Celt83
Structural
- Sep 4, 2007
- 2,070
When determining the A2/A1 ratio is A2 based on a projection of the area in compression or a projection of the entire base/embed plate?
in attached image left is projection of base pl and right is projection of area in compression for a specific load set:
After reading the commentary in ACI 318-05,08,11 my interpretation is that A2/A1 should be based on the area in compression so the right setup in the above image.
My Personal Open Source Structural Applications:
Open Source Structural GitHub Group:
in attached image left is projection of base pl and right is projection of area in compression for a specific load set:
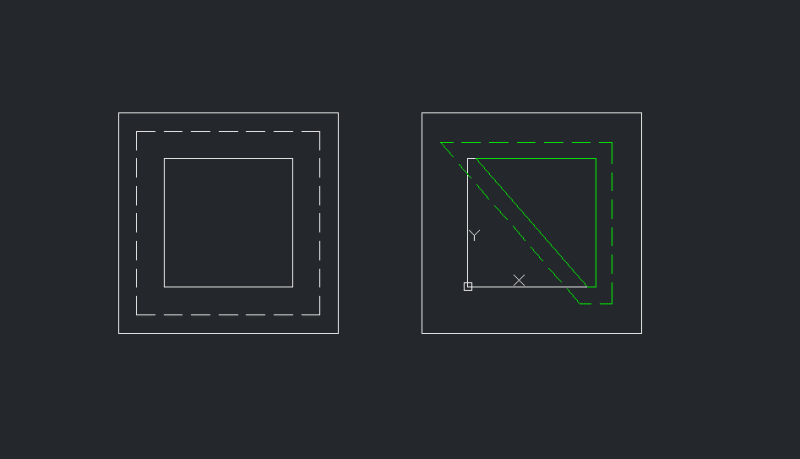
After reading the commentary in ACI 318-05,08,11 my interpretation is that A2/A1 should be based on the area in compression so the right setup in the above image.
My Personal Open Source Structural Applications:
Open Source Structural GitHub Group: