sticksandtriangles
Structural
Hello,
I am designing a building where we are utilizing the Ecospan composite floor system as our main floor framing system.
This system will be bear on metal studs that are assumed to be spaced at 16"oc. As I understand the system, if studs and joists are not aligned in direct bearing, the top track must be designed for the pre-composite load of the floor system delivered to the track, before the load distribution member develops the ability to distribute load.
This is where I get a little lost in the cold form design process. Using the AISI 2012 specification I first check section C3.1.1 for flexural strength of the track. Seems pretty easy following procedure 1 - based on the initiation of yielding, basic M.n=(Section Modulus * Fy) stuff.
Then, am I also required to check individual elements of the track per section B2 of the specification? Specifically, the top of the track will be in compression which I am picturing as an element in uniform compression stiffened on both edges. The equations in in this section look pretty convoluted and I did not know if purely checking section C3 was sufficient to say that the track can resist the moment. Because the initial yielding is in tension, I need to calculate the effective section of the track, which upon looking up examples of calculating effective sections, looks very complicated too me.
Also, if this section B2 does apply, is there any software that can aide in these calculations? I have a good amount of software available to me, but none of the more general packages seem to have any good CFS design checks (SAP RAM Risa).
Thanks in advance for the help.
S&T
I am designing a building where we are utilizing the Ecospan composite floor system as our main floor framing system.
This system will be bear on metal studs that are assumed to be spaced at 16"oc. As I understand the system, if studs and joists are not aligned in direct bearing, the top track must be designed for the pre-composite load of the floor system delivered to the track, before the load distribution member develops the ability to distribute load.
This is where I get a little lost in the cold form design process. Using the AISI 2012 specification I first check section C3.1.1 for flexural strength of the track. Seems pretty easy following procedure 1 - based on the initiation of yielding, basic M.n=(Section Modulus * Fy) stuff.
Then, am I also required to check individual elements of the track per section B2 of the specification? Specifically, the top of the track will be in compression which I am picturing as an element in uniform compression stiffened on both edges. The equations in in this section look pretty convoluted and I did not know if purely checking section C3 was sufficient to say that the track can resist the moment. Because the initial yielding is in tension, I need to calculate the effective section of the track, which upon looking up examples of calculating effective sections, looks very complicated too me.
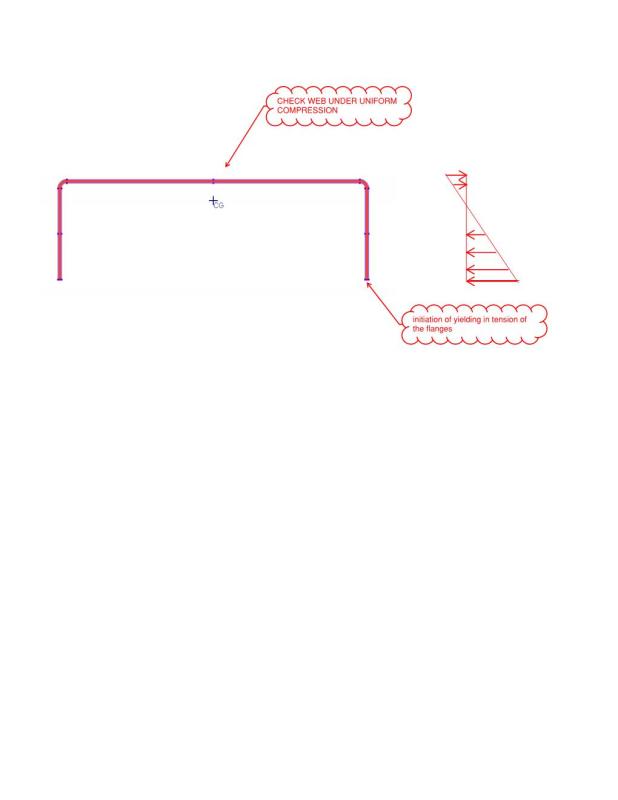
Also, if this section B2 does apply, is there any software that can aide in these calculations? I have a good amount of software available to me, but none of the more general packages seem to have any good CFS design checks (SAP RAM Risa).
Thanks in advance for the help.
S&T