I'm sure this is very obvious to most, but for some reason, I have struggled to understand this. For calculating valve authority N=ΔPv/(ΔPv+ΔPc) where ΔPv is the pressure drop across the control valve when fully open, and ΔPc is the pressure drop across the circuit, what part of the hydronic system is ΔPc? Is it from the point where the branch taps off from the main? I am attaching a picture of my question with a sketch included.
In addition, if I have a hydronic piping network with multiple branches that further split off to other branches, are there other 'rules of thumb' control valve authority values that are useful? I am attaching a picture from a slide on this issue. This slide suggests that ΔPc is the pressure drop from the inlet of the branch to the outlet (return).
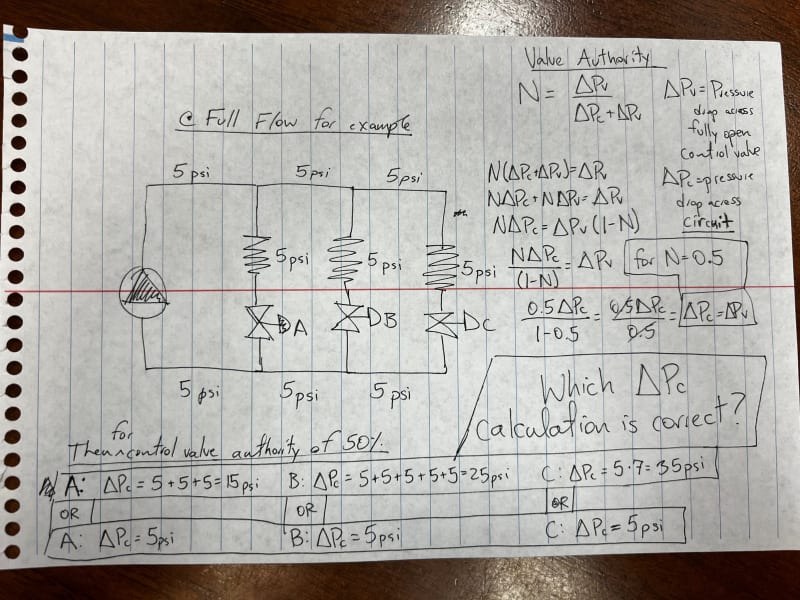
In addition, if I have a hydronic piping network with multiple branches that further split off to other branches, are there other 'rules of thumb' control valve authority values that are useful? I am attaching a picture from a slide on this issue. This slide suggests that ΔPc is the pressure drop from the inlet of the branch to the outlet (return).
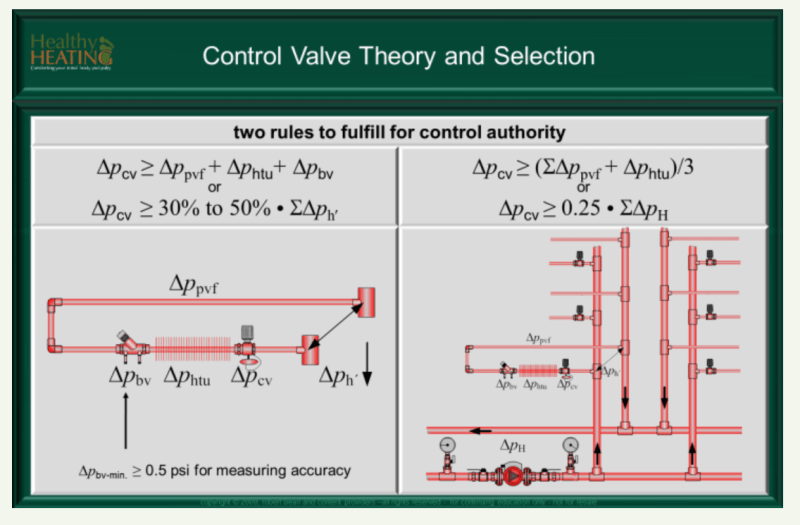