TugboatEng
Marine/Ocean
I have a carbon steel tube feeding a 4 piston recip pump, 65 psi to 40ksi. I experiencing extreme cavitation wear in the low pressure supply line. Short of putting an accumulator in the line, I'm looking for ideas to reduce the wear. Would replacing the problematic section with a harder material such as a hardened 400 stainless improve the resistance to damage? I usually move towards plastic or elastic coatings but I don't think they would be appropriate in this case.
~19mm OD. You can see the temporary repair.
Also, would adding ban accumulator to the line be a solution?
~19mm OD. You can see the temporary repair.
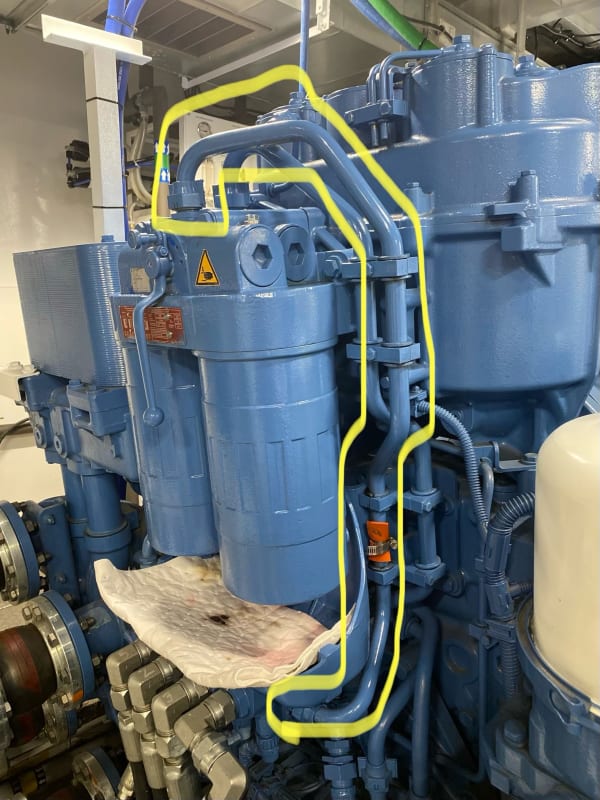
Also, would adding ban accumulator to the line be a solution?