Ron247
Structural
- Jan 18, 2019
- 1,093
I have had several instances where I reduced the spacing for an overhang bracket because my hand calcs showed the controlling stress to occur in the cantilever of the horizontal arm from where the hanger rod connects and the joint of the horizontal to the vertical. The problem is that the load/spacing charts from most bracket suppliers indicates my reduction is excessive. My other problem is, it appears to be very simple calculation to confirm. This generally occurs when the concrete overhang is lower than the top of girder. The deeper the offset, the farther the rod moves.
I was wondering if maybe the joint of the horizonal and vertical is also supposed to move to the right with the movement of the rod connection to keep the cantilever somewhat the same. I have attached a drawing that I hope clarifies my issue. Am I missing something or incorrect about how the bracket works?
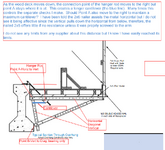
I was wondering if maybe the joint of the horizonal and vertical is also supposed to move to the right with the movement of the rod connection to keep the cantilever somewhat the same. I have attached a drawing that I hope clarifies my issue. Am I missing something or incorrect about how the bracket works?
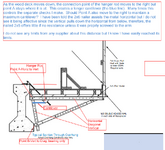