I received field photos of a cantilever retaining wall we designed. From the photos, it is clear that the contractor installed the #5 "J-bar" with the leg pointed toward the heal instead of the toe. In addition, the J-bar appears to be attached to the top mat of rebar instead of 3" from the base of the footing.
The wall is now complete and backfilled. I am trying to give the owner (homeowner) some options beyond tearing down the wall. The contractor obviously messed up, but I don't see them being in business long enough to own up to rebuilding it.
Does anyone have some resources on how best to check this scenario or potential fixes?
The wall is now complete and backfilled. I am trying to give the owner (homeowner) some options beyond tearing down the wall. The contractor obviously messed up, but I don't see them being in business long enough to own up to rebuilding it.
Does anyone have some resources on how best to check this scenario or potential fixes?
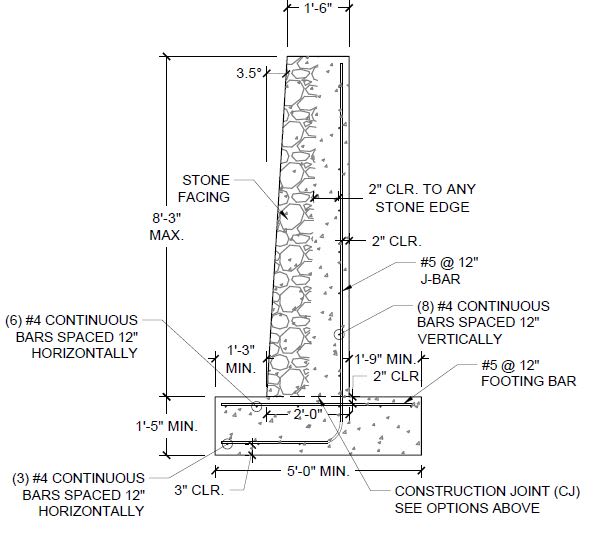
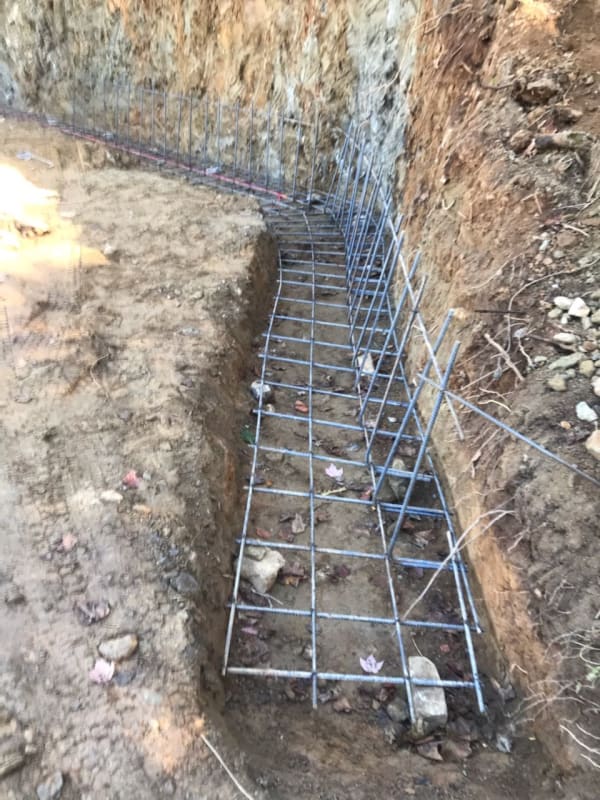