Jacob Falk
Civil/Environmental
I am trying to model a joint in Abaqus with a column and a beam, joined by a glued in rod. The job takes a long time to run and gives a lot of different warnings (see below). I think its maybe a fault in my interactions as it seems the rod is going through the column already at the first time increment. (Beam is hidden in picture for visibility)
I have tried making contact interactions between the elements and the glue and the elements and the bar. The column is encastre in the bottom, and a displacement is performed at the end of the beam.
Any help would be appreciated.
""
For *tie pair (assembly_s_surf-8-assembly_m_surf-8), not all the nodes that have been adjusted were printed. Specify *preprint,model=yes for complete printout.
For *tie pair (assembly_s_surf-8-assembly_m_surf-8), adjusted nodes with very small adjustments were not printed. Specify *preprint,model=yes for complete printout.
2346 nodes have been adjusted. The nodes have been identified in node set WarnNodeAdjust.
For *tie pair (assembly_s_surf-1-assembly_m_surf-1), not all the nodes that have been adjusted were printed. Specify *preprint,model=yes for complete printout.
For *tie pair (assembly_s_surf-1-assembly_m_surf-1), adjusted nodes with very small adjustments were not printed. Specify *preprint,model=yes for complete printout.
2346 nodes have been adjusted. The nodes have been identified in node set WarnNodeAdjust.
For *tie pair (assembly_s_surf-6-assembly_m_surf-6), not all the nodes that have been adjusted were printed. Specify *preprint,model=yes for complete printout.
For *tie pair (assembly_s_surf-6-assembly_m_surf-6), adjusted nodes with very small adjustments were not printed. Specify *preprint,model=yes for complete printout.
3162 nodes have been adjusted. The nodes have been identified in node set WarnNodeAdjust.
For *tie pair (assembly_s_surf-3-assembly_m_surf-3), not all the nodes that have been adjusted were printed. Specify *preprint,model=yes for complete printout.
For *tie pair (assembly_s_surf-3-assembly_m_surf-3), adjusted nodes with very small adjustments were not printed. Specify *preprint,model=yes for complete printout.
3162 nodes have been adjusted. The nodes have been identified in node set WarnNodeAdjust.
Strain output request le is not valid for some elements in this analysis. This request is switched to the strain measure, e.
Strain output request le is not valid for some elements in this analysis. This request is switched to the strain measure, e.
Strain output request le is not valid for some elements in this analysis. This request is switched to the strain measure, e.
Strain output request le is not valid for some elements in this analysis. This request is switched to the strain measure, e.
Strain output request le is not valid for some elements in this analysis. This request is switched to the strain measure, e.
Output request cf has been removed as there are no applicable loads in this step
Solver problem. Numerical singularity when processing node LIM-2.5580 D.O.F. 1 ratio = 452.449E+12 .
Solver problem. Numerical singularity when processing node LIM-2.5580 D.O.F. 2 ratio = 1.47036E+15.
Solver problem. Numerical singularity when processing node LIM-2.5579 D.O.F. 1 ratio = 1.43175E+15.
Solver problem. Numerical singularity when processing node LIM-2.5579 D.O.F. 2 ratio = 43.0556E+15 .
....
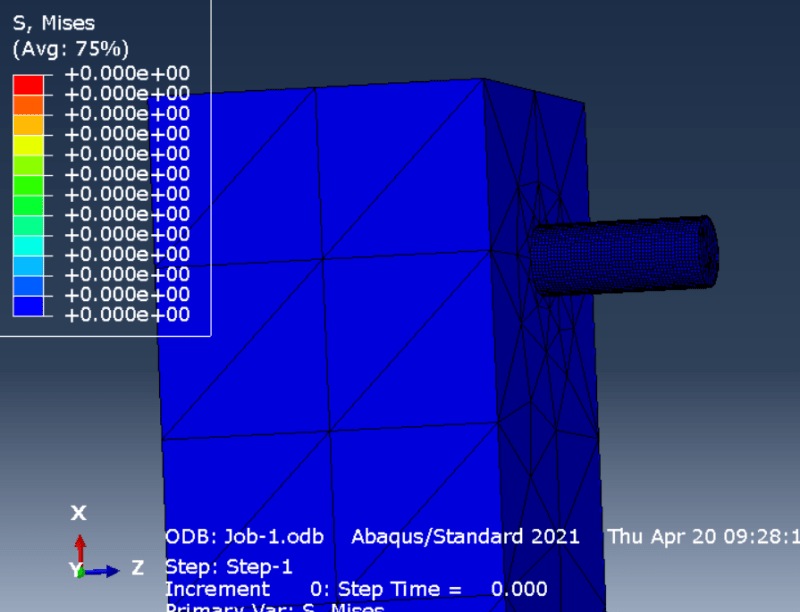
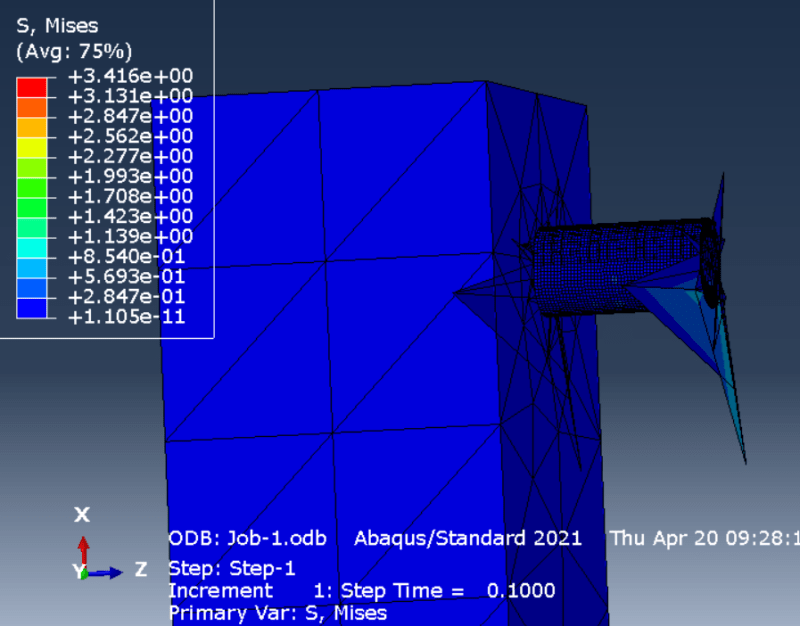
I have tried making contact interactions between the elements and the glue and the elements and the bar. The column is encastre in the bottom, and a displacement is performed at the end of the beam.
Any help would be appreciated.
""
For *tie pair (assembly_s_surf-8-assembly_m_surf-8), not all the nodes that have been adjusted were printed. Specify *preprint,model=yes for complete printout.
For *tie pair (assembly_s_surf-8-assembly_m_surf-8), adjusted nodes with very small adjustments were not printed. Specify *preprint,model=yes for complete printout.
2346 nodes have been adjusted. The nodes have been identified in node set WarnNodeAdjust.
For *tie pair (assembly_s_surf-1-assembly_m_surf-1), not all the nodes that have been adjusted were printed. Specify *preprint,model=yes for complete printout.
For *tie pair (assembly_s_surf-1-assembly_m_surf-1), adjusted nodes with very small adjustments were not printed. Specify *preprint,model=yes for complete printout.
2346 nodes have been adjusted. The nodes have been identified in node set WarnNodeAdjust.
For *tie pair (assembly_s_surf-6-assembly_m_surf-6), not all the nodes that have been adjusted were printed. Specify *preprint,model=yes for complete printout.
For *tie pair (assembly_s_surf-6-assembly_m_surf-6), adjusted nodes with very small adjustments were not printed. Specify *preprint,model=yes for complete printout.
3162 nodes have been adjusted. The nodes have been identified in node set WarnNodeAdjust.
For *tie pair (assembly_s_surf-3-assembly_m_surf-3), not all the nodes that have been adjusted were printed. Specify *preprint,model=yes for complete printout.
For *tie pair (assembly_s_surf-3-assembly_m_surf-3), adjusted nodes with very small adjustments were not printed. Specify *preprint,model=yes for complete printout.
3162 nodes have been adjusted. The nodes have been identified in node set WarnNodeAdjust.
Strain output request le is not valid for some elements in this analysis. This request is switched to the strain measure, e.
Strain output request le is not valid for some elements in this analysis. This request is switched to the strain measure, e.
Strain output request le is not valid for some elements in this analysis. This request is switched to the strain measure, e.
Strain output request le is not valid for some elements in this analysis. This request is switched to the strain measure, e.
Strain output request le is not valid for some elements in this analysis. This request is switched to the strain measure, e.
Output request cf has been removed as there are no applicable loads in this step
Solver problem. Numerical singularity when processing node LIM-2.5580 D.O.F. 1 ratio = 452.449E+12 .
Solver problem. Numerical singularity when processing node LIM-2.5580 D.O.F. 2 ratio = 1.47036E+15.
Solver problem. Numerical singularity when processing node LIM-2.5579 D.O.F. 1 ratio = 1.43175E+15.
Solver problem. Numerical singularity when processing node LIM-2.5579 D.O.F. 2 ratio = 43.0556E+15 .
....
""