tmalik3156
Structural
Good day all.
I am trying to understand the benefit of providing a longitudinal closure strip in bridge deck replacement work that is done in two stages. I have two examples in front of me.
Example 1: New deck on new steel girders. Even number of girders.
About 50% of the existing deck is removed and reconstructed (Stage 1). Then, the other 45% is removed and reconstructed (Stage 2). Finally, a closure strip of about 700 mm is poured.
Example 2: New deck on existing girders. Odd number of girders.
No closure pours. Each stage covers 50% of the width.
In both cases, traffic will continue on the opposite side of construction.
Can someone explain why closure pour was chosen in one case, but not in the other?
I am trying to understand the benefit of providing a longitudinal closure strip in bridge deck replacement work that is done in two stages. I have two examples in front of me.
Example 1: New deck on new steel girders. Even number of girders.
About 50% of the existing deck is removed and reconstructed (Stage 1). Then, the other 45% is removed and reconstructed (Stage 2). Finally, a closure strip of about 700 mm is poured.
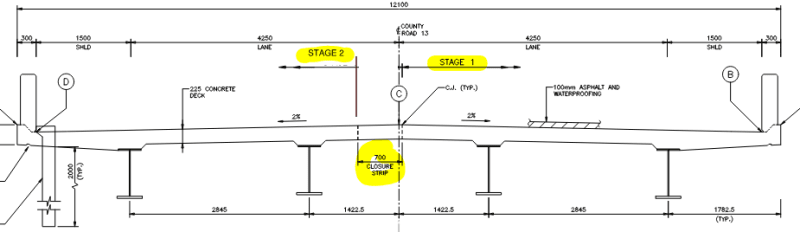
Example 2: New deck on existing girders. Odd number of girders.
No closure pours. Each stage covers 50% of the width.
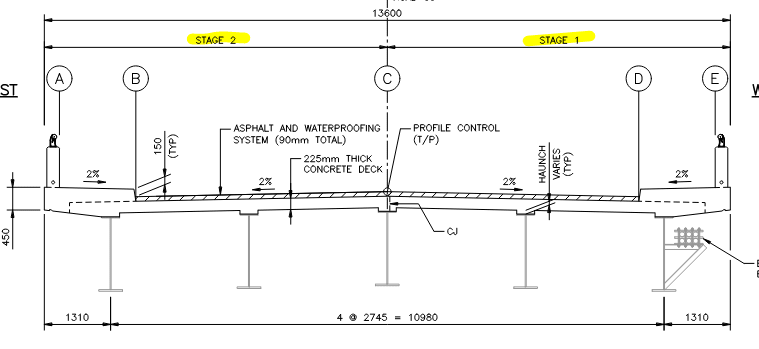
In both cases, traffic will continue on the opposite side of construction.
Can someone explain why closure pour was chosen in one case, but not in the other?