anti-fungal is but I can say that it doesn't have any odor to it, thinking one of the things that attacks brass is ammonia. There are temperature swings but it is not more than 40F to 150F. The pressure is no more than 100psi. The other brass parts, the valve and the check valve are not splitting and have the same 3/8NPT female threads and are tightened to the same spec. Here is a pic of one of the split couplers
I sent two split couplers back to the manufacturer (distributor is not saying who the manufacturer is) and they said they have no opinion on why it's splitting other than we are doing something wrong or they are not being used appropriately. Very frustrating, we are not over tightening them or exposing them to anything they wouldn't see in most applications and we still have split couplers coming back. Any insight would be appreciated.
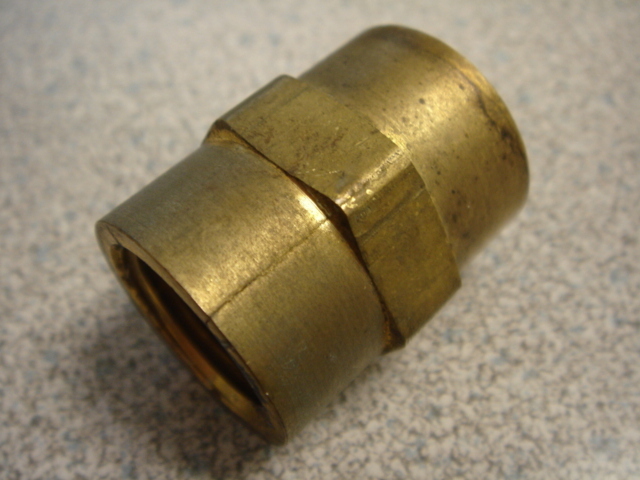
I sent two split couplers back to the manufacturer (distributor is not saying who the manufacturer is) and they said they have no opinion on why it's splitting other than we are doing something wrong or they are not being used appropriately. Very frustrating, we are not over tightening them or exposing them to anything they wouldn't see in most applications and we still have split couplers coming back. Any insight would be appreciated.