AnupSebas10
Mechanical
I'm new to the forum. I was designing a beating mechanism which consists of 2 arms hitting a variable diameter stem of a plant. These arms are pulled back by the driving gear(s) and when released, slides with the spring force and hits the stem. When the driving gear reengages with the rack to pull it back and get ready for the next hit, there is a problem in meshing, the two teeth's top faces can hit each other and damage itself.
Is there any way to ensure proper engagement as the rack can be anywhere when the pinion engages?
Some design constraints:
1. Very limited space
2. One motor drives everything
3. no space on both sides of the gear.
4. No heavy loads (<2kg)
5. Motor rpm will be around 60rpm
Gear A drives gear B or vice versa. Both these gears drive 2 racks on either side of the gears. These racks are the beating arm which is spring-loaded. Do not mind the sprigs ends, it only for showing the spring position. The dimensions of the outer boundary are close to 220mm x 120mm
Is there any way to ensure proper engagement as the rack can be anywhere when the pinion engages?
Some design constraints:
1. Very limited space
2. One motor drives everything
3. no space on both sides of the gear.
4. No heavy loads (<2kg)
5. Motor rpm will be around 60rpm
Gear A drives gear B or vice versa. Both these gears drive 2 racks on either side of the gears. These racks are the beating arm which is spring-loaded. Do not mind the sprigs ends, it only for showing the spring position. The dimensions of the outer boundary are close to 220mm x 120mm
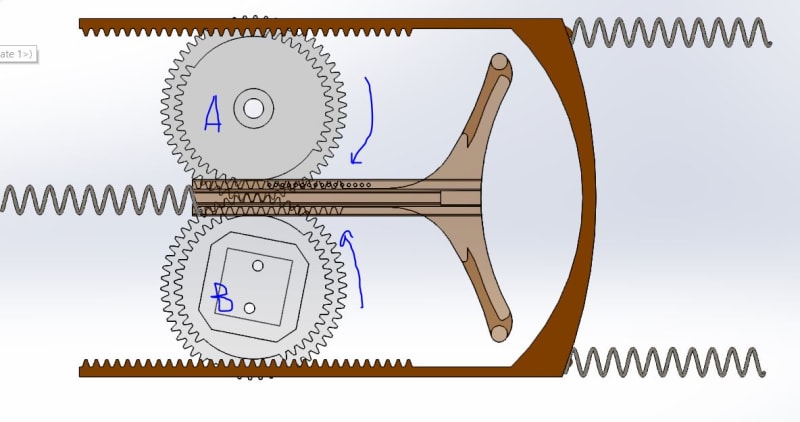
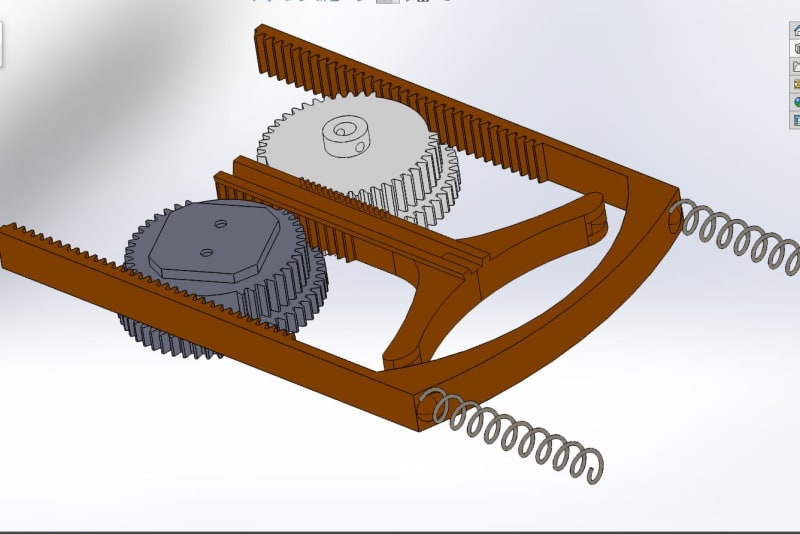
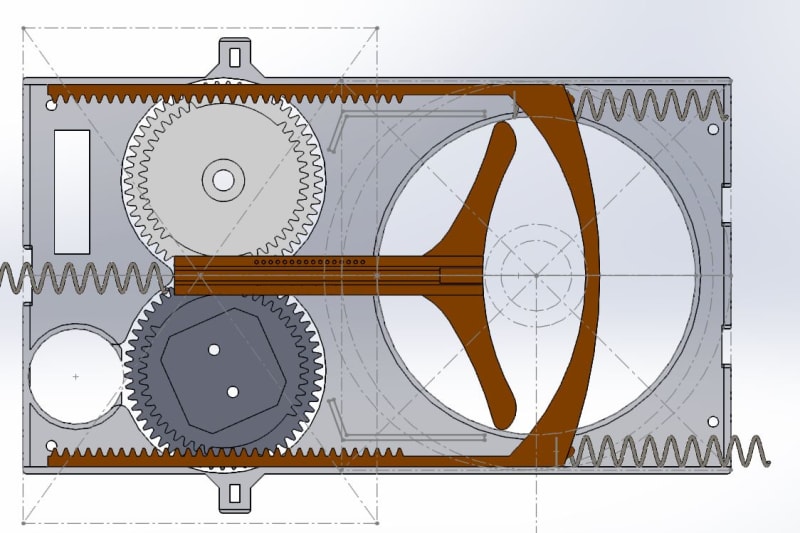
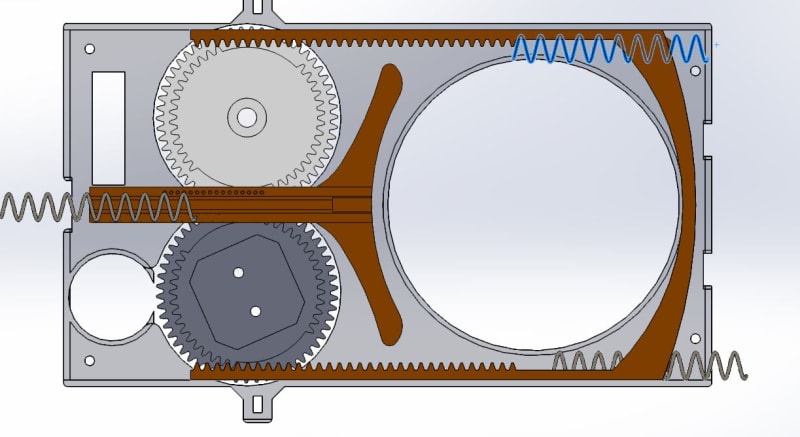
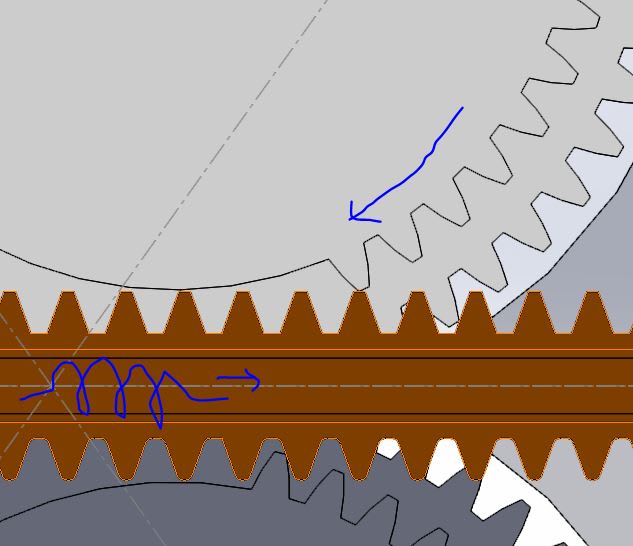