Hi,
I'm trying to design and make a Co2 vent valve which basically releases pressure from a larger pilot valve causing actuation. I am using the small 16g Co2 cartridges which provide 55 bar of pressure. My vent valve is basically the same as a direct acting pressure relief with a manual pull shank. I'm hoping i'll be able to trigger using a small 12vdc solenoid.
It consists of an alloy block, with a drilled 1mm orifice (see calculations below). Above this orifice sits a ball bearing, cupped shank, spring and bolt (see design attached). The idea being that the spring is set at just the right amount of compression to allow the shank to pulled up with minimal force. Co2 is vented through the loose hole in the bolt in which the shank sits.
@ 55 bar with 1mm orifice force against ball = 4.3 N.
Therefore with a spring force of 7 N I should be able to pull the shank with 2.7 N of force?
Can anyone confirm the calcs above are correct, and I'm on the right track here?
Many thanks,
Jim
I'm trying to design and make a Co2 vent valve which basically releases pressure from a larger pilot valve causing actuation. I am using the small 16g Co2 cartridges which provide 55 bar of pressure. My vent valve is basically the same as a direct acting pressure relief with a manual pull shank. I'm hoping i'll be able to trigger using a small 12vdc solenoid.
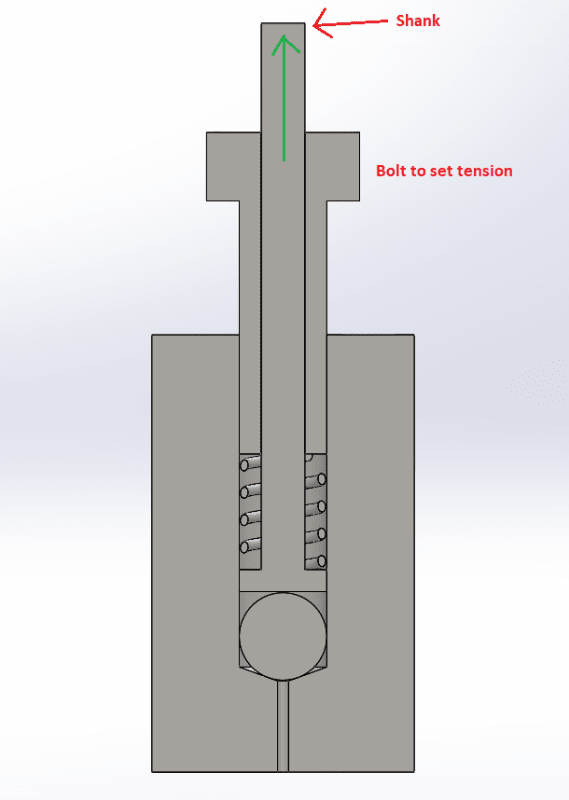
It consists of an alloy block, with a drilled 1mm orifice (see calculations below). Above this orifice sits a ball bearing, cupped shank, spring and bolt (see design attached). The idea being that the spring is set at just the right amount of compression to allow the shank to pulled up with minimal force. Co2 is vented through the loose hole in the bolt in which the shank sits.
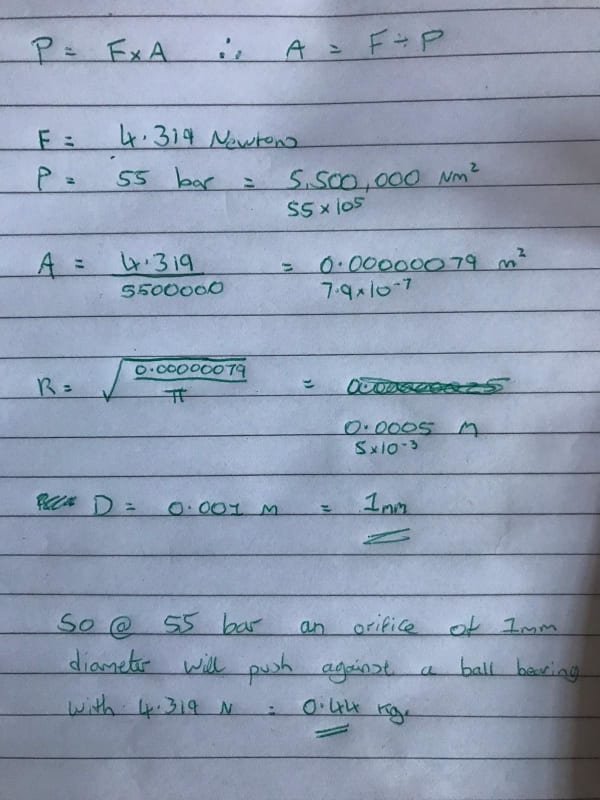
@ 55 bar with 1mm orifice force against ball = 4.3 N.
Therefore with a spring force of 7 N I should be able to pull the shank with 2.7 N of force?
Can anyone confirm the calcs above are correct, and I'm on the right track here?
Many thanks,
Jim