Redacted
Structural
- Mar 12, 2016
- 160
Hi there, I am going over a past problem and would like some clarity.
I recently designed a concrete jacket.
To simplify the problem. The top of an existing column was in poor condition. I have a lateral load applied to the column at the top (cantilever). I want to provide a transfer mechanism to transfer this load at the top to some of the sound concrete below. I want to figure out how to determine the spacing of the shear dowels I need to transfer the load.
See below (the blue square around the black square is the RC jacket)
The issue that I am realising is that because the neutral axis of the concrete jacket is the same as the neutral axis of the existing concrete, there wouldn’t be any shear flow in that location. So I don't think that I can calculate it like a normal shear flow problem.
I was looking into what was done for flitch beams as it seems like a similar problem and there wasn’t much guidance on the spacing when you have a concentrated load (it’s quite straightforward for a UDL), one document I was reading was pretty much saying try to have the dowels as close to the concentrated load as possible. Although this doesn't tell me much about the spacing.
I know the number of dowels required to take the load (18) but can’t have them all congested at the exact location of the load as there would be too many.
Does anyone have any advice or guidance for situations like this?
On a side note… Do you know of any good books or resources that discuss and provide concrete jacket design examples?
The only resources I can find are university research papers that only focus on one element of RC jacket design, which isn’t very helpful from a practical design point of view.
I recently designed a concrete jacket.
To simplify the problem. The top of an existing column was in poor condition. I have a lateral load applied to the column at the top (cantilever). I want to provide a transfer mechanism to transfer this load at the top to some of the sound concrete below. I want to figure out how to determine the spacing of the shear dowels I need to transfer the load.
See below (the blue square around the black square is the RC jacket)
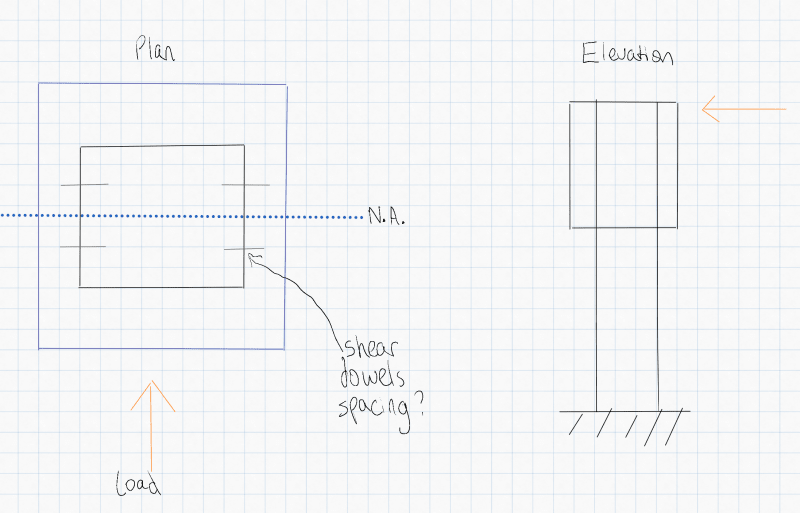
The issue that I am realising is that because the neutral axis of the concrete jacket is the same as the neutral axis of the existing concrete, there wouldn’t be any shear flow in that location. So I don't think that I can calculate it like a normal shear flow problem.
I was looking into what was done for flitch beams as it seems like a similar problem and there wasn’t much guidance on the spacing when you have a concentrated load (it’s quite straightforward for a UDL), one document I was reading was pretty much saying try to have the dowels as close to the concentrated load as possible. Although this doesn't tell me much about the spacing.
I know the number of dowels required to take the load (18) but can’t have them all congested at the exact location of the load as there would be too many.
Does anyone have any advice or guidance for situations like this?
On a side note… Do you know of any good books or resources that discuss and provide concrete jacket design examples?
The only resources I can find are university research papers that only focus on one element of RC jacket design, which isn’t very helpful from a practical design point of view.